1. 서론
최근 2차원 박막형 소자 제작을 위한 공정 기술의 발달은 고성능 전자 소자 구현을 가능하게 하였다. 특히 유연성 및 신축성을 갖는 기판 위에 소자를 구현할 경우, 새로운 기능과 형태를 갖는 시스템을 제조할 수 있기 때문에 다양한 분야에서 관련 연구 개발이 진행되고 있다[1-3]. 즉, 이는 딱딱한 형태의 기판을 유연성 및 신축성을 가진 기판으로 대체할 경우, 많은 공학적 장점을 얻을 수 있다는 것을 의미한다.
이와 유사하게 2차원 형태를 갖는 유연 및 신축 소자를 3차원 구조로 구현할 경우 기존 소자로 구현할 수 없는 기능을 부여하거나, 소자의 전기적, 기계적, 광학적 성능을 크게 개선할 수 있다. 특히 3차원 구조를 갖는 경우, 2차원 형태를 갖는 유연 및 신축소자보다 일반적으로 향상된 기계적 물성을 갖기 때문에 소프트 일렉트로닉(soft electronics) 계열의 웨어러블 바이오 메디컬 소자(wearable biomedical devices)로 활용하는데 큰 장점이 있다[4-7]. 위와 같은 목적을 위해 3차원 구조를 갖는 유연 및 신축 소자를 제작하기 방법으로써 3차원 프린팅 공정(3D printing process), 오리가미 공정(origami process), 기계적 박리공정(mechanical buckling process)와 관련된 연구가 활발하게 진행되고 있는 상황이다. 이러한 제조 공정들을 활용하면 복잡한 3차원 구조를 손쉽게 제작할 수 있기 때문에, 새로운 폼팩터(form factor)를 기반으로 향상된 성능 및 다양한 응용 분야를 갖는 유연 및 신축 소자를 제조할 수 있다[8-15].
본 총설에서는 기존 2차원 박막형 구조를 갖는 유연 및 신축 소자에 3차원 구조를 도입한 최신 연구 결과들에 대해서 소개하고자 한다. 구체적으로 (i) 센서 소자(sensors), (ii) 바이오 메디컬 소자(biomedical devices), (iii) 에너지 소자(energy devices), (iv) 광학 소자(optical devices) 분야에서 3차원 형태로 구현된 차세대 유연 및 신축 소자가 갖는 특징과 장점에 대해서 순서대로 다루어 볼 것이다(Fig. 1) [16-19].
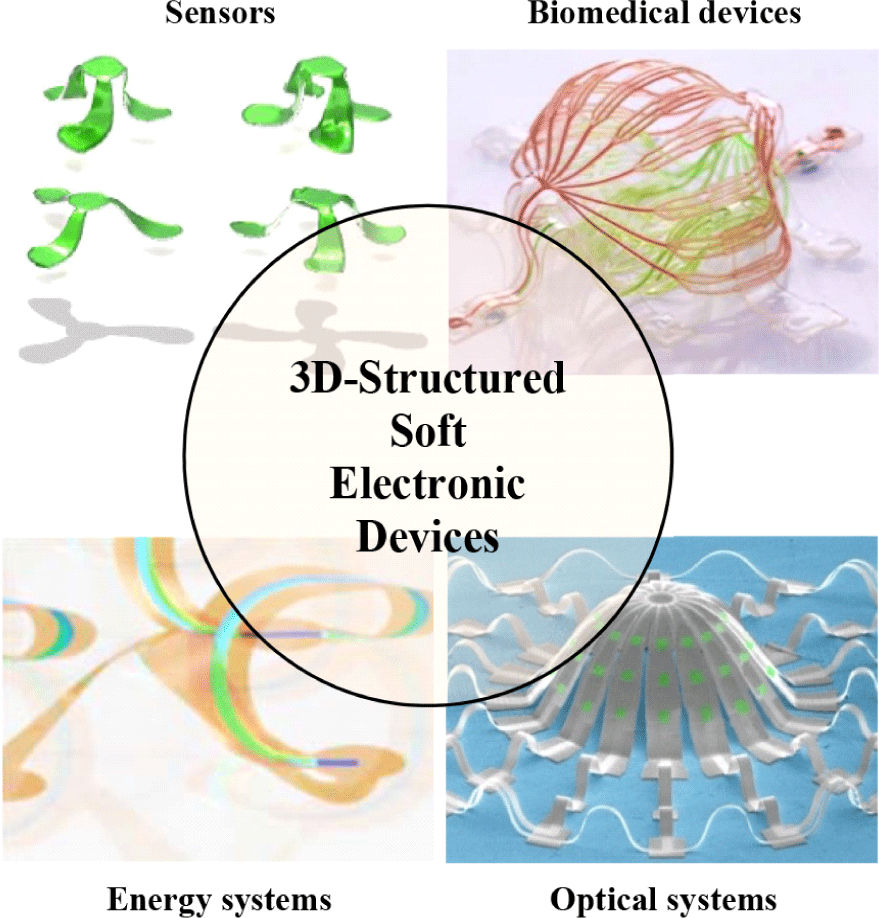
2. 본론
외부 자극을 측정하는 센서 분야는 유연 및 신축 소자와 관련된 연구가 활발하게 진행되고 있는 대표적인 연구 분야이다. 특히 3차원 구조를 갖는 유연 및 신축 센서 소자는 기존의 2차원 형태의 박막형 소자가 측정할 수 없는 물리적 또는 화학적 신호를 형태적 차별점을 이용해서 측정할 수 있다는 것을 보여주는 실험 결과가 최근 발표되고 있다.
