1. 서론
연속 잉크젯 방식(continuous inkjet, CIJ)은 충전된 액적을 편향시켜 프린팅하는 방식을 이용하여 다양한 임의의 패턴을 프린팅하는 잉크젯 방식 중 하나이다[1-7].
가장 많이 사용되는 잉크젯 방식인 요구 적출형 잉크젯(drop on demand, DOD)과 비교하여 연속 잉크젯의 장점은 2 cm 이상의 노즐과 기판의 거리를 유지하며 프린팅할 수 있어서 3차원 표면에도 프린팅이 가능하고 1개의 노즐로 10 mm 이상의 넓은 폭을 프린팅 할 수 있다. 이러한 장점을 이용하여 제품의 평면 또는 곡면 영역에 날짜 등의 정보를 마킹하는 분야에서 적극적으로 응용되고 있다[1-2].
연속잉크젯은 크게 바이너리(binary)와 다중 편향 (multiple deflection) 방식의 두 가지로 되어 있다. 바이너리 방식은 프린팅이 되거나, 아니면 잉크가 회수되게 하거나 두 가지의 경우만 있는 반면에, 다중 편향 방식은 대전되는 대전량을 조절하여 프린팅 위치를 각 drop 별로 제어하는 방식이다. 본 연구에서 사용되는 방식은 대전량을 제어하여 프린팅 위치를 제어하는 다중 편향 방식을 적용하였다. 토출 주파수는 외부에서 가진(oscillation)과 같은 주파수로 불안정이 생기게 되어 외부 가진과 같은 주파수를 갖게 된다. 액적의 크기 및 편형량의 크기 등을 고려하여 50 kHz의 주파수를 갖는 액적을 생성시키고, 각 액적을 대전시키는 방법으로 대전량에 따른 편향을 제어하는 방식으로 프린팅 하는 방식을 사용하였다.
연속 잉크젯은 아직까지는 다양한 분야로의 확장이 이루지고 있지는 않고 있다. 그 이유는 연속잉크젯에서는 많은 양의 잉크(1 L)이상의 잉크를 사용하여 순환하는 방식으로 값비싼 잉크를 개발하고 최적화 하는데는 비용이 많이 필요하고, 저점도(2cP 내외)의 잉크를 사용해야 하는 단점이 있기 때문이다. 그럼에도 불구하고, 일부 선행 연구에서는 기능성 잉크를 활용하여 선택적 영역에 코팅 등의 새로운 분야로 확장하려는 노력이 있었다[2-4].
한편으로는 한 개 노즐을 사용하여 프린팅하기 때문에 프린팅 폭의 증대는 생산성을 결정하는 결정적인 요소가 된다. 가장 간단한 프린팅 폭 향상 방법으로는 액적을 충전시키는 펄스 전압 및 편향시키는 DC 전압의 크기를 증가시키는 것이다. 그러나, 전압 크기를 증가시키는 것은 액적 간 간섭 증가, 액적과 편향 전극간의 간섭, electrical breakdown 등의 문제가 발생할 수 있다.
이러한 문제로 본 연구에서는 양방향 편향 방식을 고려하였다. 기존에는 주로 사용하는 한쪽 방향으로만 편향이 이루어지는 단방향 편향을 사용하였는데, 이 방식은 근본적으로 프린팅 폭을 증대시키는데 한계가 있다.
본 연구에서는 실제 양방향 프린팅 방식이 응용될 수 있도록 하는 충전 전압 인가 방법, 제팅 가시화의 연구와 실험을 통하여 향후 이러한 개발 방향의 응용 가능성을 논의하려고 한다.
2. 연구방법
본 연구를 진행하기 위하여 연구용으로 Fig. 1과 같은 연속 잉크젯 실험장치를 개발하였다.
