1. 서론
디스플레이는 컴퓨터와 모바일 기기의 개발과 발전에 따라 단순한 계산 값을 보여주는 정보 표시 기능을 넘어 다채로운 화상 정보를 현실감 있게 제공하도록 개발되었다. 특히, 메타버스 시대가 도래함에 따라 디스플레이는 착용 가능하면서도 증강 현실을 자연스럽게 표현하여야 하는 기술 수준까지 요구되고 있다. 한편, 디스플레이 기술이 진공의 벌크 타입 브라운관(cathode ray tube, CRT)에서 초박형의 평판형 디스플레이(flat panel display, FPD)로 발전해 옴에 따라 디스플레이의 초대화면화가 가능해졌고, 공간적 효율이 급격하게 증가하였다. 동시에 형태적으로 유연성을 확보할 수 있게 되어, 최근 수년 사이에는 말거나 접을 수 있는 폼팩터를 가진 대화면 텔레비전과 중소화면의 스마트기기가 대량생산되어 보급되기 시작했다. 이러한 유연성 확보에는 유기물 또는 고분자 소재가 매우 큰 견인차 역할을 해 왔으며, 제품으로 양산되어 보급되고 있는 디스플레이 또한 organic light-emitting diode (OLED) 디스플레이다. 이러한 유연 OLED 패널은 자유 곡면 상에 쉽게 붙일 수 있어 비교적 복잡하고 비평면형 표면이 많은 차량 내부의 디스플레이로 활용되기 시작하였다.
한편, 무기물 반도체 기반의 light-emitting diodes (LED)는 고효율, 장수명, 고휘도, 고온 안정성 등의 여러가지 우수한 물리적 성질 때문에 차세대 고휘도 고화질 디스플레이의 광원 및 화소 소재로 각광을 받고 있다[1,2]. 이러한 LED에는 III–V족 화합물 반도체가 있고, InAlGaP과 InGaN 계열의 에피박막 소재가 각각 고효율 적색과 녹청색을 발광하는데 사용되고 있다[3]. 그러나 일반적인 박막형 LED의 취성 때문에 유연성을 확보할 수 없어 유연 디스플레이 제작 및 응용으로의 한계가 있어 왔다. LED를 유연 디스플레이로 제작하기 위해서는 무기물 결정질 박막의 내재적 취성을 극복할 수 있는 LED 칩의 크기와 배열이 필수적이고, 휨, 굽힘, 스트레칭 등의 반복된 변형에도 구조적 안정성을 담보할 수 있는 기판, 인터커넥트(또는 전극), 구동소자 등에 기술적 도전이 필요하다[4,5].
본 고에서는 화합물 반도체 분야에서 최근 약 20여년간 유연 발광소자와 디스플레이 구현을 위해 여러 연구자들이 개발한 연구들을 요약하겠다. 특히, LED 구조, 에피택시, 기판, 집적, 구동회로 관점에서 리뷰하고, 장단점을 논하겠으며, 미래 디스플레이를 위한 기술적 챌린지에 대해 간략하게 논의하도록 하겠다.
2. 유연 디스플레이
반도체 및 발광소자를 매우 작게 만드는 방법의 하나로 나노와이어(또는 나노막대, 나노로드) 성장이 있다. 나노와이어는 직경이 수십~수백 나노미터 수준이고 길이가 수~수백 마이크로 미터로 종횡비가 매우 커 형태적으로 이방적인 나노소재이다. 따라서 수~수십 나노미터 크기의 거의 구형에 가까운 등방구조를 가지는 나노입자에 비해 기계적 또는 전기적으로 기판 상의 위치 및 방향 조작이 더 용이하여 어레이 형태의 소자를 제작하기 적합한 나노소재이다[6,7]. 일반적으로 나노와이어의 위치나 배향을 조절하는데 있어 원자힘 현미경의 팁에 의한 정밀한 위치조작, 유전영동법 내지는 나노와이어가 분산된 유체의 흐름을 이용한 배향조절과 같은 방법이 사용되었다[7]. 대조적으로 나노입자는 원자힘 현미경의 팁과 같은 기계적 조작 툴로 위치를 정하여 옮기기 매우 어렵고, 또한 유전영동법과 같은 외부 전기장으로 원하는 배향을 가지도록 하거나 위치를 조절하는 것이 매우 어렵다. 나노와이어는 직경이 매우 가늘어 기계적으로 탄성도가 높다. 이러한 이유로 비교적 초창기 유연 디스플레이 소자 연구에 있어 위치와 방향이 조절되고 유연성을 확보할 수 있는 나노와이어 LED가 활용되었다.
나노와이어 LED를 이용한 유연 디스플레이 제조는 용액 기반의 어셈블리 방법을 주로 사용하였고, 자세한 방법은 다음과 같다. 나노와이어 LED를 모기판(mother substrate)에서 성장한 후, 기계적인 힘을 가해 나노와이어 LED의 하단부를 부러뜨려 모기판에서 분리하고 분산성이 우수한 용매에 분산시켜 나노와이어 현탁 용액(suspension solution)을 제조한다[8]. 제조한 현탁액을 잉크처럼 사용해 유연기판 상에 분사한다. 이때 스핀코팅(spin-coating) 또는 드롭 캐스팅(drop-casting)을 하면 나노와이어가 불규칙하게 분산되고, 블레이드 코팅 또는 유체 이송법을 활용하게 되면 나노와이어들이 일정한 방향성을 가지고 분산된다. 일정한 방향성을 가지도록 나노와이어 어레이를 캐스팅한 후, 여기에 90도 각도로 교차하게 하여 다시 나노와이어들을 일방향 캐스팅 하게 되면 직교 교차된 기계적 접합을 만들 수 있다(Fig. 1(a)). 이후, 나노와이어 LED의 위치를 확인하고 전자빔 리소그래피(electron-beam lithography) 등의 전극 형성 공정을 거쳐 소자를 제조하게 된다. 이러한 나노와이어 LED 어셈블리에 의한 소자 제작 방식은 모기판의 제약을 받지 않고, 서로 다른 물성이나 기능을 가지는 혹은 성장법이 다른 각각의 나노와이어들을 한 기판에 이종접합 집적할 수 있다는 점에서 장점을 가진다.
