1. 서론
인쇄 전자소자(printable electronics)는 글과 그림을 찍어내던 기존의 인쇄 기술을 이용해 전도성 잉크를 인쇄하여 만든 전자소자의 일종이다. 인쇄 전자소자는 높은 처리량의 저비용 제조, 다양한 신축성 기판과의 우수한 호환성, 그리고 상대적으로 용이한 디바이스 통합 공정으로 인해 최근 몇 년 동안 엄청난 관심을 받고 있다. 기존의 실리콘 기반 미세 가공 기술인 포토 리소그래피 및 스퍼터링과 같은 진공 기반 기술은 일반적으로 복잡한 제조 공정과 높은 생산 비용을 필요로 한다. 이와 달리 인쇄 전자소자는 분산된 물질을 포함하는 기능성 잉크를 인쇄함으로써 신축성 있는 전자소자를 구현하고자 하며, 이는 투명 전도성 필름(transparent conductive films, TCF)[1-3], 박막 트랜지스터(thin film transistor, TFT)[4], 전계발광(electroluminescent, EL) 소자[5], 그리고 웨어러블 센서[6] 등 다양한 응용을 가능하게 한다.
이러한 신축성 인쇄 전자소자를 구현하기 위한 세 가지 요건은 다음과 같다. 첫째, 큰 변형을 견딜 수 있는 신축성 기판을 마련해야 한다. 둘째, 인쇄 가능한 전도성 잉크를 설계해야 한다. 마지막으로, 이 잉크를 연속적으로 인쇄할 수 있는 대규모 공정 기술이 필요하다. 신축성 기판의 경우 탄성중합체(elastomer)가 많이 사용되고 있으며, 이들의 우수한 기계적 물성은 이미 잘 알려져 있다[7-9].
인쇄를 위한 적절한 기계적 물성을 갖는 전도성 잉크와 대규모 인쇄 공정의 개발은 많은 연구진의 노력에 의해 많은 발전을 이루어 냈으나, 아직 완벽히 상용화된 기술이 아니기에 여전히 다양한 연구가 진행되고 있다.
현재 신축성 기판에 인쇄 가능한 전도성 잉크는 크게 두 가지 방향으로 연구되고 있다. 먼저 신축성은 없지만 우수한 전기 전도도를 가진 나노 물질을 적절한 용매에 분산시킨 후, 기판 위에 인쇄하여 나노 물질 간의 연결을 통해 도선 경로(conductive path)를 유도하는 연구가 많이 진행되고 있다. 금속 나노 물질(예를 들어, 금속 나노입자 및 나노와이어)[10,11]과 탄소 나노 물질(예를 들어, 그래핀 및 탄소 나노 튜브(CNT))[12]을 활용하는 것이 대표적이며, 신축성 절연체와 혼합하여 복합재료로 인쇄하기도 한다[13,14]. 두 번째로는 이미 신축성을 내재하였으면서, 동시에 전도성을 가진 소재를 용매와 함께 적절한 제형의 잉크로 만들어 인쇄하는 연구가 활발히 진행 중이다. 전도성을 가진 PEDOT:PSS 고분자[15,16]와 액체금속이 대표적이며[17], 그 자체로도 인쇄 가능하지만 다른 물질과 혼합하여 복합재료로 사용하거나, 액체 금속의 경우 고분자 매트릭스에서 신축성을 가진 마이크로 필러(filler)로 활용하기도 한다[18].
신축성 전자소자는 다양한 인쇄 기술에 의해 제조되는데, 일반적인 인쇄 기술은 노즐을 이용하는 비접촉 패터닝과 접촉 기반 패터닝의 두 가지로 나눌 수 있다. 비접촉 기술로는 잉크젯 프린팅, 스프레이 코팅, 슬롯 다이 코팅 등이 있으며, 접촉 기술로는 스크린 프린팅, 트랜스퍼 프린팅 등이 있다. 이러한 기술들은 각각 장단점을 가지고 있지만, 모두 잉크를 기판에 정확하고 안정한 형태로 전달하고자 하는 목표를 공유한다. 또한, 저비용 및 대면적 인쇄에 용이한 롤투롤(R2R) 인쇄는 연구실 규모의 인쇄 기술을 대규모 생산 공정으로 확대하는데 필수적이기에 산업계와 연구계 모두의 많은 관심을 받고 있다.
본 리뷰 논문에서는 각 인쇄 기술에 대한 설명, 그리고 신축성 전자소자의 인쇄에 사용되는 전도성 재료에 대해 이야기하고자 한다. 제 2절에서 다양한 인쇄 기술의 기본 원리와 최근의 발전에 대해 설명한다. 이후 제3절에서는 인쇄 공정을 위한 다양한 소재의 잉크 제형 설계 방법을 설명한다. 그리고 2절에서 언급한 인쇄 기술들을 각 소재에 적용하는 구체적인 사례를 제시한다. 이를 바탕으로 인쇄 가능한 신축성 전자소자 분야의 연구 과제, 기회 및 향후 발전에 대해 마지막 절에서 논의한다.
2. 인쇄기법
스크린 프린팅은 마스크 위에 잉크를 떨어뜨리고 롤러, 넓은 판 등을 이용하여 눌러줌으로써 마스크의 패터닝된 부분에 잉크를 통과하게 하여 프린팅을 하는 방법이다(Fig. 1(a)). 스크린 프린팅에서는 잉크의 점도, 잉크와 기판의 젖음성(wetting) 정도, 기판의 평평한 정도와 같은 다양한 변수가 프린팅된 잉크의 품질 및 패턴의 해상도에 영향을 미친다[19]. 최근에는, 포토리소그래피를 이용한 높은 해상도(∼5 μm)를 갖는 마스크의 제작을 통해 40 마이크로미터 폭의 높은 해상도를 갖는 패터닝을 구현했다[20].