Fig. 2(a)는 3차원 구조를 활용하여 수직 압력(normal pressure)과 전단력(shear force)과 같은 다양한 외부 힘을 독립적으로 동시에 측정할 수 있는 유연 및 신축 센서 소자의 연구 결과이다[20]. 3차원 테이블 구조가 외부 힘에 의해서 입체적으로 변형되면 테이블의 다리 부분에 삽입되어 있는 단결정 실리콘(monocrystalline silicon)에 변형의 종류에 따라 각기 다른 저항 변화가 발생되어, 서로 다른 방향으로 발생된 기계적 자극을 구분하여 측정할 수 있는 센서 소자 구현이 가능하다. 이는 기존 2차원 형태의 박막형 소자는 한 종류의 외부 자극을 측정할 수 있다는 한계점을 극복해 다중모드(multimodal) 측정이 가능한 3차원 유연 및 신축 센서 제작을 보여준 연구 결과이다. 이 소자는 미리 늘려놓은 실리콘 탄성체(silicone elastomer) 기판에 마이크로 펩 공정을 통해 제작된 2차원 형태의 전구체(precursor)를 전사 인쇄(transfer printing)하는 기계적 박리공정(mechanical buckling process)을 통해 제작되었으며, 2차원 구조와 3차원 구조의 변형이 가역적이라는 점에서 차별화된 장점을 갖는다(Fig. 2(b)). Fig. 2(c)는 압력이 가해졌을 때 소자의 저항 변화를 보여주고 있으며, 밀리초 단위로 외부 힘 유무에 따른 저항 변화가 측정된 결과에서 소자의 응답 속도가 매우 짧은 센서임을 알 수 있다. 위처럼 3차원 구조를 갖는 유연성 및 신축성을 갖는 센서 소자의 경우, 일반적인 2차원 형태의 박막형 센서 소자와 다르게 다양한 외부 자극을 동시에 측정할 수 있다는 장점을 갖는다.
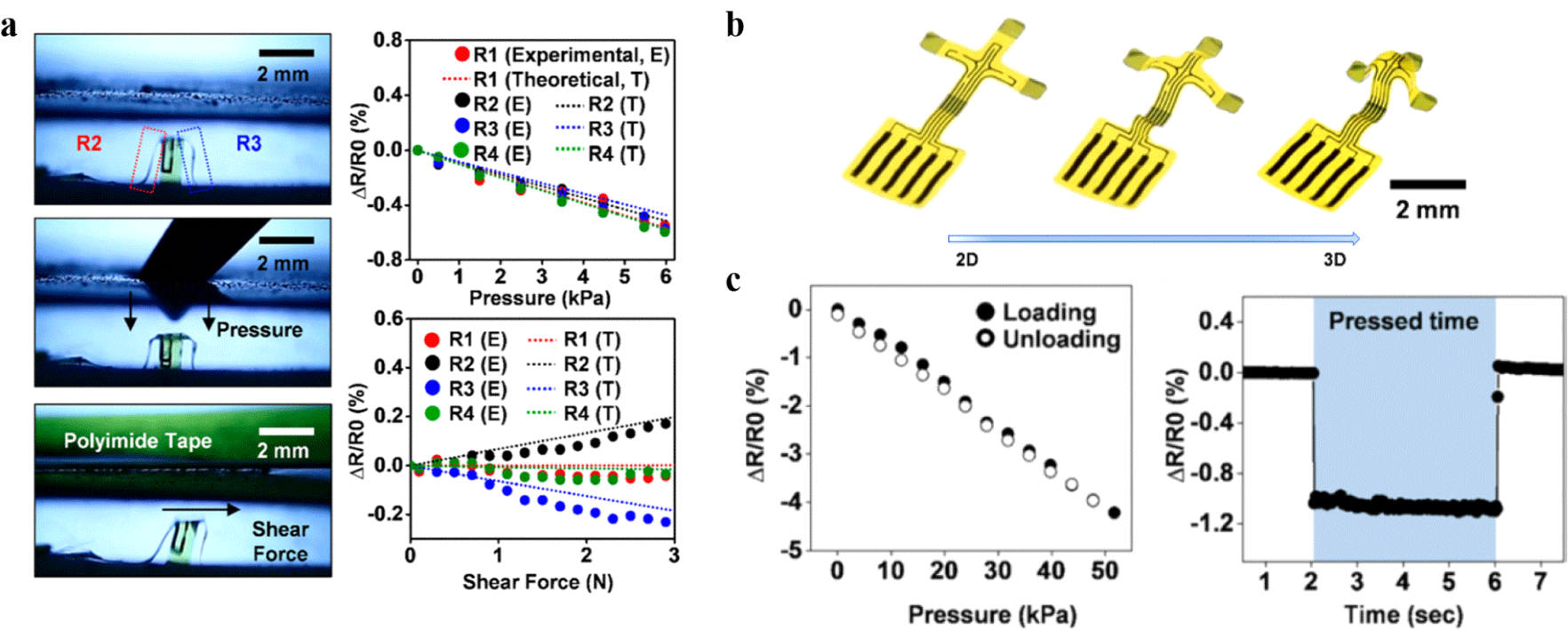
메디컬 소자가 피부 혹은 인체 조직과의 완벽한 접촉(conformal contact)을 통해 바이오 신호를 정밀하게 측정하기 위해서는 신체 변형이 발생하는 경우에도 안정적인 소자 동작을 보장하는 유연성과 신축성이 필수적이다. 기존의 2차원 형태를 갖는 유연 및 신축 바이오 메디컬 소자에 3차원 구조를 도입할 경우, 복잡한 구조의 특징을 활용하여 생체 신호를 정밀하고 지속적으로 측정할 수 있기 때문에 차세대 바이오 메디컬 소자로써 큰 잠재력을 갖는다.