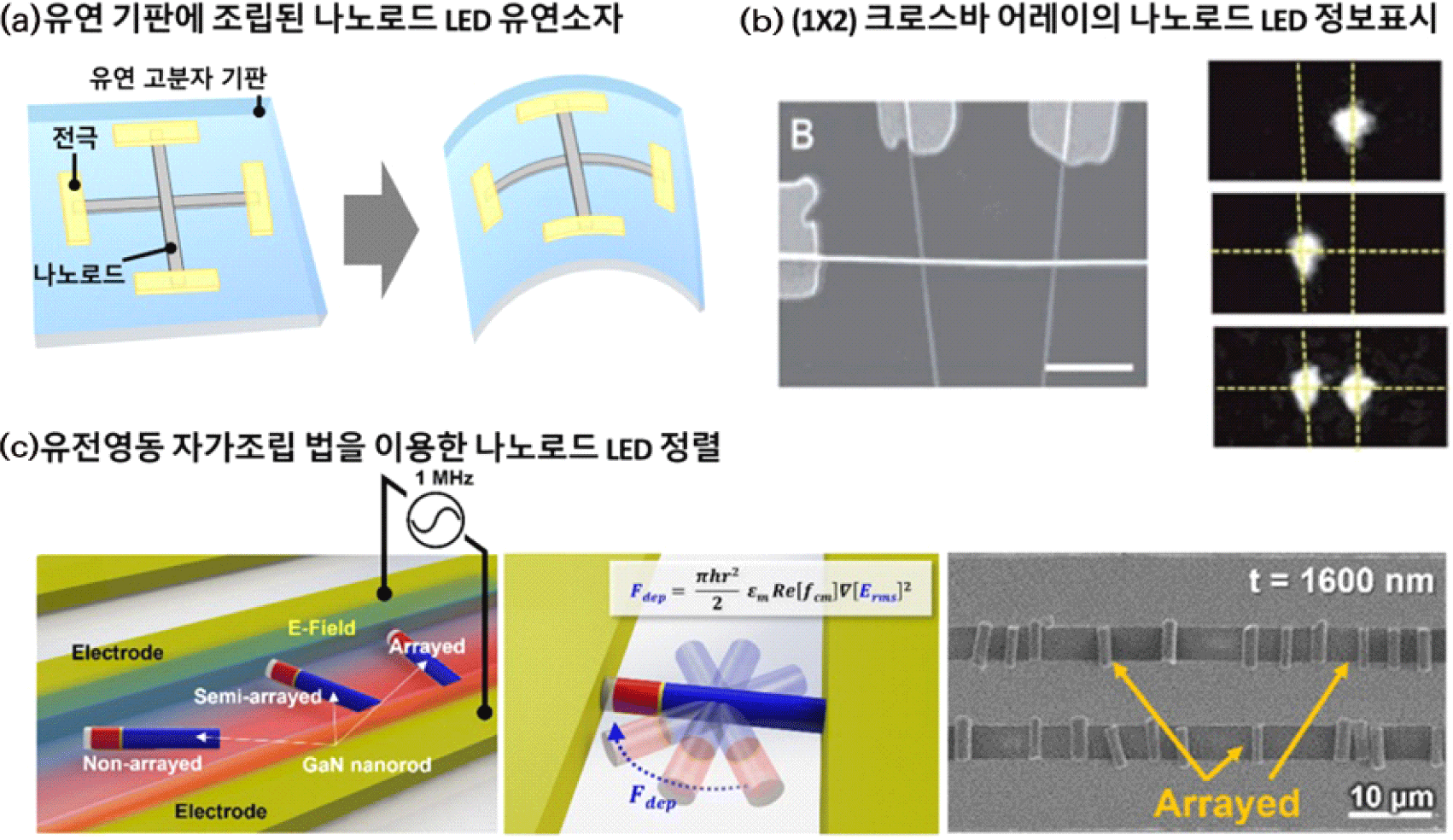
2003년 하버드대 연구팀은 전술한 장점을 이용해 n-타입 GaN 나노와이어와 p-타입 Si 나노와이어를 각각 성장시킨 후 유연한 고분자 플라스틱 기판에 크로스바 형태로 이종집적하고 전극을 형성해 (1×2) 행렬 접점 어레이의 p/n-이종접합 나노와이어 LED를 제작했다(Fig. 1(b))[8]. 서로 직교 접합한 두 나노와이어(p-Si 및 n-GaN)에 전류를 주입함으로써 나노와이어 크로스바 접합부에서 전류주입발광(electroluminescence)을 얻을 수 있었다. 또한 두 개의 평행한 나노와이어에 전류를 개별적으로 주입함으로써, 두 접합의 발광을 조절하여 개별 구동이 가능함을 입증하여, 화소로 활용될 수 있는 가능성을 입증하였다. 뿐만 아니라 반복적인 휨 사이클 테스트에서도 나노와이어 LED 어레이의 정보표시 소자가 안정적으로 작동함을 보였다. 한편, 이러한 방식의 나노와이어 정보 표시 방식은 고밀도로 나노와이어를 배치하고 정확하게 전극을 형성하는 것이 매우 어렵고 시간이 많이 소요되어 고해상도의 디스플레이를 대량으로 제조하는 데 적합하지는 않다[9].
한편, 국민대 연구팀은 위의 단점들을 극복하는 유전영동 자기조립법을 개발하여 고밀도 어레이화 및 대량 고수율 디스플레이 생산 가능성을 열었다[10,11]. 유전영동 자기조립법은 나노와이어를 무작위적으로 또는 유체에 의존하여 방향성만 대략적으로 조절하는 기존의 나노와이어 어셈블리와는 달리 미리 형성된 전극 패턴상에 나노와이어를 국부적으로 잉크-젯팅하여 국소적으로 분산시키고 전극에 교류 전기장을 걸어 고밀도의 나노와이어를 두 전극 사이에 일방향으로 정렬하고 접합을 시켜 디스플레이로 제작하는 방법이다(Fig. 1(c)). 따라서 해당 방법을 유연 기판에 적용하게 되면 고수율, 고해상도, 대면적으로 유연 디스플레이를 제작할 수 있을 것으로 기대된다.
에피택시는 고성능 고체 전자소자(solid-state electronics) 제작의 근간 기술로써 단결정성(mono-crystallinity)을 가지는 반도체 박막을 이종의 웨이퍼에 제조하는 방법이다[12]. 일반적으로 LED 디스플레이에 사용되는 화합물 반도체(e.g., 적색-AlGaInP계 및 청, 녹색-InGaN계)는 무기물 재료의 취성(brittleness)으로 인해 굽힘(bending), 늘림(stretching) 또는 동적 변형(dynamic deformation)에 대해 균열(crack)이나 파단(fracture)과 같은 영구적 손상이 야기된다(Fig. 2(a)). 따라서 박막 형태의 소자는 유연 디스플레이 제조에 직접 사용될 수는 없고, 신축성이나 유연성을 가질 수 있는 크기 또는 형태로의 가공이 필요하다. 이를 위해서는 작은 칩의 어레이가 적합하며 이를 이송기판(또는 인터포저라고 불리움)을 통해 유연 기판 상에 옮기는 방법이 주로 사용된다[13].