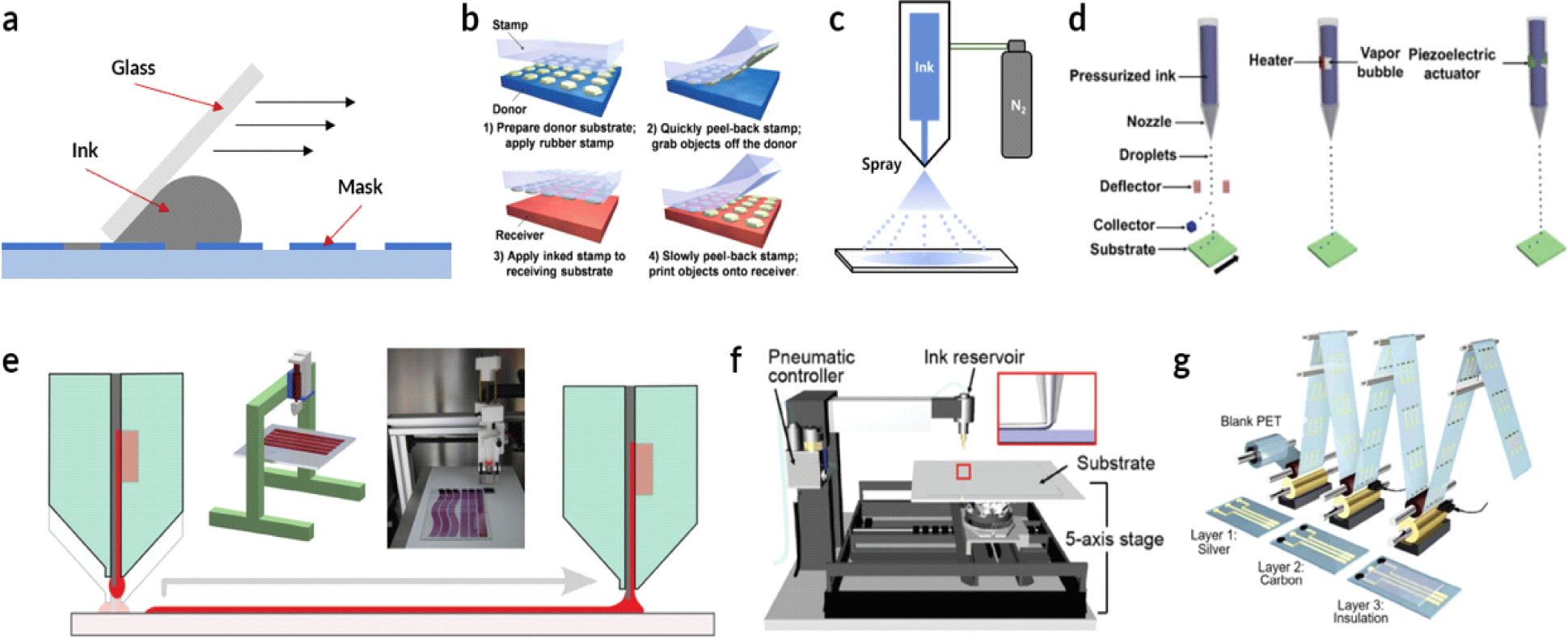
스크린 프린팅은 대면적으로 패터닝을 가능하게 하고, 잉크의 두께를 마스크의 두께를 통해 두껍게 하여 우수한 전기적 성질을 부여할 수 있기에 신축성 인쇄 전자소자로 사용되기에 매우 적합한 방법이다.
트랜스퍼 프린팅은 물리적, 화학적으로 패터닝된 주형 스탬프(molded stamp)를 이용하여 도너(donor) 기판의 잉크를 리시버(receiver) 기판으로 옮기는 인쇄 기술이다(그림1(b). 이때, 각 기판과의 빈틈없는 탈부착을 위해 PDMS와 같은 유연한 탄성중합체 소재를 스탬프로 사용하며 소프트 리소그래피(soft lithography) 의 일종이라 할 수 있다[21,22].
트랜스퍼 프린팅은 트랜스퍼 방식에 따라 크게 세 가지 방식으로 나눌 수 있는데, 먼저 스탬프 위에 직접 잉크를 도포한 후 리시버 기판에 옮기는 가법적 이동(additive transfer)과, 도너 기판 위 균일한 잉크 층에 스탬프가 밀착하여 스탬프와 접촉한 영역의 잉크만을 선택적으로 리시버 기판에 옮기는 감법적 이동(subtractive transfer), 그리고 도너 기판 위 미리 패터닝 된 잉크를 스탬프가 리시버 기판으로 옮기기만 하는 결정론적 결합(deterministic assembly)가 있다.
결정론적 결합은 다른 두 방식과 달리 패터닝과 이동이 분리되어 있어 잉크와 스탬프, 도너 기판의 상호작용을 고려할 필요가 없으므로 더 다양한 소재에 적용할 수 있다는 것이 큰 장점이다.
트랜스퍼 프린팅은 유연한 스탬프를 사용하므로 거의 모든 종류의 기판에 상온에서 높은 정확도로 인쇄할 수 있다. 또한 아주 빠르게 병렬적으로 여러 번 잉크를 옮길 수 있어 높은 공간 해상도의 대면적 프린팅이 가능하며 잉크의 2D, 3D 배치가 가능한 점이 다른 인쇄 기술보다 우수한 특징이다[23]. 그러나 스탬프의 탄성으로 인해 스탬프를 강하게 누를 시 미세 요철 구조가 납작하게 눌리거나, 높은 종횡비를 가지는 패턴의 경우 요철이 휘어져 패턴이 무너질 수 있는 단점이 있다[24,25].