Fig. 3은 3차원 다공성 실리콘 탄성체를 사용하여 최대 75%의 변형률을 갖는 웨어러블 바이오 메디컬 소자와 관련된 연구 결과를 보여주고 있다[21]. 본 연구 논문에서는 다공성 실리콘 탄성체 소자가 3차원 구조를 갖는다는 특징을 이용하여 구부림(bending)과 신축(stretching)과 같은 기계적 변형을 저항 변화를 통해서 정밀하게 측정할 수 있고, 특히 구부림과 신축이 혼합된 복잡한 기계적 변형이 발생한 경우에도 외부 힘들을 종류별로 독립적으로 분석할 수 있다(Fig. 3(a)).
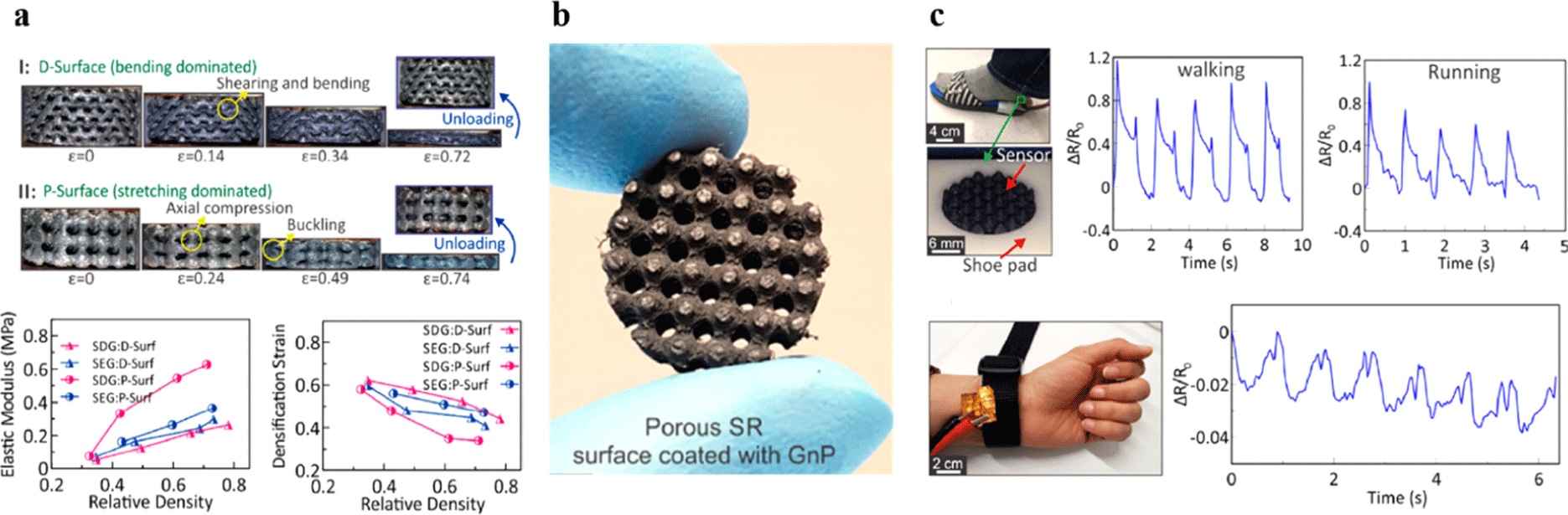
본 연구에서는 3차원 프린팅 공정을 통해 제작된 다공성 실리콘 고무(porous silicone rubber)에 딥 코팅 공정(dip-coating process)을 사용하여 표면에 그래핀(graphene)을 코팅함으로써 높은 전도성을 갖는 3차원 구조체를 구현하였다(Fig. 3(b)).
본 연구에서 보고된 3차원 바이오 메디컬 소자는 극단적인 기계적 변형과 높은 온도에서 안정적인 저항 변화를 보여주었고, 압축 변형률 조절을 통해 소자의 민감도를 조절할 수 있기 때문에, 맥박에 의한 작은 변형부터 걷기와 뛰기 같은 큰 변형까지 지속적으로 측정이 가능하였다(Fig. 3(c)). 이는 3차원 바이오 메디컬 소자의 활용 목적에 따라 외부 자극에 의한 변형 범위를 자유롭게 설정할 수 있으며, 장시간 동안 안정적으로 생체 신호를 측정하는 것이 가능함을 보여주는 연구 결과이다. 특히 3차원 구조를 갖는 유연 및 신축 소자를 인체 후두부 또는 가슴에 부착할 경우, 지속적인 호흡 신호 모니터링을 통해 COVID-19 확진자의 생체 신호를 측정하는 실험 결과, 역시 최근 보고된 바 있다[22].