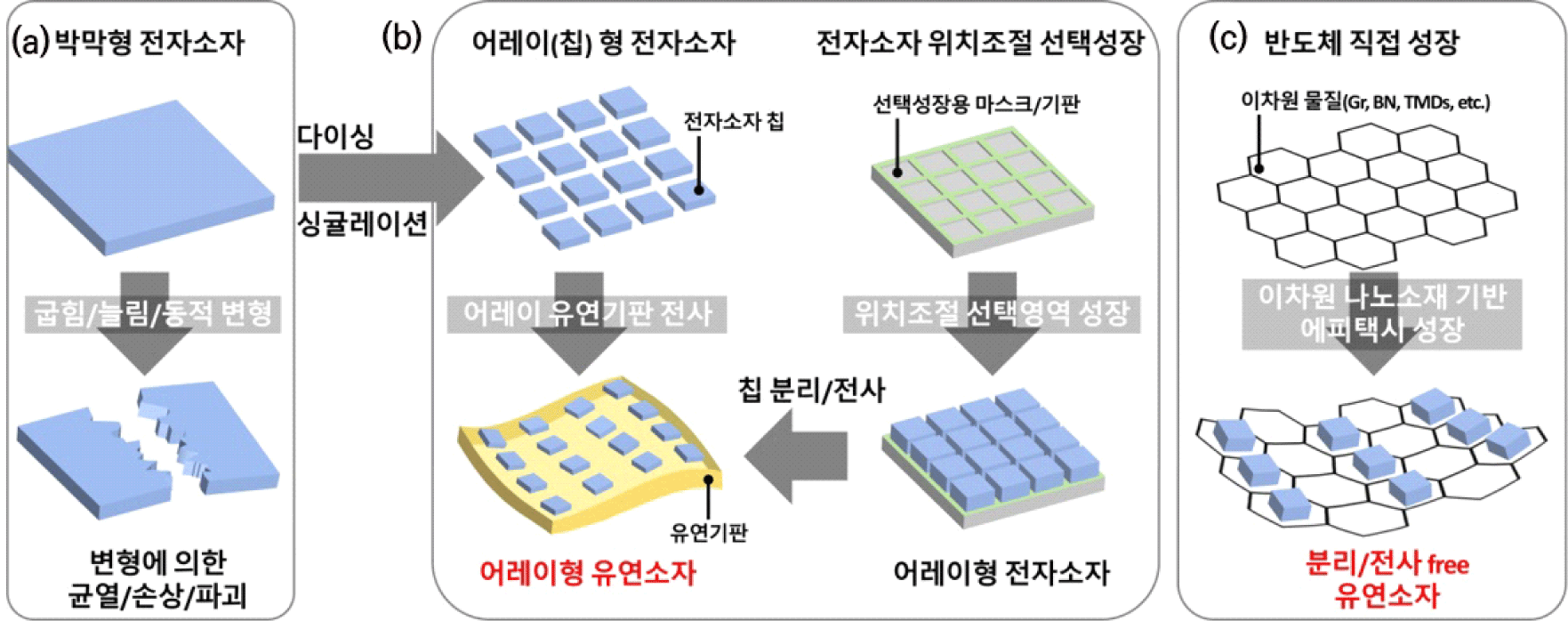
LED를 칩 어레이 형태로 제작하는 방법은 크게 두 가지가 있다. 첫째, 박막-on-웨이퍼 형태의 LED를 톱이나 레이저와 같은 물리적 방법 또는 에칭과 같은 화학적 방법을 이용해 작은 칩 형태로 나누고 기판을 제거하는 과정, 둘째, 패터닝이 된 기판 상에 위치조절 선택성장법을 이용해 원하는 크기와 어레이로 LED 자체를 성장하는 방법이 있다(Fig. 2(b))[14,15]. 두 가지 방법 모두 각각의 장점을 지니고 있으나 결과적으로 칩 어레이 형태의 제조, 모(母)기판 분리 및 유연기판으로의 전사공정이 필수적이다. 이러한 전사 공정은 전사 정확도가 높지 않아 수율이 낮고, 전사 속도도 빠르지 않아 생산성이 낮은 편이다. 이를 ㈜삼성전자의 갤럭시 S24 평판 디스플레이(6.78 인치, ~500 PPI)를 기준으로 삼아 LED 칩을 유연기판으로 전사할 경우, 픽셀의 개수가 약 4,500,000개이고, 전사수율이 99.999 %일 때 픽셀 결함이 약 50개, 초당 1,000개의 픽셀 전사속도일 때 전사공정이 1시간 이상 소요되고, 현재 기술 수준에서 분당 1~2개의 픽셀 리페어 공정이 가능함을 감안하면, 최종적으로 스마트폰 수준의 디스플레이 한 개를 생산하는데 약 1.5시간 이상이 소요된다. 수율이나 생산속도 면에 있어 기존의 평판 디스플레이인 LCD, OLED에 비견될 수 없다. 따라서, 기존 LED 소자를 유연기판으로 옮겨 유연소자를 제조할 경우에는 전사수율이 매우 높아야 하고, 전사속도가 빠른 공정(e.g., 롤-to-플레이트 공정은 초당 수만 개의 마이크로 LED 전사 가능)이 필수적이다. 또는 전사를 필요로 하지 않는 유연 기판으로의 LED 직성장이 바람직할 수 있다.
이차원 나노소재(e.g., 그래핀, 질화붕소 등)에서 반도체 물질을 직접 성장시키는 이차원 나노소재 기반의 에피택시법(i.e., 반 데어 발스 에피택시, 원격 에피택시)의 경우, 기판을 그래핀과 같이 원자층 수준으로 얇고 매우 유연한 이차원 물질을 사용하기 때문에 추가적인 공정 없이 유연소자 제조가 가능하다(Fig. 2(c)) [16,17]. 이차원 나노소재 기반의 에피택시법은 기판과 에피택시 층 사이에 직접적인 공유 또는 이온결합을 형성하지 않고 약한 반 데어 발스(van der Waals, vdW) 결합 또는 하부기판과 상부 에피층 사이에 원격 상호 작용력(remote interacting force) 만이 존재하기 때문에 일반적인 접착 테이프로도 에피택시층을 기판으로부터 손쉽게 분리할 수 있다는 특징을 가진다[18,19]. 따라서, 유연 디스플레이 제조를 위해 기존처럼 단단하고 두꺼운 모기판의 분리 또는 제거, 그리고 소자 전사공정이 필요없다[6,16,17,20]. 다만, 구동회로(backplane circuits) 상에 분리된 에피택시층을 이종집적 또는 본딩하거나, 반대로 구동회로를 에피택시층에 직접 형성하여야 한다. 이와 관련된 자세한 내용은 뒤에 2.5.절에서 소개하겠다. 이처럼 이차원 나노소재 기반의 에피택시 방법은 분리/전사를 최소화하거나 필요로 하지 않는 유연 디스플레이 제조방법으로서 웨이퍼 처리량(through-put), 공정단계 및 비용을 크게 절감할 수 있는 차세대 공정 방법이다.
나노 에피택시는 수십에서 수백 나노미터 크기의 상호 이격된 단결정 반도체 구조물들을 에피택시로 기판에 제조하는 방법으로써 유연 디스플레이 제조에 있어 다양한 장점을 가진다. 대표적으로 두 가지 방법이 있다. 하나는 성장 모드를 조절하여 결정이 한 방향으로만 성장하도록 함으로써 무작위 위치에서 나노와이어와 같은 나노소재를 에피택시하는 방법이고[21], 다른 하나는 나노소재를 원하는 위치 또는 영역에만 선택에피성장을 하는 것으로[22-24], 이를 선택성장 나노에피라고 한다. 전자소자 및 디스플레이 응용을 위해서는 선택성장 나노에피 방법이 훨씬 바람직하다고 할 수 있겠다. 선택성장 나노에피 방법에 대한 논의는 2.4.절에서 설명하고자 한다. 나노 에피택시는 기존의 벌크(또는 박막) 에피택시와 마찬가지로 동일한 방식의 성장방법과 장치를 이용하기 때문에 합성을 위한 추가적인 전구체 및 장비 없이 기존 화합물 반도체 성장 공정 인프라를 그대로 활용할 수 있다. 또한 위치가 조절되어 선택성장된 반도체 어레이는 매트릭스-어드레서블 패터닝을 기반으로 하는 포토리소그래피, 건식식각 및 증착공정 등 기존의 반도체 전공정을 그대로 적용할 수 있기 때문에 정교한 초미세 공정을 활용할 수 있다(Fig. 3(a))[25,26].