스프레이 코팅은 대표적인 비접촉식 인쇄 기술로 마이크론 사이즈의 잉크 입자들을 급격하게 분출하여 기판 위에 층층이 쌓는 공정이다(그림 1(c))[26].
잉크젯 프린팅과 유사하지만 스프레이의 방향이 무작위란 점에서 잉크젯 프린팅과 달리 디지털 방식의 제어가 없는 코팅 방법이라 할 수 있다. 이때, 마스크를 사용한 2D 패터닝도 가능하지만, 가장자리의 선명도가 떨어지며 마스크에 적층된 잉크를 재활용하기 힘들다는 단점이 있다.
잉크 입자의 스프레이를 만들기 위해 주로 고압 가스를 이용한 저온분사(kinetic spraying) 방식이 사용되며, 분출된 입자가 기판과 충돌 시 적층된 입자들과 접합을 형성하도록 고속충돌을 일으키는 것이 주 원리이다[27]. 입자의 크기는 잉크의 점도, 표면 장력, 밀도에 따라 달라지며, 재료 외적으로도 가스의 압력, 노즐의 모양, 기판의 표면 장력, 코팅 스피드 등에 좌우된다. 잉크 에어로졸로 인한 오염으로 인해 대면적 롤투롤 공정(roll-to-roll, R2R)은 어렵지만, 실험실 규모에서 쉽게 코팅할 수 있는 것이 장점인 접근성 높은 공정이라 할 수 있다.
잉크젯 프린팅은 점도가 낮은 잉크에 펄스를 가함으로써 잉크들이 노즐을 통과하게 하여 잉크 방울을 만들고, 이들을 원하는 부분에만 분사하는 프린팅 방법이다(그림 1(d)). 이때 노즐에서의 잉크의 방출을 위한 펄스는 열을 통해 만들어진 증기포, 또는 압전기 작동 장치를 통해 만들어진다[28].
잉크젯 프린팅에 사용되는 잉크는 전도성을 갖는 나노 입자가 용매에 안정한 콜로이드 형태로 분산되어 있는 형태다. 잉크젯 프린팅에 사용되는 잉크의 품질은 잉크 속 입자의 크기, 잉크의 점도, 표면장력, 점도에 의해 결정된다. 잉크의 물리적 성질은 레놀즈(Re), 위버(We), 오네수지(Oh) 수를 통해 표현될 수 있다.
ρ, η, γ는 각각 잉크의 밀도, 점도, 표면장력이고, ν, α는 각각 노즐이 움직이는 속도, 노즐의 반경이다. 일반적으로 오네수지 수의 역수인 Z값을 통해 잉크 방울 형성의 안정도를 평가한다. Z값이 1에서 14 사이일 때 잉크젯 프린팅을 위한 방울이 안정적으로 형성된다[29,30]. 여기서 추가로 고려해야 하는 것은 입자의 크기로, 입자의 크기가 노즐의 반경의 50분의 1보다 크게 되면 프린팅 도중에 노즐을 막을 가능성이 존재한다[31,32]. 다만 1D입자의 경우 이러한 크기가 덜 중요할 수도 있다. 이는 프린팅 과정에서 만들어지는 전단력에 의한 입자의 정렬로 인해 1D 입자가 노즐을 막을 확률이 줄어들기 때문이다[31].
잉크젯 프린팅의 가장 큰 장점은 다양한 재료를 넓은 면적의 기판에 정확하고 빠르게 프린팅 할 수 있다는 것이다. 이와 동시에 잉크젯 프린팅은 원하는 부분에만 잉크를 분사하는 방식이기에 기존에 널리 사용되는 리소그래피와 달리 재료의 사용을 최소화할 수 있고[33], 기판과 접촉 없이 인쇄하기 때문에 기판의 오염을 최소화할 수 있다는 장점을 갖는다[34,35].
슬롯-다이 코팅은 잉크의 균일한 도포가 가능한 비접촉식, 대면적 인쇄 공정이다[36,37]. 1 mPaㆍs 미만에서 수천 Paㆍs까지의 광범위한 점도의 잉크를 코팅할 수 있으며, 코팅 속도 또한 1 mㆍmin−1 미만에서 600 mㆍmin−1 이상의 넓은 스펙트럼에서 가능하여 인쇄 조건을 쉽게 최적화할 수 있다.
슬롯-다이 코팅(slot die coating)에서는 그림 1e와 같이 잉크가 슬롯을 통해 코팅 헤드로 펌핑된다. 이때 잉크는 코팅 헤드와 기판(web) 사이에 메니스커스(meniscus)를 형성하며 구슬 형태(bead)로 맺히게 되는데, 지속적인 잉크 공급으로 인해 인쇄 시에도 메니스커스를 일정하게 유지할 수 있다. 그리고 이는 움직이는 기판 위에서 일정한 조건으로 잉크를 도포하며 넓은 면적에 걸친 균일한 코팅을 가능하게 한다[26]. 이때 필름의 두께 d는 다음과 같이 표현할 수 있다.
여기서 f는 펌핑량(pumping rate)이고 S는 코팅 속도, w는 코팅 너비, c는 잉크의 농도, 그리고 ρ는 최종적으로 도포된 코팅층의 밀도를 의미한다. 이렇듯 코팅 속도, 코팅 너비, 펌핑량을 조절하여 쉽게 필름 두께를 조작할 수 있다. 이 뿐만 아니라 공정 효율을 높이기 위해 더블 슬롯-다이 코팅(double slot-die coating) 공정 또한 고안되어 있으며[38], 최근에는 3D 프린팅 시 노즐(nozzle) 대신 슬롯-다이를 활용한 사례도 있는 만큼 그 활용도가 높은 인쇄 기술이다[39].