덧붙여 세포 배양용 지지체 제작 및 응용을 위한 바이오 연구 분야에서는 단순한 와이어 구조 혹은 마이크로/나노 패턴을 가진 기존의 2차원 기판을 대신하여 복잡한 3차원 구조를 사용하려는 경향이 커지고 있으며, 이를 위해 다양한 형태와 스케일을 갖는 3차원 입체 구조 제조 공정이 세포 배양용 지지체 제작 및 응용 연구에 활용되고 있다. 특히 기계적 박리공정을 통해 제작된 3차원 지지체의 연구 결과는 스페로이드(spheroid)/오가노이드(organoid)를 입체 구조에 고정시킬 수 있는 기능과 지지체 내부에 전자 소자를 삽입시켜 다중모드 측정을 가능하게 하는 성능을 보였다. Fig. 4(a)는 다기능성 메소 스케일 프레임워크(multifunctional mesoscale frameworks, MMF)를 이용해 스페로이드를 감싸 고정한 광학 이미지과 시뮬레이션 결과이다. Fig. 4(b)는 기판을 인장 시켜 열린 구조를 만들어 스페로이드를 고정시키지 않은 실험 결과를 보여준다. 이는 기계적으로 최적화된 3차원 구조체를 매우 적은 힘으로 조직 계면에 접촉시켜 표면 손상 없이 스페로이드에 기계적 안정성을 부여했고, 가역적으로 스페로이드를 삽입 혹은 제거할 수 있는 성능을 보였다. Fig. 4(c)는 MMF에 삽입된 광학, 열 소자, 외부 장비와 연결된 electrodes/electrochemical sensors의 모식도이다. 기계적 박리 공정을 이용해 제작된 3차원 구조는 스페로이드에 메탈 인터커넥터(metal interconnector) 를 직접적으로 접촉시켜도 파괴되지 않아, 삽입된 센서들을 통한 비파괴 형식의 물성 측정을 가능케 했다. Fig. 4(d)는 스페로이드에 전압(0∼50 mV)를 인가한 후 메탈 인터커넥터를 통한 전기적 자극의 응답을 분석한 결과이다. 이 실험 결과를 통해 3차원 소자가 메소 스케일의 스페로이드의 electroencephalography(EEG) 를 분석할 수 있음을 확인했고, 특히 MMF에 삽입된 24개의 전극을 통해 전기 자극에 대한 응답의 크기를 분석해, 외부 자극에 대한 응답을 공간적으로 분석할 수 있음을 확인했다. Fig. 4(e)는 삽입된 마이크로 light emitting diode(LED)와 열 액추에이터(thermal actuator)를 통해 외부 자극을 생성한 후, 빛과 열에 대한 스페로이드의 응답을 분석한 결과이다. 이 실험 결과는 외부 자극에 응답으로 발생한 field potential을 3차원 메탈 인터커넥터를 통해 추적하여 외부 스트레스(빛, 열)가 스페로이드에 가해지는 위치를 알 수 있을 뿐만 아니라, 외부 자극에 대한 스페로이드의 반응을 실시간으로 측정할 수 있는 성능을 보였다[23]. 이는 기존의 2차원 형태의 박막형 지지체가 가질 수 없는 기계적 안정성과 다기능성을 3차 원 MMF를 통해 구현한 결과와 기계적 박리 공정으로 제작된 입체 구조가 차세대 세포 배양 및 물성 측정 플랫폼으로써 사용될 수 있음을 보여준다.
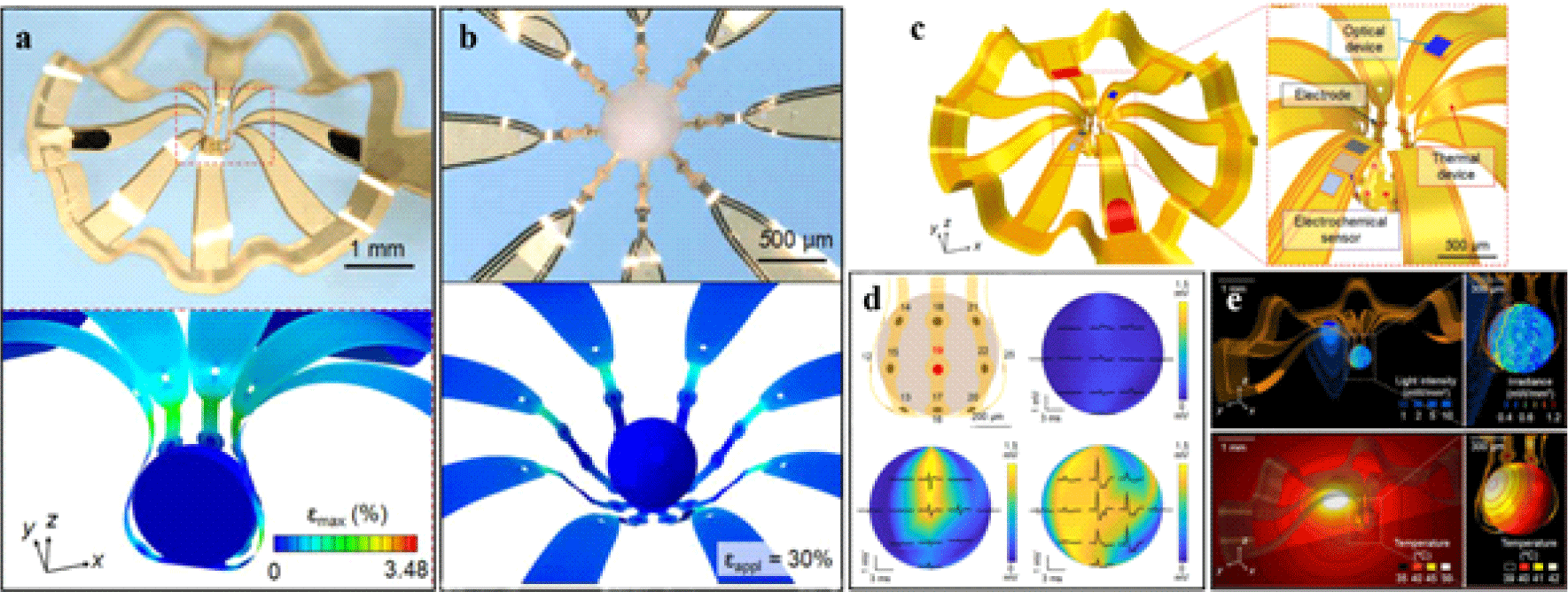
에너지 하베스팅(energy harvesting) 연구 분야는 에너지 재활용 기술 및 고성능 전자소자 동작에 필요한 에너지 저장 기술 수요 증대에 따라 현재 많은 연구 개발이 이루어지고 있다. 특히 무선 전원 공급이 필요한 웨어러블 사물인터넷 시스템 또는 센서 소자가 외부 에너지 공급 없이 지속적인 소자 구동을 하려면 유연성과 신축성을 갖춘 에너지 하베스팅 시스템이 필수적이다.