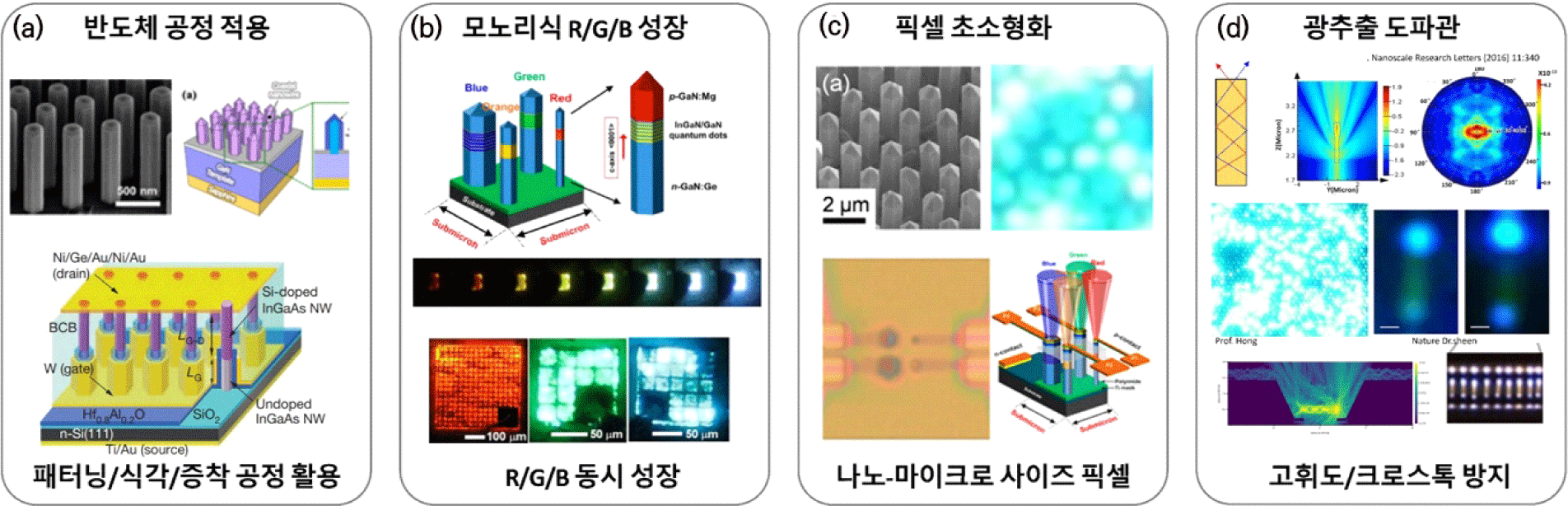
또한, 바텀-업 방식의 위치조절 선택성장법이나 탑-다운 방식의 수직 식각법을 이용해 나노와이어의 직경과 간격을 조절하여 제조할 경우, 한 웨이퍼 내에서 적/녹/청색을 모두 구현할 수 있다는 장점을 지닌다(Fig. 3(b)) [26-28]. 나노와이어의 간격 및 직경을 한 기판에 다양하게 패터닝하게 되면 선택성장 시 간격과 직경에 따라 양자우물의 인듐 조성이 달라진다. 이러한 현상을 활용하게 되면 한 기판에 적, 녹, 청의 전류주입 발광의 나노와이어 LED를 제조할 수 있게 된다. 뿐만 아니라 인듐이 과량으로 들어간 적색 발광의 LED 박막을 수직 식각하여 나노와이어를 제작할 때 나노와이어의 직경을 가늘게 하면 질화갈륨/질화인듐갈륨 양자우물 구조의 응력 완화가 효과적으로 이뤄지면서 양자구속 스타크 효과(quantum-confined Stark effect)의 완화에 따른 밴드갭의 청색편이 현상이 일어난다[27]. 따라서 나노와이어의 두께를 달리 함에 따라 또한 적, 녹, 청색 발광의 나노와이어 LED를 제작할 수 있다.
수직 나노와이어 어레이는 유연디스플레이 제조에 있어 구조적으로 큰 장점을 지닌다. 나노와이어는 직경이 매우 작아 하부의 기판과의 접촉 면적이 매우 협소하기 때문에 기판의 휨 변형에 따른 나노와이어/기판의 응력 발생을 충분히 수용할 수 있다. 따라서 나노와이어-on-연성기판의 곡률 및 굽힘반경을 수 밀리미터 이내 수준으로 접을 수 있을 수 있고, 나노와이어 구조체간에 공간적으로 서로 이격되어 있기 때문에 기계적, 전기적 상호간섭 없이 자유롭게 굽힘, 수축 및 늘림의 변형을 구조적 손상 없이 할 수 있다[16,17,29].
또 다른 장점은 픽셀의 초소형화이다(Fig. 3(c)). 수십 마이크로미터 크기의 픽셀에는 고밀도 나노와이어 LED가 수 백~수 천개를 포함할 수 있고, 픽셀 크기를 줄임에 따라 나노와이어 갯수만 감소시키면 된다. 그리고 이상적으로는 개별 나노와이어 LED를 픽셀로 사용할 수도 있다[26]. 이때 가장 중요한 기술은 나노와이어 LED 성능의 균일도 확보에 있다. 이를 위해서는 전기적으로 턴-온 전압, 온-저항, 밝기 등에 있어 동일한 성능을 가져야 할 것이다.
한편, 픽셀의 초소형화와 더불어 나노와이어 LED 군집 픽셀의 장점은 픽셀간 성능 균일도 제고에 있다. 아무래도 큰 크기의 픽셀에는 수 백~수 천개의 나노와이어 LED가 포함되어 있기 때문에 개별 나노와이어의 밝기 차이는 군집의 평균화(ensemble average) 효과로 인해 픽셀간 균일도에 크게 영향을 주지 않는다. 또한 작동하지 않는 결함 나노와이어 LED가 몇 개 있더라도 화소 전체의 전기적, 광학적 성능에 크게 영향을 미치지 않으므로 자체적으로 빌트-인 리던던시(built-in redundancy) 효과를 가진다. 따라서 기존 박막칩 LED로 디스플레이를 만들 때 보다 불량에 의한 리워크 공정이 필요하지 않게 되어 디스플레이 제조공정에 큰 잇점이 있다.