직접 잉크 쓰기 방법은 점도가 높은 잉크를 공압을 이용하여 노즐을 통해 방출시킴으로써 잉크를 인쇄하는 방법이다[40,41]. 직접 잉크 쓰기 방법은 컴퓨터를 이용한 미세한 조절을 이용해 잉크를 복잡하면서 고해상도를 갖는 미세한 패턴으로 인쇄할 수 있다[42].
Fig. 1(f)는 직접 잉크 쓰기 방법을 나타낸다. 이 시스템은 잉크 저장공간, 잉크가 통과하는 노즐, 움직이는 받침판, 그리고 잉크의 방출을 위한 공압 조절 장치로 구성된다. 일반적으로 직접 잉크 쓰기 방법은 다음과 같은 순서로 이루어진다. 첫 번째, 잉크가 공압을 통해 노즐을 통과하게 되면 노즐의 끝에서 메니스커스(meniscus)를 형성한다. 그 다음으로 잉크와 기판 사이의 상호작용에 기반한 젖음성을 통해 잉크가 기판 위에 안정적으로 올라간다. 이 때 젖음성이 충분하게 되면 받침판이 움직일 때 잉크가 안정적인 정상 상태를 유지하면서 프린팅이 진행된다[43].
직접 잉크 쓰기 방법에서 인쇄된 잉크의 품질을 결정하는 요소는 잉크의 물리적 성질, 그리고 노즐이 움직이는 속도와 잉크가 노즐을 나오는 속도의 비율이다[40,44].
잉크는 전단 응력이 가해질 때에만 노즐을 통과하여 프린팅이 되고 프린팅 후에 기판 위에서는 안정적인 형태를 유지해야 하기 때문에 전단 응력이 가해지지 않을 때에는 고체와 같이 높은 탄성률(>104 Pa)을 가져야 하고, 전단 응력이 가해지면 탄성률이 급격히 낮아지면서 액체와 같은 성질을 가져야 한다[40].
또한 노즐이 움직이는 속도(V)와 잉크가 노즐을 통과하는 속도(C)의 비율 V*(V/C)에 따라 인쇄된 잉크의 형태가 변하게 된다. V*가 1보다 작은 경우, 프린팅 경로의 길이가 노즐에서 나오는 잉크의 길이보다 짧으므로 인쇄된 잉크는 코일 모양을 갖게 된다. V*가 1 이상의 값을 갖는 경우 위와 반대의 상황이므로 인쇄된 잉크는 반듯한 직선 형태이다. 이 경우 V*의 값에 따라 Die-swelling(1≤V*<α2), Equi-dimensional(V*=α2), Thining(α2<V*<Vf), 또는 discontinuous(Vf≤V*) 한 형태의 선이 인쇄된다. 이 때 Vf 값은 잉크의 점도에 따라 결정되며, 높은 점도를 가질수록 낮은 Vf값을 갖는다[44].
직접 잉크 쓰기 방법은 잉크젯 프린팅과 같이 재료의 사용을 최소화할 수 있고, 기판의 오염을 최소화할 수 있다는 장점을 갖는다. 이와 더불어 적절한 잉크의 설계를 통해 3D 구조를 갖는 전극을 인쇄할 수 있다는 잉크젯 프린팅이 갖지 못하는 장점을 갖고 있다.
롤투롤 공정은 인쇄 규모를 실험실 규모에서 산업 규모로 확장하기 위해 필수적인 기술이다. 일반적으로 여러 개의 롤러(roller) 사이를 기판(web)이 지나가면서 라미네이트, 코팅, 프린팅 등이 연속적으로 이루어지며, 빠르고 저렴하게 전자소자의 대면적, 대량 생산을 가능하게 한다(그림 1(g))[45]. 지금까지 언급한 여러 인쇄 기술을 롤투롤 공정으로 구현하기 위한 노력들이 많이 있지만, 산업 규모의 대량 인쇄는 아직 사례가 많지 않다.
스크린 프린팅의 경우, 스퀴지(squeegee)가 스크린 위에서 잉크를 민 후 프린팅 된 기판(web)이 롤러를 따라 이동하는 플랫 베드(flat bed) 방식과 스크린이 롤 형태로 있어 연속적으로 스크린 프린팅이 가능한 로터리(rotary) 방식이 있다[46,47].
잉크젯 프린팅, 스프레이 코팅, 슬롯-다이 코팅 또한 기판이 롤러를 따라 움직이면서 잉크를 인쇄하는 롤투롤 방식이 고안되었다. 트랜스퍼 프린팅의 경우, 패턴이 양각된 볼록판 롤러를 이용하는 플렉소 프린팅(floxoprinting)과 패턴이 음각된 오목판 롤러를 이용하는 그라비어 프린팅(gravure printing)이 롤투롤 공정으로 구현되었다[26].
3. 신축성 전도체를 위한 재료 및 이들의 응용
인쇄 가능한 잉크에 전도성을 부여하는 전도성 나노 물질 중 가장 대표적인 것이 금속 나노 구조체이다. 은(silver, Ag)은 상온에서 전기 전도도가 가장 높은 금속이며, 이로 인해 은 나노입자 혹은 은 플레이크(silver flake), 은 나노와이어 등 다양한 형태의 인쇄 가능한 전도체로서 가장 광범위하게 연구되었다[48,49]. 이와 비슷하게 구리(Copper, Cu 나노입자 및 나노와이어 또한 많이 연구되고 있으며[50,51], 이러한 금속 나노 구조체를 이용하여 금속 그리드(Grid) 혹은 금속 나노와이어 네트워크를 만들어 높은 전도도와 함께 높은 빛 투과율과 우수한 기계적 특성을 가지는 전도체를 구현할 수 있다.