Fig. 5는 사물인터넷 시스템에 적용하기 위해 오리가미 공정을 통해 대면적으로 제작된 유연성 및 신축성을 갖춘 3차원 열전 발전기(thermoelectric generator, TEG)의 연구결과를 보여주고 있다[24]. 효율적인 TEG 제작을 위해서 유연 기판에 고분자(poly(3,4ethylenedioxythiophene, PEDOT)/TiS2) 재료를 스크린 프린팅(screen printing process)하는 방식으로 대면적/저비용 소자를 제작하였다(Fig. 5(a)). 오리가미 공정을 통해 3차원 구조로 구현된 TEG 소자는 가역적인 2차원 및 3차원 구조 변환을 통해 우수한 기계적 안정성을 가지게 되었으며(Fig. 5(b)), 박막형 열전소자에 비해 같은 면적 대비 높은 열전대(thermocouple) 밀도(cm2당 190개 열전대)를 보유함으로써 30 K의 온도차에서 최대 47.8 μW/cm2의 열전 효율을 보여주었다(Fig. 5(c)). 이와 같은 3차원 TEG 소자의 경우 손쉽게 대면적으로 제조할 수 있기 때문에, 외부에서 동작하는 날씨 측정용 전자 시스템의 에너지 공급을 위해 사용되거나, 실내에서 동작하는 블루투스 플랫폼과 함께 무선 소자 시스템으로 활용하는 것이 가능하다.
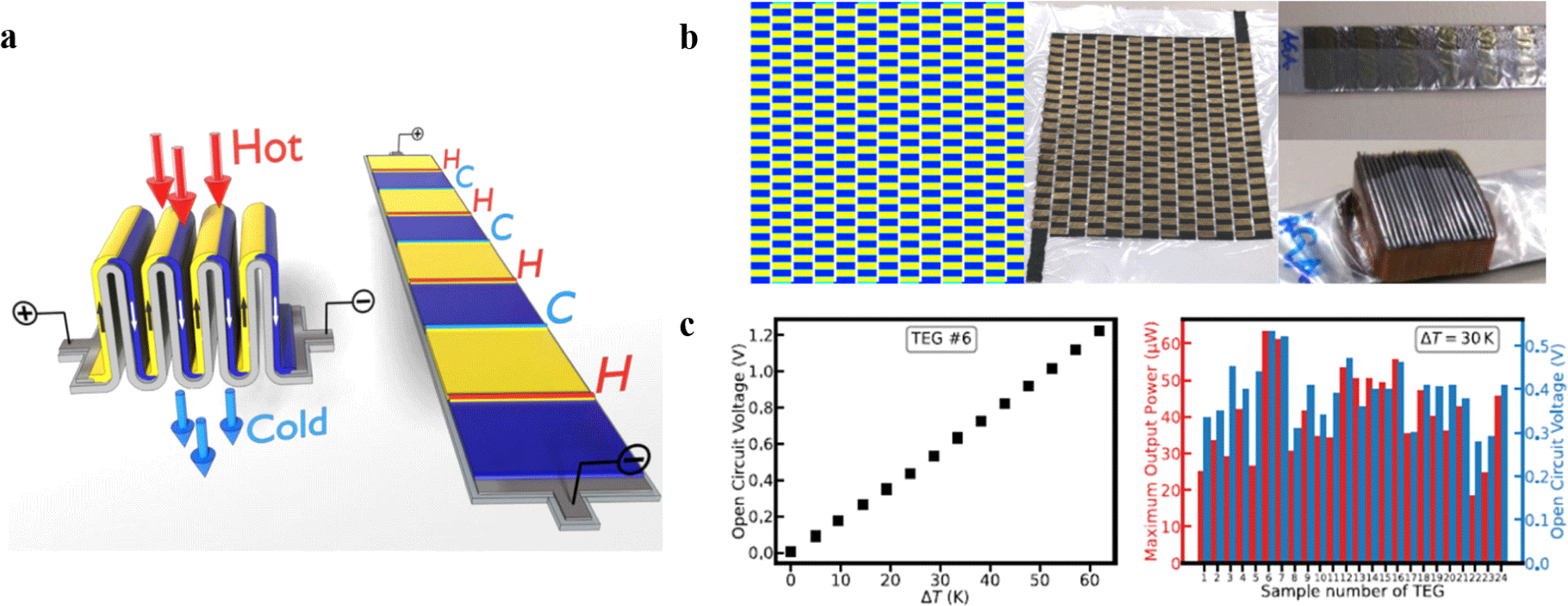
Fig. 6은 마이크로 크기의 3차원 소형 에너지 하베스팅 시스템을 웨어러블 소자에 적용한 연구 결과를 보여주고 있다[18]. 기계적 박리공정을 통해 제작된 3차원 코일 형태의 열전 소자는 실리콘 탄성체 기판을 활용하여 소자의 유연성 및 신축성을 충분히 확보함으로써, 극단적인 기계적 변형에도 실리콘 탄성체 기판 내부에 삽입된 코일 형태의 무기 열전 재료가 파괴되거나 성능 저하 발생 없이 안정적인 소자 동작이 가능하다(Fig. 6(a)).