상용 연속 잉크젯 시스템은 1 L 이상의 많은 잉크의 연속 공급이 필요하기 때문에 다양한 잉크로 실험을 시도하기가 어려운 단점을 극복하기 위하여 소량으로 실험을 위한 연구용 장치를 개발하였다. 또한 제팅 현상을 가시화 하기 위하여 제팅 신호와 동기화된 Strobe light를 통한 Drop watcher를 개발하였다. 이를 통하여 일반 CCD camera(Basler acA-1300-60gc)를 사용하여 고속, 고주파 토출 현상을 가시화하는 것이 가능하였다. 프린트 헤드로는 상용화된 CIJ 헤드(Troy T7)를 구매하고 재가공하여 원하는 구조로 제작하였다. 기존 시스템과 완전히 다른 전압으로 구동하기 위하여 Fig. 2와 같이 전압 드라이브 시스템을 자체적으로 개발하였다. 개발된 시스템과 소프트웨어의 자세한 정보는 연구실에 출판된 기존의 참고논문 [1]을 참조 할 수 있다.
구체적인 전압 인가 방식은 연속 잉크젯 스트림(stream)을 고주파의 drop으로 분리하기 위한 가진 주파수(50 kHz 이상)를 발생시키고 가진하기 위하여 임의 파형 발생기(Keysight Agilent 33220A)와 고전압 증폭기(Trek PZD30)를 사용하였고, 충전을 위한 펄스 파형을 위하여 파형 생성기(Rcontrol FG1)를 사용하고 Amplifier(Trek PZD350)를 사용하여 증폭시켰다. 마지막으로 Deflection을 위한 고전압 전기장 생성을 위해 고전압 파워 서플라이를 사용하였다(ConverTech SHV 30R 10kV 3mA). 연속 잉크젯의 작동 원리와 구체적인 내용은 연구실에서 발표한 기존 논문을 참조할 수 있다[1].
본 연구에서 개발하려고 하는 양방향 프린팅 방법은 젯 스트림에서 편향 방법을 양쪽으로 넓혀서 프린팅의 폭을 단방향에 비해서 2배 정도 넓히려는 방식이다. 이를 위하여 프린팅되지 않는 액적을 Gutter로 보내야 되는데 이러한 Gutter 위치를 한쪽 방향으로 위치시켜야 하므로 프린팅 되지 않을 때 가장 큰 전압으로 충전 시켜야 되는 문제점이 있다.
양쪽 방향으로 편향 시켜서 폭을 넓히기 위해서는 충전의 극성이 +와 − 모두 존재해야 하기 때문에 한쪽 방향 편향 방식의 프린팅에 비해 난이도가 높다.
양방향 구현을 위해서는 충전 전극(charge electrode, charge plate)에 적절한 충전 전압을 인가하는 것이 매우 중요하다. 기존의 단방향 프린팅과는 달리 프린팅을 하지 않는 상태에서는 음의 DC전압인 Vdefault를 인가하여 항상 액적을 (+)로 충전시켜 Gutter를 통해 프린팅하지 않는 액적을 회수한다. 프린팅을 진행할 때는 원하는 프린팅 전압 범위에 따라 Vpulse를 적절히 설정하여 편향의 양을 조절한다.
단방향 프린팅을 위한 전압은 편향에 크기에 따라서 단계적으로 높아지는 Fig. 4(a)와 같은 전압을 사용하지만, 본 방법은 양방향의 편향을 위하여 (+) 와 (−) 전압을 모두 사용한다. 또한 토출을 하지 않을 때는 항상 (+) 전압이 유지되어야 하므로 이를 위하여 DAQ(데이터 획득 시스템)의 아날로그 출력 채널에서 DC 전압(Vdefault)을 출력시킨다. 프린팅 시에는 편향 전압을 출력시키기 위해 펄스 전압을 만들고 이것을 차동회로(Fig. 4(d))를 거치게 하여 DC+pulse 전압 형태로 구성하였다. 이러한 신호 레벨의 전압은 고전압 증폭기를 사용하여 작동 범위의 전압으로 증폭시켜준다.