금속 나노 구조체는 그 자체로 높은 전기 전도도를 가지고 있으며 PVP와 같은 바인더(binder)를 활용하면 잉크 내 안정한 분산을 쉽게 구현할 수 있다. 또한 큰 종횡비에도 불구하고 우수한 물리적 안정성을 보여준다는 장점이 있다. 그러나 고분자 기반 신축성 기판과의 접착력이 좋지 않거나 코팅된 나노 구조체의 거친 표면으로 인한 박막 불안정성과 금속 산화로 인한 성능 저하의 가능성이 존재한다[52]. 결정적으로 신축성 소자의 큰 변형 시 퍼콜레이션 네트워크(percolation network)가 엉성하게 되며 도선 경로(conducting pathway)가 끊기는 제한된 신축성을 보여준다[13,53].
잉크젯 프린팅은 은 나노 구조체 잉크를 인쇄하는 가장 보편적인 방법이며[54], 잉크 건조 시의 불안정성을 해결하고 잉크젯 프린팅 가능한 소재의 저변을 넓히기 위한 시도가 많이 있다. 은 나노와이어의 노즐 막힘 현상을 방지하기 위해 종횡비를 줄이는 트리밍(trimming)을 하거나[55], 프린팅 시 잉크 증발을 막기 위해 고비점(high boiling point) 용매를 첨가하는 잉크 제형 연구[31] 등이 진행되었다. 한편 커피 링 현상을 이용하여 복잡한 구조의 패턴을 인쇄하거나[56], 전기장을 이용하여 잉크 흐름을 유도해 더 높은 인쇄 해상도를 가능케 하는 전기 수력학 잉크젯 프린팅(electrohydrodynamic inkjet printing, EHD printing) 연구가 진행되었다. 또한 스프레이 코팅을 이용하여 은 나노와이어를 늘어날 수 있는 고분자 기판 위에 코팅함으로써 신축성 전극을 만드는데 활용되고 있다(Fig. 2(a)[3]. 이외에도 스크린 프린팅은 금속 나노 구조체 잉크를 대량 인쇄할 수 있는 유망한 기술로서 은 플레이크 잉크 도포에 널리 쓰였으며[57], 현재는 은 나노입자와 은 나노와이어의 스크린 프린팅을 통해 더 높은 해상도를 구현하려는 연구가 진행되고 있다[58]. 마지막으로 대면적 인쇄가 용이한 슬롯-다이 코팅과 그라비어 프린팅, 플렉소 프린팅의 금속 나노 구조체 잉크 기반 롤투롤 공정이 연구되고 있다. 은 나노 구조체 외에도 구리 혹은 금(gold) 나노 구조체의 인쇄 기법 또한 비슷한 양상으로 이루어지고 있다. 그러나 위와 같은 많은 연구들은 아직 충분한 신축성을 보여주지 못한 채 유연성 소자 단계에 머무르는 한계를 보여주고 있다[59,60].
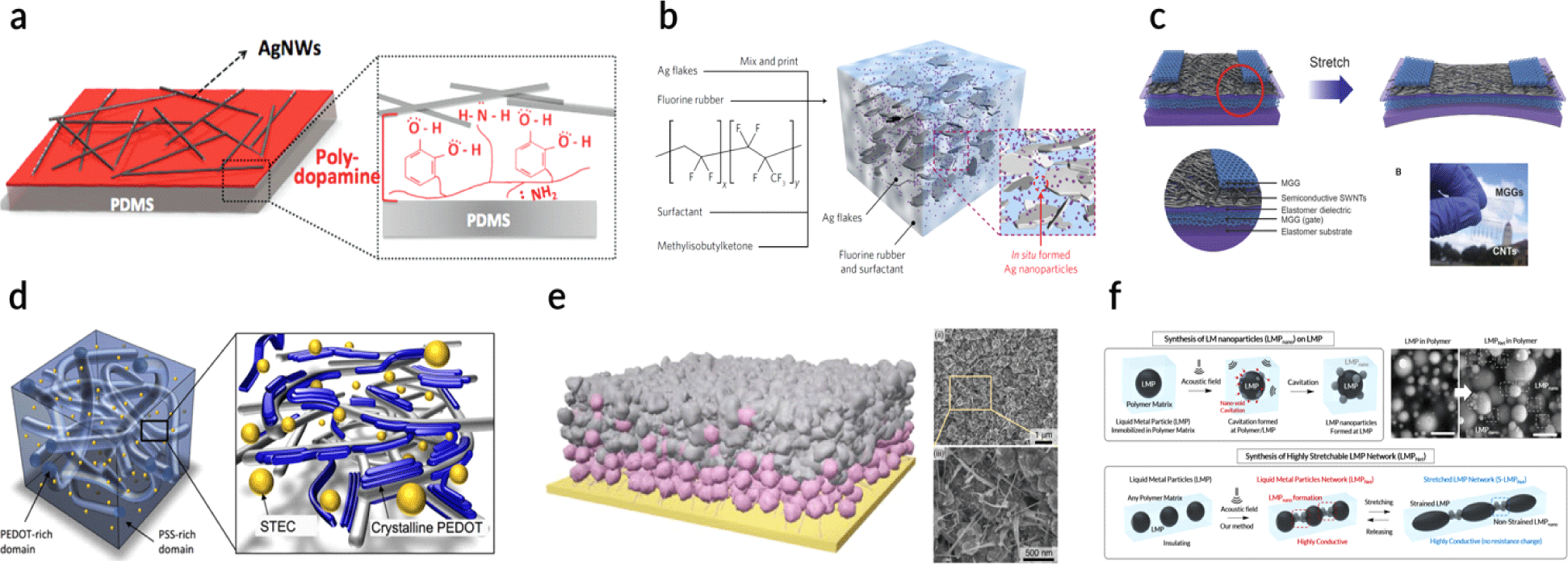
Matsuhisa et al.은 불소 고무(fluorinated rubber) 매트릭스 안에 은 플레이크(silver flake)와 은 나노입자의 퍼콜레이션을 만들어냈고 고분자 금속입자 복합재료에 전도성을 부여하였다. 이를 통해 금속 나노 입자를 이용한 신축성 전자소자를 구현하는데 성공하였다(Fig. 2b)[13].