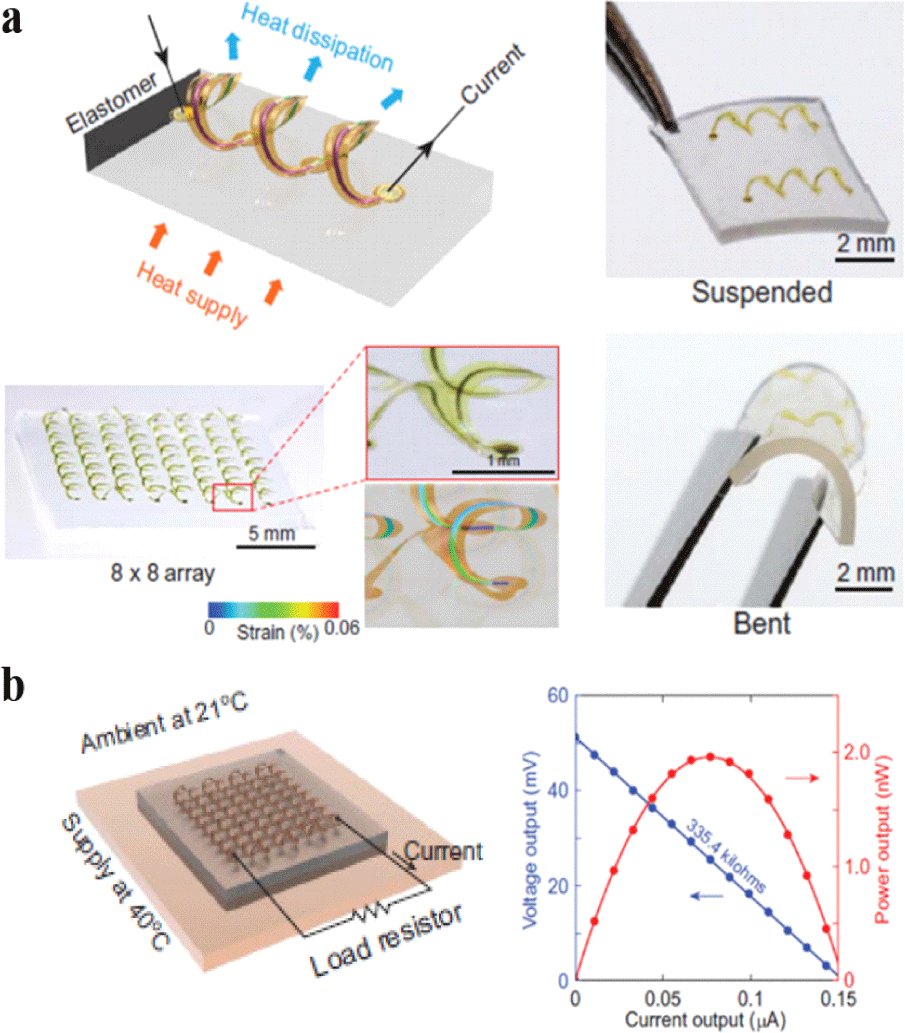
특히 웨어러블 소자 응용을 위해 수백 마이크로 크기의 어레이 형태로 제작된 3차원 열전 소자의 경우 얇은 실리콘 탄성체 기판이 피부와 완전한 접촉을 유도함으로써 체온에 의한 열 공급을 원활하게 만들어 주고, 동시에 외부로 개방된 구조를 통해 열 흐름이 증가되어 기판과 소자 사이에 큰 온도 차이를 유도한다. 즉, 유연성 및 신축성을 갖는 3차원 구조가 열 방출을 촉진시켜 기존의 2차원 형태의 박막형 열전 소자가 갖기 힘든 주변 환경 대비 매우 낮은 열 임피던스(thermal impedance)가 구현되고, 이를 통해 피부에 부착된 3차원 열전 소자의 경우, 40℃에서 최대 약 2 nW의 전력 변환이라는 높은 에너지 효율성을 달성할 수 있다(Fig. 6(b)).
광학 소자 분야 역시 3차원 구조가 적용된 유연 및 신축 소자 연구와 관련하여 최신 연구 결과가 활발하게 발표되고 있다. 예를 들어 복잡한 3차원 구조를 통해 복수의 광원을 동시에 측정할 수 있는 유연 및 신축 광검출기(photodetector)와 기계적 변형에 따라 투명도가 가역적으로 제어되는 3차원 광학 소자에 대한 연구 논문이 보고된 바 있다.