마지막으로 나노와이어 LED는 종횡비가 큰 막대 형태이기 때문에 자체로 광추출도파관 역할을 하며 나노와이어의 팁에서 광추출효율이 매우 우수하다(Fig. 3(d))[30-33]. 이는 박막 LED와 대별되는 다른 점인데, 박막 LED는 브루스터 임계각(Brewster angle) 보다 크게 방출되려고 하는 빛은 박막 내부에 갖히게(trapped) 된다. 이 때문에 상당량의 빛이 칩 내부에 트랩되어 흡수되면서 광추출 효율이 떨어진다. 이러한 이유로 박막형 LED는 에칭을 통해 표면을 거칠게 하거나 또는 패터닝된 사파이어(patterned sapphire substrate, PSS)를 사용하여 광추출효율(light extraction efficiency)을 증대시킨다. 나노와이어 LED는 광추출효율을 증가시키기 위해 추가적인 공정이나 특별한 기판소재를 필요로 하지 않기 때문에 고효율 광원으로 적합하다. 뿐만 아니라 빛 방출 방향성이 우수하여 디스플레이에서 혼색 현상의 원인인 공간적 크로스톡 현상을 방지할 수 있다. 이러한 장점은 안경형 augmented reality (AR) 기기의 프로젝션형의 디스플레이에 활용될 수 있다[34].
이전 2.2.절에서 전술한 것처럼 LED 구조를 다이싱(dicing 또는 chip singulation) 공정을 통해 칩 형태로 제조 후, 유연기판에 전사하여 정렬, 배치, 조립하는 것은 여러 가지 어려움을 야기한다. 칩 제조 시 다이싱 및 모기판 제거에 의한 소자의 표면 및 손상뿐만 아니라 유연기판으로의 전사 시 위치 정확도, 수율 등 공정적인 문제로 인한 단점이 있다[35,36]. 따라서 어레이 형태로 반도체 물질을 성장하고 에칭 없이 어레이 자체를 활용하는 방식이 전사법에 의한 문제들을 해결할 수 있는 방법론을 제공할 수 있다[37].
위치조절 선택성장법은 모기판에 에피택시 성장이 이루어지지 않고 공정 분위기에 강한 산화규소(SiOx)와 같은 선택성이 있는 물질을 증착하고 에피택시가 이루어질 부분만 개구부 패턴(opening pattern)을 형성하여 원하는 위치 또는 영역에서만 선택적으로 반도체 물질을 증착 제조하는 방법이다(Fig. 4(a)). 이러한 방
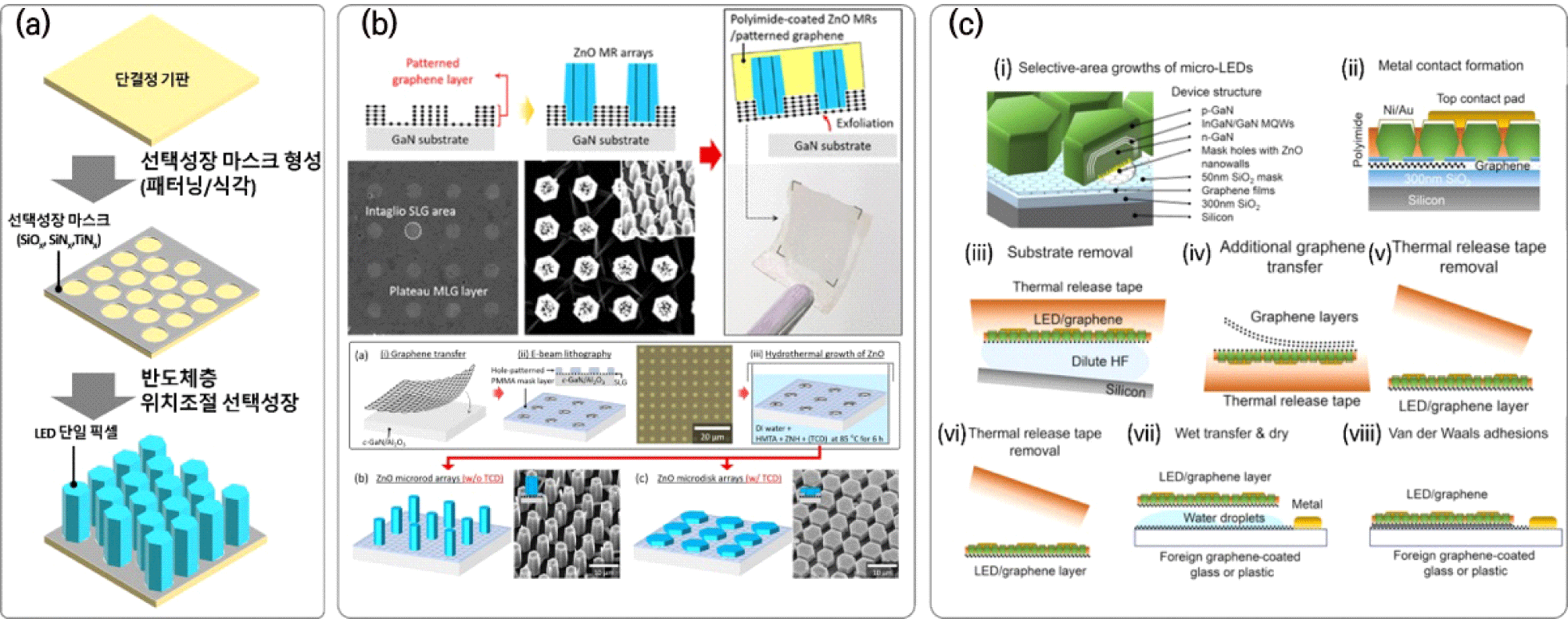
식은 포토리소그래피 및 식각공정을 통해 개구부의 패터닝 형상을 조절하고, 원하는 구동 소자의 크기와 형상에 맞춰 반도체 에피 구조물 어레이를 형성할 수 있게 한다[38]. 에피 구조물이 나노구조체인 경우, 2.3.절에서 기술한 선택성장 나노에피에 해당된다. 이 방법은 칩 형성(chip singulation) 공정 없이 공간적으로 이격된 소자 어레이를 형성할 수 있는 장점을 지니지만, 한편 기판 제거 및 전사공정 자체를 피할 수는 없다[39].