금속 나노 구조체 외에도 그래핀(graphene)과 탄소나노튜브(carbon nanotube, CNT)를 포함한 탄소 나노 물질들은 고유의 높은 전하 이동도(carrier mobility)와 물리적 유연성, 얇은 두께로 인한 높은 빛 투과율로 인해 인쇄 가능한 신축성 전자 소재로 유망한 물질이다[61]. 탄소나노튜브는 단원자 두께의 탄소 시트가 둥글게 말려 원통형 벽을 이룬 나노 구조체이다. 이는 종횡비가 큰 1차원 소재이므로 금속 나노와이어와 마찬가지로 신축성 기판 위에 퍼콜레이션 네트워크를 형성하며 전도성을 부여한다[62]. 반면 그래핀은 탄소 원자가 단층의 벌집 구조를 이룬 2차원 소재이므로 1차원 소재인 탄소나노튜브와 다르게 그 자체로 평면적 적층이 가능하기에 공정의 규모적 확장 가능성이 높다는 것이 특징이다[63].
탄소나노튜브와 그래핀은 구리와 비슷하거나 더 높은 전기 전도도를 가지고 있으며 물리적 특성은 철강보다 100배 강하지만[64], 파괴 변형률(fracture strain)은 각각 15%, 20%에 달하는 금속 나노 구조체보다 신축성 전자소자에 더 적합한 소재이다[65,66]. 그러나 탄소나노튜브는 금속 나노와이어와 마찬가지로 표면의 거칠기가 높아 박막 불안정성을 초래하며[67], 탄소 시트의 카이랄성(chirality)에 따라 서로 다른 반도체와 도체 탄소나노튜브를 분리해내는 것이 어려워 공정의 한계가 있는 것이 단점이다[68]. 무엇보다 탄소나노튜브와 그래핀 모두 여러 용매에서 낮은 분산성을 보여주기 때문에, 응집이나 침전이 없으면서도 고농도의 탄소 나노 물질 잉크를 만드는 것이 상당한 장벽으로 작용하고 있다. 이를 해결하기 위해 다양한 고분자 바인더(binder)나 계면활성제(surfactant)를 활용하고 표면 개질을 통해 분산성을 높일 수 있지만 공정의 복잡성 증가와 탄소 나노 물질의 성능 저하로 이어지기도 한다[69-71].
탄소 기반 나노 물질 역시 다양한 인쇄 기법으로 신축성 전자소자를 구현하는데 사용되고 있다. 특히 인쇄 가능한 탄소 나노 물질 잉크를 만들기 위한 노력들이 많았다. 잉크젯 프린팅의 경우, 순수 1-Methyl-2-pyrrolidinone(NMP) 용매에 그래핀을 분산시킨 잉크가 최초로 사용되었으며[29], 이후 다양한 혼합 용매와 바인더(binder)를 조합하여 인쇄된 그래핀 필름의 전기 전도도와 물리적 안정성을 향상해 왔다. 최근에는 물 기반의 탄소나노튜브 잉크를 인쇄하여 생체적합성 또한 확보한 사례가 등장하고 있다[72].
스크린 프린팅에서도 역시 탄소 나노 구조체의 안정적인 인쇄를 위해 ethyl cellulose(EC), polyaniline(PANI), polyvinylpyrrolidone(PVP) 등의 다양한 고분자 바인더(binder)들이 연구되었으며, 현재까지 많은 탄소 기반의 신축성 전자소자가 연구되어 왔다(그림 2(c))[73,74].
전도성 고분자는 그 자체로 전기전도도를 갖는 고분자 재료로, 생체적합성, 우수한 기계적 성질 및 전기적 성질, 그리고 안정성으로 인해 신축성 전도체로 많은 관심을 받고 다양한 응용이 진행되었다[75].
전도성 고분자에서 각광을 받는 재료는 PEDOT: PSS이나, 결정구조로 인해 신축성이 매우 낮아서 신축성 전도체로 사용하기 어렵다는 문제점을 갖고 있다. 이들을 신축성 전도체로 사용하기 위해서 가소제(plasticizer)와 섞어서 신축성을 부여한다. 이러한 가소제로 이온성 액체, 계면 활성제 등이 주로 사용된다(Fig. 2(d))[76].
위와 같은 방법을 이용하여 다양한 인쇄가 가능한 신축성 전도성 고분자가 개발되었다. 이들 중 일부를 소개하고자 한다.
Wang et al.에서는 PEDOT:PSS 수용액을 이온성 액체와 섞어 잉크로 만든 후, 잉크젯 프린팅 및 스크린 프린팅을 진행하여 높은 해상도를 갖는 패턴을 인쇄함으로써 전도성 고분자가 배선으로 사용될 수 있음을 보였다(Fig. 2(e))[77]. 이에 더불어, Zhu et al.에서는 위의 PEDOT:PSS와 이온성 액체로 만든 잉크를 스크린 프린팅을 통해 인쇄하였고, 이들을 신축성 배선으로 적용함으로써 전도성 고분자가 실제로 신축성 전자소자에 응용될 수 있음을 보였다[78].