3차원 유연 및 신축 광검출기 소자의 경우 기계적 박리공정을 통해 제조되었으며 그래핀/이산화 몰리브덴(graphene/MoS2) 나노소재를 3차원 입체 구조 표면에 도입함으로써 입사광의 방향, 세기, 입사된 가시광에 의해 생성된 광전류(photocurrent)의 전기적 특성(I-V characteristic)을 분석하는 것이 가능하다(Fig. 7 (a) 및 Fig. 7(b)) [19]. 즉, 3차원 유연 및 신축 광검출기 소자의 반구형 구조는 기존의 2차원 형태의 박막형 광학 소자가 감지하기 어려운 복수의 광원을 동시에 감지할 수 있다. 예를 들어 전 방향(omnidirectional)에서 실시간으로 입사된 빛의 시작점, 이동 방향, 투과 지점을 정확히 측정할 수 있으며 이러한 데이터를 바탕으로 입체적인 3차원 이미지를 생성할 수 있다(Fig. 7(c) 및 Fig. 7(d)).
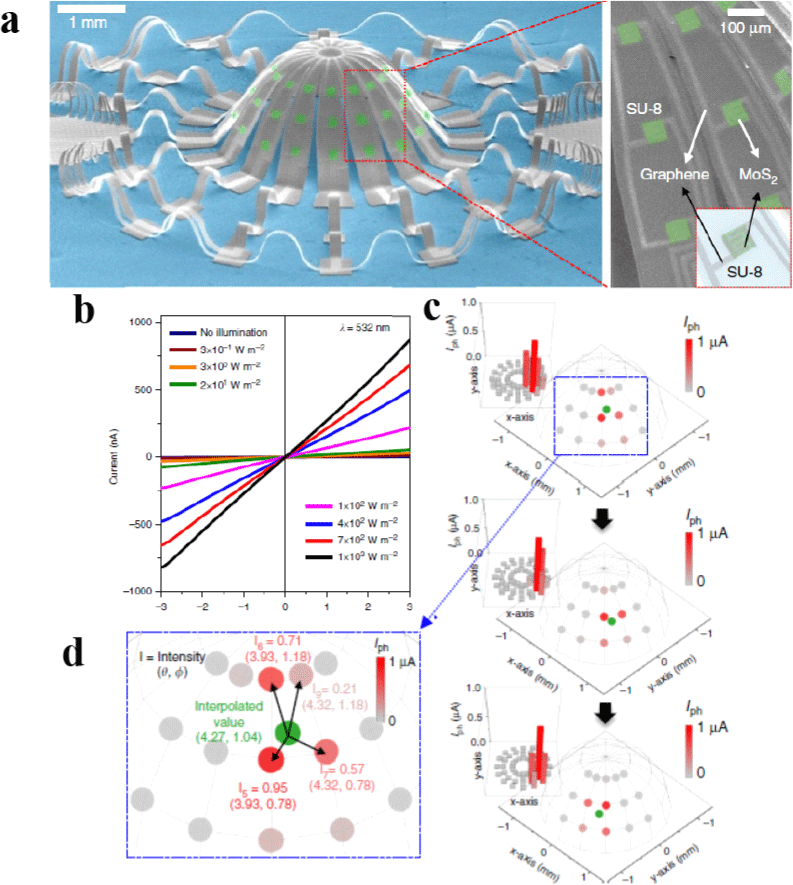
Fig. 8은 인장 변형률(tensile strain)에 따라 소자의 광학 물성이 정밀하게 제어되는 스마트 윈도우(mechano- responsive smart window)와 관련된 연구 결과를 보여주고 있다[25]. Fig. 8(a)는 외부 힘에 의해서 실리콘 탄성체 필름 내부에 존재하는 3차원 구조에 기계적 변형이 발생하면 Al2O3/실리콘 탄성체 계면에서 에어 갭 (air gap)이 생성되고, 이를 통해 가시광을 산란시킴으로써 최종적으로 인장 변형에 따라 투명도를 조절할 수 있는 3차원 광학 소자 이미지를 보여주고 있다.