2차원 소재를 이용한 비공유결합 에피택시(i.e., 반 데어 발스 에피택시, 원격 에피택시) 방법으로 반도체 물질의 선택성장을 수행하게 되면 칩 형성 및 모기판 제거공정(ex. 그라인딩, 레이저 리프트-오프, 기판식각 등)을 거치지 않아도 유연 디스플레이의 제조가 가능하다[40-42]. 이러한 이차원 나노소재 기반의 에피택
시법을 이용한 선택성장법은 기존 공유결합 에피택시와 그 방법이 크게 다르지 않고, 2차원 소재를 기판으로 사용한다는 점에서 다르다. 기 에피택시법과 동일한 방식을 사용하는데, 2차원 물질이 코팅된 기판 상에 선택성장 마스크를 형성하고 비공유결합 에피택시 성장을 수행하면 위치나 형상을 조절하여 반도체 물질을 제조할 수 있다[39,43]. 이렇게 제조된 반도체 물질은 기판과 1차 화학결합(i.e., 공유결합, 이온결합)이 없어 손쉽게 분리될 수 있고, 분리한 필름은 자유자재로 굽히거나 휠 수 있다(Fig. 4(b))[39,43]. 예를 들어, 마이크론 크기의 구조물을 선택성장하고 에피구조물 사이를 고분자로 채우고, 필름 형태의 고분자/에피구조물을 테이프로 떼어낸다. 이차원 물질을 사용하는 경우 비공유결합 에피택시가 가능하기 때문에 레이저 리프트-오프나 화학적 식각 공정 없이 테이프 등과 같은 점착 물질을 사용하여 유연기판으로의 손쉬운 전사가 가능하다. 일반적으로 반도체층을 기판과 접합하는 방식은 열과 압력, 그리고 화학 반응을 통해 원자수준에서 계면에 강제적으로 강한 화학결합을 형성하는 것이다. 하지만 유연 디스플레이의 경우 대게 유연기판 자체가 열에 약한 고분자 기반의 물질이기 때문에 고온을 필요로 하는 에피택시 공정 또는 에피층의 기판으로의 본딩이 어렵고, 추가적인 점착층 없이는 유연기판과 유연소자층을 접합하기 어렵다. 하지만 신개념 에피택시를 기반으로 분리된 필름은 접합층이나 접합 공정 없이 이차원 물질의 반 데어 발스 힘을 이용하여 유연기판 상에 쉽게 전사할 수 있다는 장점을 지닌다(Fig. 4(c))[44]. 그리고 반복적인 변형에도 안정적으로 유연기판에 잘 점착되어 있음이 보고되었다. 따라서 위치조절 선택성장법은 칩 다이싱과 기판 및 소자 손상을 야기하는 리프트-오프 공정 없이 어레이 형태의 반도체 소자를 원하는 형상과 위치, 배열로 제작하는 방법으로 유연소자 제작에 응용할 수 있는 방법이라 할 수 있다.
디스플레이는 삼원색 R, G, B의 혼색으로 총천연색을 표현한다. LED는 자체발광화소(self-emissive pixel)이기 때문에 R, G, B 서브픽셀을 동일 평면상에 배치할 수 있고 또는 수직 적층형으로도 조립할 수 있다. 후자의 경우에는 동일한 서브픽셀 크기로도 훨씬 작은 픽셀 면적이 요구되므로 고해상도 디스플레이에 적합하나 공정과 구조의 난이도가 높다[45]. 이러한 이유로 높은 수율과 비용 절감을 위해 수평 배열의 디스플레이를 주로 제작한다[46].
LED 디스플레이는 R, G, B 칩의 전극을 인쇄 회로기판 또는 박막 트랜지스터의 전극과 접속해 주는 실장 공정이 필수이다. 이를 위해서는 에피택시 공정 이후 두가지 방식을 통해 제조된다(Fig. 5(a)~Fig. 5(c)). 먼저, R, G, B LED를 에피택시로 웨이퍼에 성장한 후(Fig. 5(a)), 단색의 서브픽셀 칩을 만들고 이를 원래 웨이퍼에서 1차 캐리어 기판(또는 인터포저)으로 옮긴다. 그리고 2차 캐리어 기판에는 1차 단색 인터포저로부터 R, G, B를 합친 어레이 형식으로 옮긴다. 그리고 이 2차 인터포저에서 백플레인 회로가 있는 기판에 이송하여 대량(mass-transfer) 전사한다(Fig. 5(b)). 이때 LED의 전극이 하부의 백플레인 기판과 정확하게 정렬되도록 전사 접합하여 컨택이 형성되어야 한다. 이 경우에는 LED 칩의 전극이 아래로 향하게 하여 구동회로에 직접 접촉을 형성하는 페이스-다운(face-down, 전극이 아래로 향하는 형태) 전사 조립 방식이 많이 쓰이나, 때로는 페이스-업(face-up) 형태로 배열한 후에 추가적인 인터커넥트 형성 공정(Fan-out 공정이라고 명명하기도 함)을 하기도 한다.
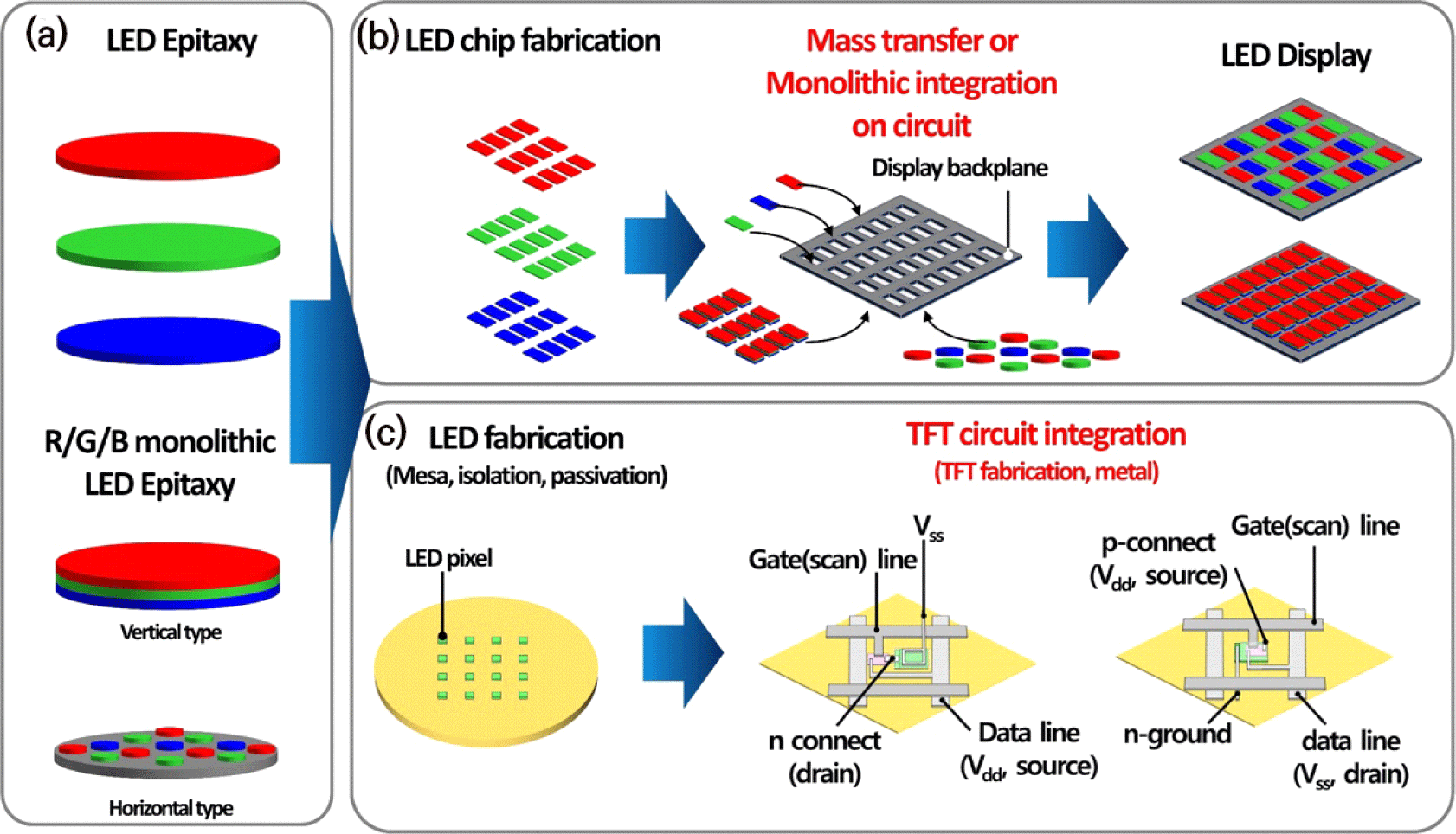
또 다른 집적 방식은 LED 칩의 어레이에 박막 트랜지스터를 형성하고 이를 패터닝한 후 배선을 형성하여 디스플레이를 제작하는 것이다(Fig. 5(c)). 트랜지스터를 LED 칩과 동일한 평면 또는 LED 칩 위에 배치할 수 있다. 같은 평면 상에 배치할 경우 스캔 라인으로 게이팅되는 트랜지스터의 소스가 수직의 데이터 라인과 연결되어 있고, 드레인을 통해 n-전극에 전류가 주입되며, p-전극은 접지된다(Fig. 5(c) 가운데). LED는 고온에서 안정하므로 LED 칩 위에 low-temperature polycrystalline oxide(LTPO)와 같은 트랜지스터를 형성할 수 있다. LED칩의 p-전극 표면 위에 트랜지스터를 형성하는데, 이는 소스와 컨택된다. 그리고 드레인이 데이터 라인으로 연결된다. 이에 따라, LED는 상부의 p-타입이 트랜지스터와 연결되고, n-전극은 그라운드가 되는 소자 지오메트리가 된다(Fig. 5(c) 오른쪽).