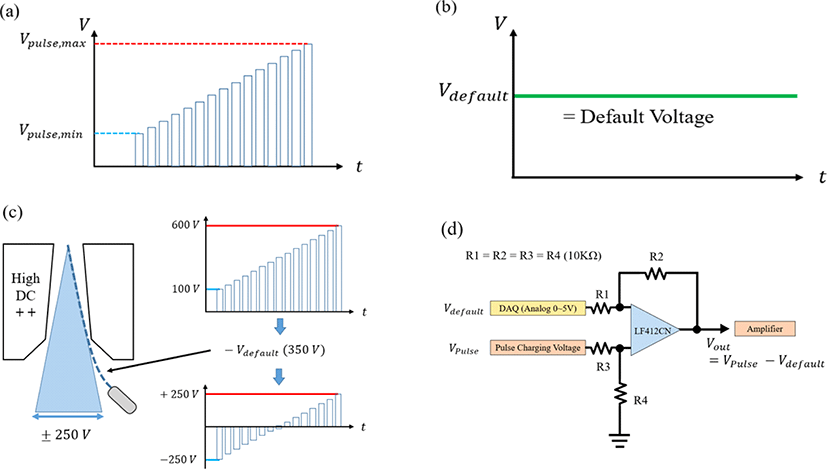
양방향 잉크젯 방법에서는 Deflection되어 회수되는 액적들이 Gutter의 위치와 형상에 따라 중요한 영향을 받는다. 만약 Gutter의 형상이 적절하지 못하다면 Deflection되는 액적들이 Gutter와 충돌하여 다른 액적들을 방해할 수 있다. 우리는 구부러진 스테인리스 튜브를 활용하여 이를 해결하였다. 스테인리스 튜브는 기존 Gutter 모양에 비해 접촉면이 적고 각도를 조절하는 데 용이하여 Gutter로서 적절한 역할을 수행할 수 있다.

Fig. 6은 CIJ 실험을 위해 구동 및 제어 소프트웨어를 개발한 것이다. Piezo 가진 주파수 및 진폭, Pulse voltage parameter 제어를 통한 제어를 모두 사용자 인터페이스 환경(graphical user interface, GUI)에서 액적 개수 및 디자인 변경, DC 전압 제어 등 다양한 parameter를 제어할 수 있다. 이후 가시화 이미지를 획득해 충전된 액적 간의 거동을 확인하고, 실제 프린팅을 통해 기판 위의 액적 탄착 결과물을 획득할 수 있다. 이러한 과정을 종합하여 문제점을 파악하고, 개선 아이디어를 도출할 수 있다.
연속 잉크젯 방법에서는 적절한 property를 갖는 잉크를 사용해야 한다. 위성 액적 제거 및 적절한 위치에서의 Break-up 과정을 위해서는 점도 및 표면장력을 제어할 수 있어야 하며, Charging 및 Deflection 과정을 위해서는 Conductivity가 필요하다. 장비의 성능 및 헤드 내부 상태에 따라 적절한 property가 다를 수 있다. 우리는 적합한 property를 가진 실험용 잉크가 필요하다. 테스트를 위한 잉크는 친환경 및 인체에 무해한 것도 중요하다. 이를 위하여 잉크젯에서 사용하는 표준 잉크 사용 및 친환경 Solvent를 사용하고, 적절한 전도성을 만들기 위하여 염화 나트륨을 소량 첨가하였다. 이 잉크의 측정된 물성은 Table 1과 같다.