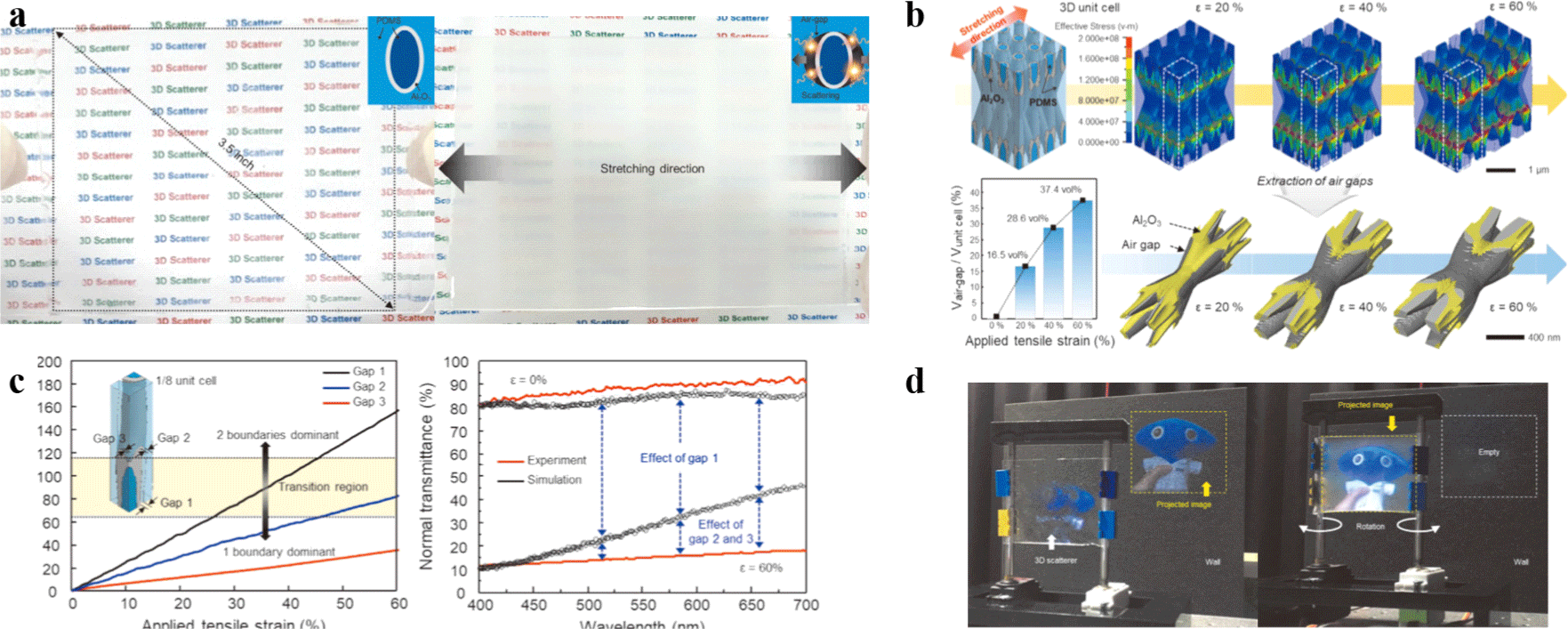
Fig. 8(b)와 Fig. 8(c)에서 (i) 3차원 단위 셀(unit cell)에 가해진 변형률에 따른 에어 갭(air gap)의 생성, (ii) 기계적 변형에 의한 에어 갭 크기의 선형적인 증가, (iii) 인장 변형률에 따른 광학 소자의 투과도 변화와 관련하여 시뮬레이션 결과와 실험 결과가 일치한다는 사실을 확인할 수 있다. 특히 이와 같이 복잡한 3차원 구조를 갖는 유연 및 신축 산란체(scatterer)는 임시 프로젝션 스크린(temporary projection screen)으로 활용이 가능하며, 프로젝션된 이미지가 벽에 초점이 맞추어지는지 여부에 따라 스크린 온/오프 모드(screen- on/off modes)로 각각 동작이 가능하다는 사실을 알 수 있다(Fig. 8(d)). 기존의 박막형 스마트 윈도우들이 유연성 및 신축성을 확보하기 위해서는 매우 복잡한 공정 단계 및 설비가 필요한 반면에, 본 연구에서는 실리콘 탄성체 내에 3차원 구조를 도입시킴으로써 손쉽게 유연성과 신축성을 극대화하고, 동시에 재료의 투명도를 부여하는 것이 가능하다는 것을 보여주고 있다.
3. 결론 및 전망
본 총설에서는 3차원 프린팅 공정, 오리가미 공정, 기계적 박리공정을 활용하여 제작된 복잡한 3차원 구조의 유연 및 신축 소자가 갖는 공학적 잠재력을 분석해 보았으며, 최신 연구 결과를 통해서 기존의 2차원 소자와 비교하였을 때 3차원 구조를 갖는 유연 및 신축 소자의 장점을 설명하였다. 구체적으로 (i) 기존 2차원 형태의 박막형 스트레인 센서의 경우 오직 한 종류의 외부 힘을 감지할 수 있는 반면에, 3차원 구조를 갖는 유연 및 신축 센서 소자의 경우 입체적인 기계적 변형을 통해 수직 압력과 전단력을 동시에 독립적으로 측정할 수 있으며, (ii) 세포 배양용 지지체가 3차원 구조를 가질 경우 오가노이드와 같은 바이오 샘플을 안정적인 고정할 수 있기 때문에 장시간 3차원 형태의 생체 신호 측정이 가능하고, (iii) 유연 및 신축 열전 소자에 3차원 구조를 도입할 경우, 기판과 소자 사이에 큰 온도 차이로 인하여 열전 효율을 증가시키는 것이 가능하며, (iv) 3차원 구조를 갖는 유연 및 신축 광검출기의 경우, 다양한 방향에서 입사하는 복수의 광원을 입체적인 3차원 형태로 감지할 수 있다. 본 총설에서 살펴본 바와 같이 3차원 구조를 갖는 유연 및 신축 소자의 경우, 2차원 형태를 갖는 기존 소프트 일렉트로닉 소자의 성능을 향상시키거나, 응용 분야를 확장하는데 활용하는 것이 가능하다. 나아가 3차원 프린팅 공정, 오리가미 공정, 기계적 박리공정을 통해 제작된 3차원 구조의 유연 및 신축소자가 최근 많은 연구가 이루어지고 있는 소프트 로봇 분야에 이용된다면 차세대 로봇 연구 개발에 큰 파급 효과를 가져올 것으로 기대해 본다.