유연 디스플레이 제작을 위해서는 LED와 구동회로를 유연한 기판에 형성하거나 집적하는 것이 필요하다. 또한 반복적인 변형에도 기계적 안정성을 유지하기 위해서는 이에 맞는 전극구조(e.g., serpentine 구조를 가지는 금속전극)가 필요하다[47]. 대량 전사법 중 하나인 롤-투-플레이트(roll-to-plate) 전사법으로 실리콘 박막 트랜지스터 어레이를 유리 기판에 옮기고, 두 번째 롤 공정으로 LED 칩을 전사한다. 그리고 집적 공정을 거치면서 연성을 가지는 전극구조를 형성하고 이를 유연 기판에 전사하여 옮기게 되면 스트레칭이 가능한 디스플레이 제작이 가능하다(Fig. 6(a))[48]. 또 다른 방법으로는 탄성체(elastomer)를 이용한 스탬프 전사 프린팅(stamp transfer printing) 방식을 이용할 수 있다. 유연 기판 상에 트랜지스터 및 1차 전극구조를 형성하고 미리 제조해둔 LED 칩을 polydimethylsiloxane (PDMS)와 같은 탄성체를 이용하여 기판으로부터 떼어낸다. 그리고 1차전극 구조의 유연 기판상에 원하는 위치에 도장을 찍듯이 스탬핑하여 LED를 전사할 수 있다. 이후 2차 전극공정을 통해 배선공정을 마무리하면 PM 및 AM 구조를 만들어 디스플레이 구동이 가능하다(Fig. 6(b))[49].
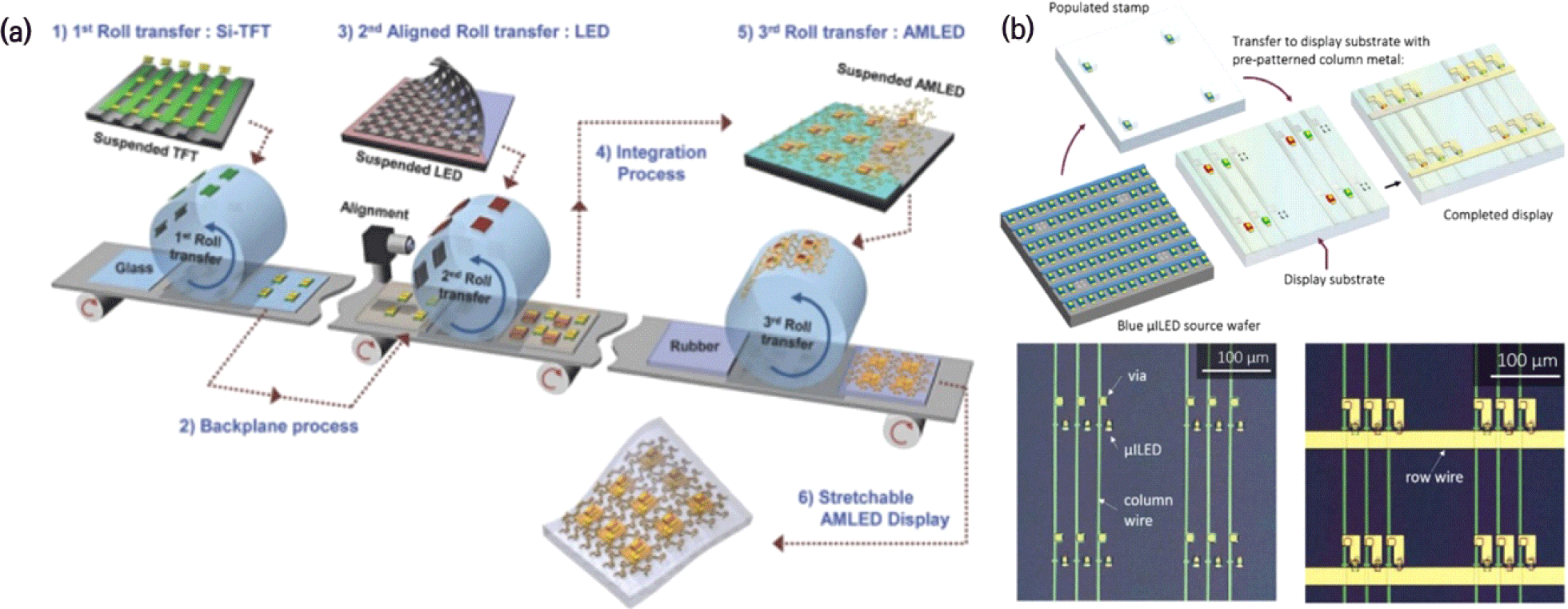
최근에는 2차원 나노소재를 구동소자로 하여 LED 디스플레이가 구현되었다[50]. LED-on-Si 기판에 MoS2를 직성장시키고 포토리소그래피 패터닝을 하여 소스를 p-전극에 접속하고, 드레인과 게이트를 형성한다. 그리고 게이트를 스캔 라인으로, 그리고 드레인을 데이터 라인으로 만드는 추가 구조를 위한 공정을 수행하게 되면 MoS2의 전계효과 트랜지스터로 고밀도 LED 디스플레이 구현이 가능하다. MoS2는 2차원 나노소재로 가시광에 대해 투명도가 높고, 따라서 LED 위에 집적하여도 광흡수에 의한 손실이 적다는 장점을 가지고 있고, LED 위에 수직으로 집적되어 있기 때문에 추가적인 유연 전극 구조를 필요로 하지 않는다는 점에서 유연 LED 디스플레이를 위한 바람직한 트랜지스터 소재 및 구조라 할 수 있다(Fig. 7).