Conductivity (μS/cm) | Viscosity (cPs) | Surface tension (dyne/cm) |
---|---|---|
16,70 | 2 | 28 |
3. 결과 및 고찰
먼저, 선형 펄스 파형을 이용하여 실험을 수행하였다. 선형 펄스 파형은 Fig. 4(c)에서처럼 ±250 V까지 전압 간격이 일정하게 증가하는 모양의 파형이다. 동일한 일정 간격의 펄스 전압을 인가하는 경우에는 동일한 간격의 폭을 갖는 프린팅 패턴을 얻을 수 있으나, 실제로는 Fig. 7의 프린팅 결과물과 같이 중앙에서 오른쪽 부근에 두껍게 줄이 생긴 탄착 패턴을 보인다. 이 현상을 설명하기 위하여 선형 펄스 전압을 인가하는 동안 편향 전극의 내부에서 액적들을 Fig. 8과 같이 가시화를 통해 확인할 수 있었다. 10개의 펄스 전압을 인가하였을 때 액적 중 하나가 다른 액적에 비해 큰 부피를 가진다. 이 원인은 양방향을 프린팅하기 위한 대전 전압의 극성 변화에 의한 것이다.

양방향 대전 현상을 규명하기 위한 첫 번째 방법으로 waveform을 양극과 음극 교차점을 기준으로 둘로 쪼개어 인가하였다. 해당 방법에 대한 실험 결과를 Fig. 9에서 보여주고 있는데, Positive pulse에 의해 (−)로 충전된 액적에서만 문제가 발생한다는 것을 확인할 수 있다.
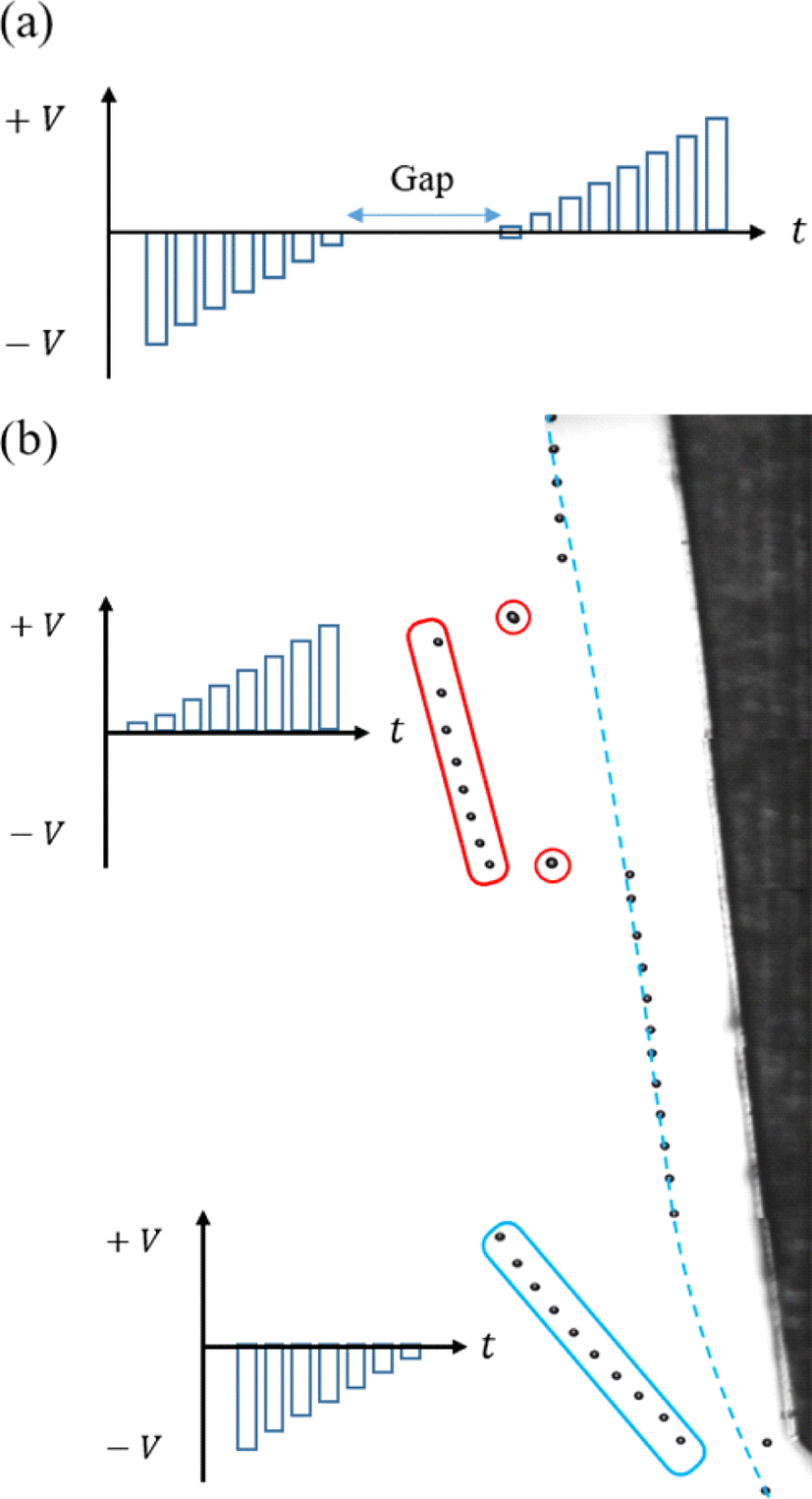