이외에도 Wu et al.에서는 PEDOT:PSS와 하이드로젤과 섞은 후에 직접 잉크 쓰기를 이용하여 패터닝을 진행하였다. 비록 전자소자로의 응용을 보여주지는 않았지만 전도성 고분자가 직접 잉크 쓰기를 통해 신축성 전자소자에 이용될 가능성이 있음을 보였다[79].
액체 금속은 상온에서 액체의 상태를 유지하는 금속으로, 높은 전기전도도(34,000 S/cm)를 갖고, 액체라는 성질에 기반해 자유롭게 형태가 변하고 늘어날 수 있기에 늘어났을 때 저항이 적은 신축성 전도체로 많은 관심을 받고 있다[17].
액체 금속의 종류에는 수은 및 갈륨을 기반으로 한 다양한 합금 물질들이 있다. 하지만 수은은 독성을 갖기에 신축성 전도체를 위한 재료로 이용되지 않고, 갈륨을 기반으로 한 합금들이 주로 연구되고 있다. 액체 금속으로 주로 사용되는 합금은 공융-갈륨-인듐(EGaIn) 및 공융-갈륨-인듐-주석(Galinstan)이 있다[80].
액체금속은 다양한 방식으로 인쇄되어 신축성 전자 소자에 응용되고 있다.
Ma et al.에서는 EGaIn을 스텐실 프린팅을 통해 SBS 고분자 필름 위에 패터닝을 하고, 액체금속 기반 신축성 배선 사이 LED를 연결해 신축성 LED를 보였다[81]. 또한 Liu et al.에서는 액체 금속에 열을 가하여 고체와 액체의 상을 동시에 갖는 액체금속 기반의 잉크를 만들고 스텐실 프린팅을 이용해 신축성 배선을 인쇄하고 이에 다양한 전자 부품을 연결하여 복잡한 구조를 갖는 증폭기 소자를 보였다(그림 2(e))[82]. 그리고 Park et al.에서는 액체금속을 하이드로겔 위에 트랜스퍼 프린팅을 이용하여 인쇄하여 신축성 전자소자를 위한 신축성 배선으로 사용될 수 있음을 보였다[83]. 그리고 Lee et al.에서는 액체금속-고분자 복합체를 다양한 프린팅 기법을 통해 패터닝을 한 후, 초음파를 이용하여 비파괴적인 방법으로 전도성 네트워크를 형성해 신축성 전자재료를 구현했다. 그리고 이를 신축성 인쇄회로 기판으로 응용함으로써 신축성 전자소자의 기판을 마련했다(그림 2(f))[84].
앞서 말한 다양한 신축성 전자재료를 이용해 만든 신축성 인쇄 전자소자는 기존의 단단한 실리콘 기반 전자 소자들로는 실현할 수 없는 디바이스를 구현하고 있다. 각광을 받는 활용처는 웨어러블 전자소자로, 인간 피부를 모방하여 자극을 감지하는 기능을 구현하려는 다양한 연구가 진행되었다. 금속 나노 입자-고분자 기반의 신축성 전자 재료를 배선으로 이용해 변형 및 온도 센서를 옷 위에 전기적, 기계적으로 연결하여 웨어러블 센서를 구현한 연구가 진행되었다(Fig. 3(a)) [13]. 이를 넘어서 단순한 웨어러블 센서가 아닌 피부와 유사한 기계적 성질을 갖는 고분자를 기판과 신축성 전극으로 이용하여 피부에 부착할 수 있는 센서 또한 제시되었다(Fig. 3(b) 및 Fig. 3(c))[78,85]. 그리고 인간 피부의 기능을 넘어서 다양한 생체 신호를 감지하는 바이오 센서에 대한 연구 또한 활발히 진행되고 있다(Fig. 3(d)∼Fig. 3(f))[84,86].