이러한 양방향 프린팅에 생기는 대전 현상을 규명하기 위한 두 번째 방식으로는 Strobe LED의 Delay를 이용하여 최초로 문제가 발생하는 위치를 추적하는 것이다. 헤드 이동을 통해 특정 위치의 가시화 이미지를 획득하는 방법으로 두 번째 방법에 대한 실험 결과를 Fig. 10에서 보여주고 있다. Fig. 10에서 Charging plate를 지나며 충전된 액적들은 Deflection plate에 진입하기 전부터 결합됨을 확인할 수 있다. 즉, Gutter로 보내기 위한 Default voltage에 의해 (+)로 충전된 액적과 인접한 (−)로 충전된 액적 사이의 인력에 의하여 액적이 결합되는 것을 확인하였다. 결합되는 과정은 Fig. 10에서 보다 명확히 알 수 있다.
Fig. 7∼Fig. 10까지의 분석 실험을 도출하여 파악한 대전시 생기는 문제점을 해결하기 위한 방법으로 시작과 끝부분의 액적에서 아이들 상태와 같은 극성의 전하가 만들어지도록 펄스 파형을 만드는 것이다. 이를 위하여 Fig. 11(a)와 같이 삼각형 모양의 파형을 만들어서 시작점과 끝점이 같은 극성을 갖도록 펄스 파형을 인가하였다. 이러한 결과로서 Fig. 11(b)와 같이 액적끼리 뭉침이 없이 프린팅이 가능하였다. 그러나 초기 drop인 경우 액적 간에 같은 전하의 반발력에 의해서 밀려나는 것을 보여줄 수 있다. 이러한 끝부분의 정밀도에 영향은 전체적으로 넓은 폭의 프린팅이 어렵게 만드는 원인이다. 그럼에도 불구하고 양방향 충전 방식은 프린팅 폭을 획기적으로 늘릴 수 있는 장점으로 다양한 응용에 활용이 가능할 것이다.