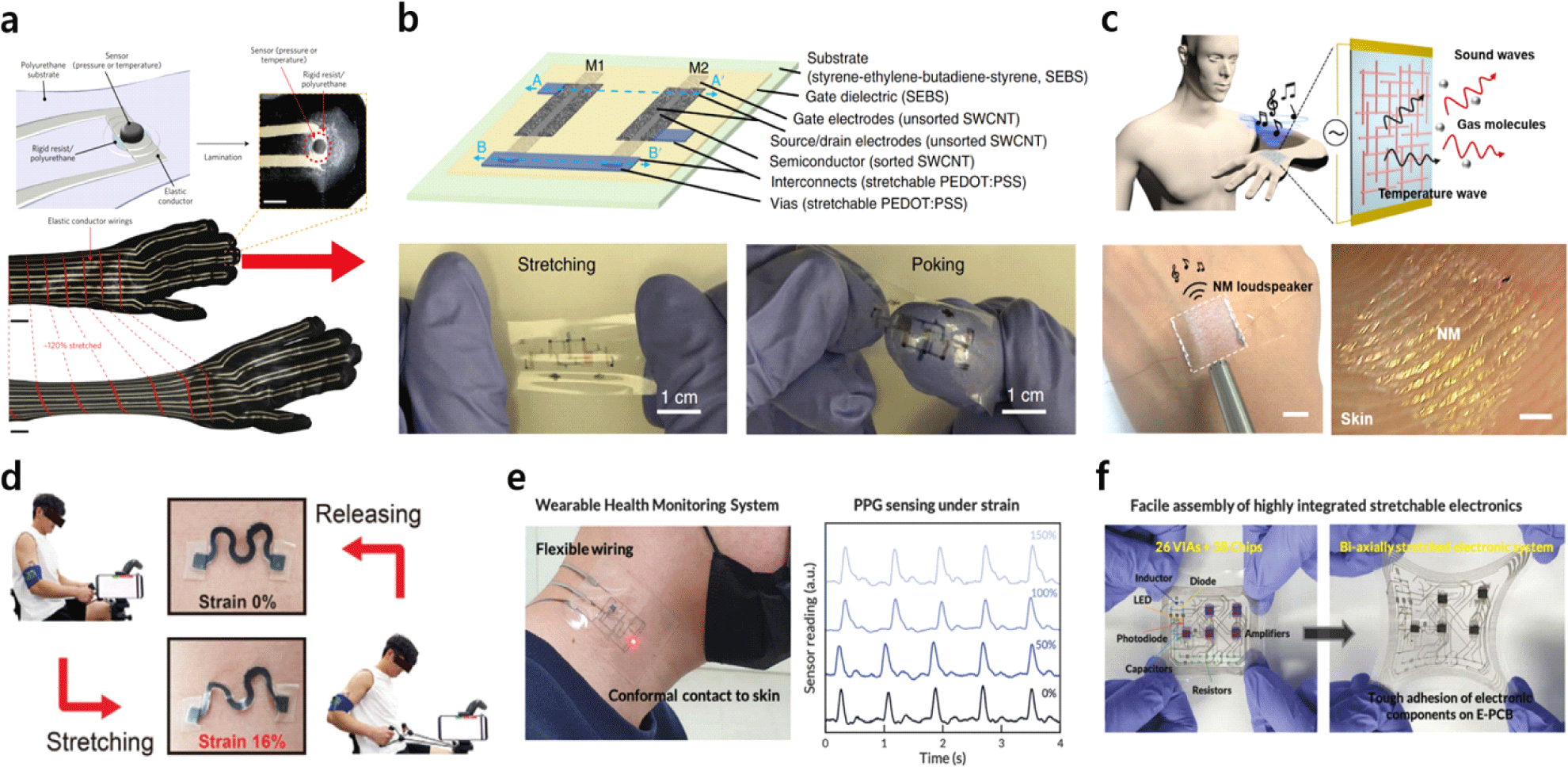
그러나 신축성 전도체를 기반으로 한 디바이스가 실생활에 적용되기 위해선 몇 가지 한계점을 극복해야 한다. 먼저 신축성 전도체가 도선으로 사용될 경우 기계적 변형과 무관하게 일정한 저항을 유지해야 하지만, 많은 재료에서 금속의 균열, 고분자의 구조 변화, 전도성 필러의 퍼콜레이션의 끊김 등으로 인해 어려움을 겪고 있다. 이에 대해 Kang et al.에서 혁신적으로 타개한 바가 있다[84]. 또한 웨어러블을 넘어서 몸 안에 삽입하기 위해선 생체 적합성이 매우 중요하나 많은 신축성 전도체들이 그렇지 못한 경우가 많다. 이에 대해 Kim et al.에서 금 코팅을 통해 은 나노와이어의 생체 적합성을 부여한 바가 있다[87]. 또한 고성능 전자 소자를 개발하기 위해선, 재료 자체의 특성뿐만 아니라 공간적 해상도를 높여 디바이스 소형화를 이루어 내야한다. 따라서 더 높은 해상도의 인쇄 기술과 그에 맞는 재료 특성을 연구할 필요가 있다. 나아가 공간적 복잡성을 확보하기 위해 2D 프린팅이 아닌 3D 프린팅이 가능한 신축성 전도체 연구 또한 필요할 것이다.
4. 결론 및 전망
신축성 전자소자는 웨어러블 전자소자, 체내 삽입형 전자소자, 소프트 로보틱스를 포함한 다양한 분야에서 혁신적인 변화를 가져다 줄 수 있다. 이러한 신축성 전자소자의 실현은 새로운 신축성 전도체의 개발, 그리고 이들의 패터닝을 위한 인쇄 기법의 개발 및 발전을 통해 이뤄낼 수 있다. 기존의 리뷰 논문은 주로 신축성 전자소자에 사용될 수 있는 신축성 전도체의 개발을 집중적으로 소개했으나, 이 리뷰 논문에서는 신축성 전자소자의 제작을 위한 신축성 전도체의 인쇄 기법 및 실제 응용 사례에 대해 이야기함으로써, 신축성 소재 개발이 디바이스 실용화로 이어지기 위해 인쇄 기술에 적합한 소재 특성 개발이 중요함을 강조하고자 한다.
이 리뷰 논문에서 언급된 다양한 사례에서 볼 수 있듯이, 많은 연구진의 노력에 의해 인쇄기법 및 신축성 전자 재료에 많은 발전이 있었다. 하지만 여전히 신축성 전자 재료 및 인쇄 기법에서 극복해야 할 문제점들이 여럿 있다. 금속 나노 필러의 경우, 균일한 사이즈를 갖는 나노 입자의 합성과 금속 입자의 산화를 막기 위한 후처리 과정 연구가 더욱 필요하며, 탄소 나노 필러의 경우 잉크 내 고른 분산을 이루어 인쇄 가능성을 높이는 것이 중요한 과제로 남아 있다. 전도성 고분자 또한 적절한 상 분리 조절을 통해 더 높은 전기전도도와 신축성을 확보해야 하며, 액체 금속의 경우 필름 손상에 대한 기계적 안정성을 획득해야 한다. 마지막으로 각 인쇄 기법에 따른 적절한 잉크 제형 설계 및 고해상도의 인쇄를 이루기 위한 인쇄 기법의 최적화 연구가 반드시 동반되어야 한다. 이 리뷰 논문에서 소개한 신축성 전도체들 특유의 용액 공정의 용이함과 스마트한 디바이스와 더욱 밀접해지고 싶어하는 사람들의 수요로 인해, 인쇄 가능한 신축성 전도체와 이에 최적화된 인쇄 기법은 지금보다 더 많이 연구되고 필요로 하게 될 것이라 예상한다.