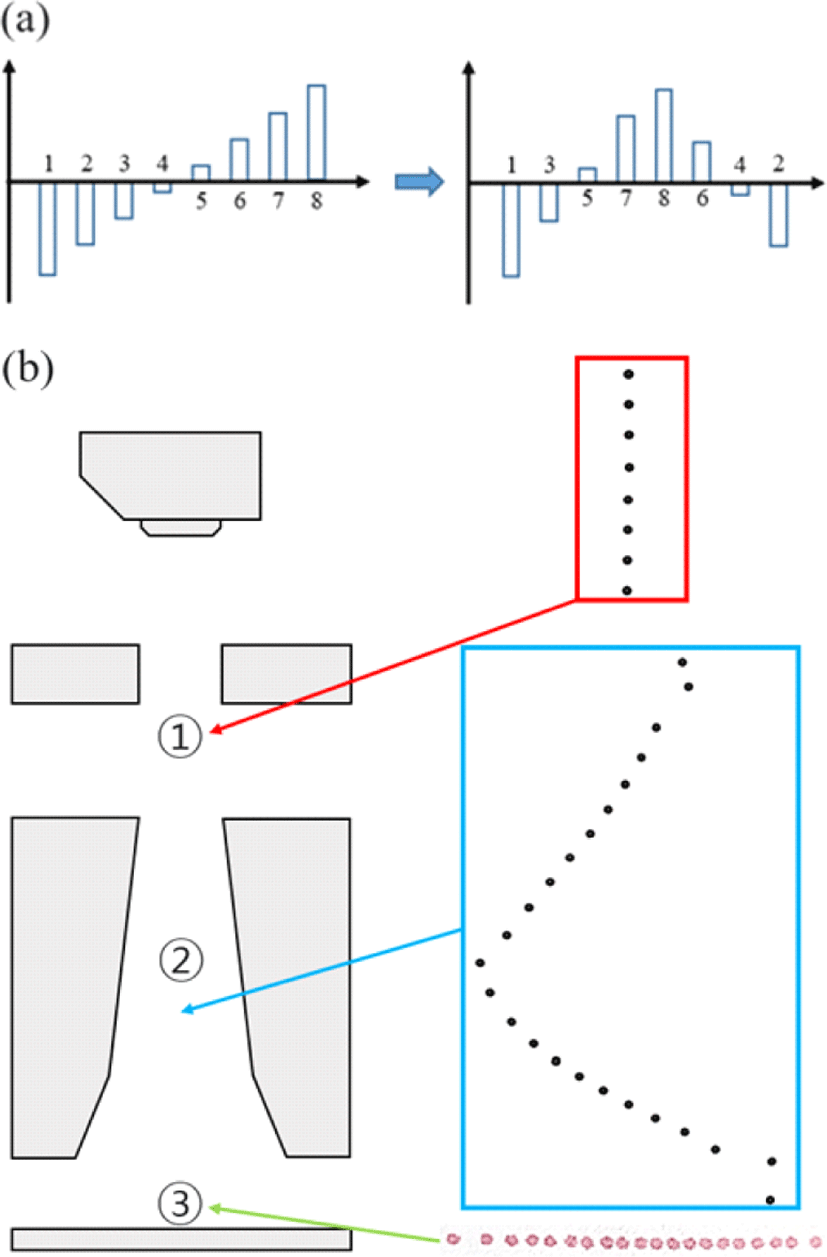
4. 결론
연속 잉크젯에서 프린팅 폭을 향상시키기 위하여 양방향 프린팅 방법을 위한 전압 인가 방식, 거터링 (Guttering) 방식, 전압인가 방법, 하드웨어 구성 방법에 대한 연구를 진행하였다.
양방향 프린팅을 위하여 프린팅하지 않는 액적인 경우 거터링을 위하여 회수하는데, Gutter의 설치 위치를 반드시 한쪽 방향 끝에 설치하게 되고, 항상 충전을 시켜 프린팅하게 된다. 프린팅할 때 이러한 거터링 방식의 문제점으로 기존처럼 전압을 증가시키면서 프린팅하면 향후 Gutter 전압으로 복귀할 때 반드시 극성의 변화가 커지게 된다. 이때 발생하는 인력으로 큰 drop이 생기게 되어 탄착점도 원하는 위치가 아닌 다른 위치에 프린팅하게 된다.
이러한 문제를 해결하기 위하여 삼각형 형태의 펄스 파형을 제안하였다. 다만 반발력에 의한 시작점과 끝점의 탄착점 정밀도에는 영향을 미치기 때문에 전하량을 늘리는 데 일부 제한이 있었다.