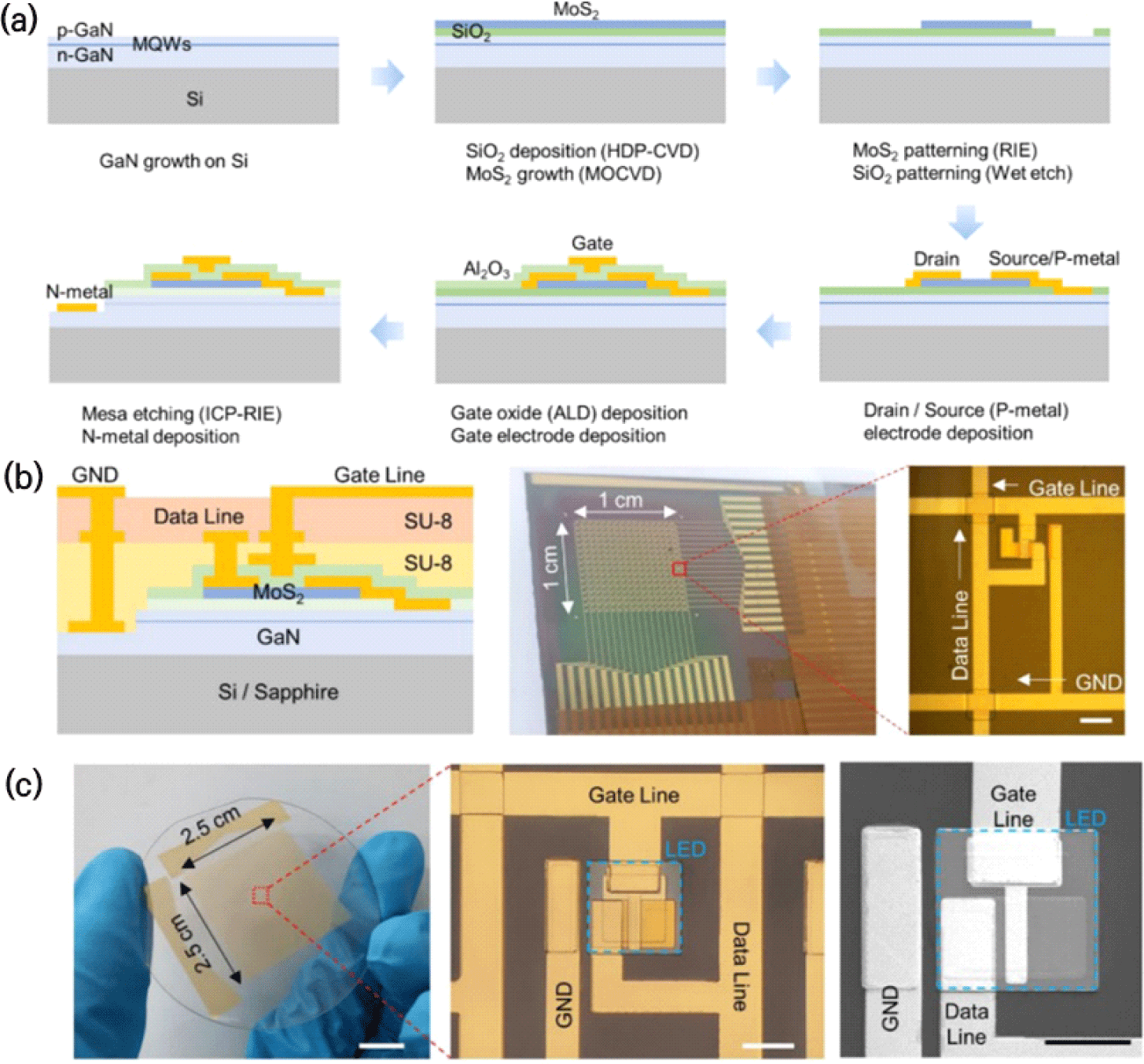
3. 요약 및 전망
반도체 LED를 기반으로 한 유연 소자 및 디스플레이 제작에 대해 간단하게 리뷰하였다. LED는 나노와이어, 박막 칩의 대표적인 두가지 광원 형태가 있고, 이를 화소로 조립하여 디스플레이로 제작하는 방법에 대해 정리하였다. 나노와이어는 성장된 모기판으로부터 분리한 후 원하는 백플레인 기판 상에 유체이송 및 유전영동법으로 어셈블리 하는 방법이 있었다. 특히 유전영동법은 전극을 미리 형성하고 전극에 나노와이어를 고밀도로 접속시키는, 대면적 저비용 조립에 유리한 디스플레이 제조 방법이다(2.1.절). 한편, 수직 나노와이어를 원하는 위치와 배열로 에피택시로 형성하고, 반도체 공정을 이용하여 화소구조를 구현하는 방법이 있다. 수직 나노와이어 어레이는 반도체 공정을 이용할 뿐만 아니라 나노와이어 군집을 화소로 이용하기 때문에 구조적인 빌트-인 리던던시를 활용할 수 있고, 한 기판에 R, G, B 모두 형성할 수 있다는 점에서 고해상도 디스플레이를 위한 미래지향적 방법론을 제공한다고 할 수 있다(2.3.절). 그러나 고온에 취약한 유연 기판에 직접 에피택시를 하기 어렵다는 점에서 유연 디스플레이 제작에 있어 한계가 있다.
박막 칩 형태의 LED를 디스플레이로 제작하기 위해서는 다이싱과 웨이퍼 제거 후 유연 기판에 형성된 백플레인 회로 상으로 집적을 해야 한다. 이때, 전사 정렬도가 수율에 직접적으로 영향을 미치고 생산 단가에 결정적인 영향을 미친다(2.2.절). 전사를 최소화하는 방법으로는 나노미터 두께의 2차원 나노소재 상에 LED를 선택성장 하는 방법이 있다. 2차원 나노소재는 표면에 비결합 전자쌍이 존재하지 않기 때문에 2차원 나노소재와 에피층 사이에 공유결합이나 이온결합이 형성되지 않는 비공유결합 에피택시가 된다. 2차원 소재는 고온에서 안정하고, 유연성이 있기 때문에 LED 칩을 선택성장하게 되면 유연소자를 제작하기 쉽다(2.4.절).
구동회로에 LED를 집적하는 여러 가지 방법이 있다. 구동회로 위에 LED를 접합하는 방법, 또는 LED 위에 구동회로를 형성하는 방법이 있고, 특히 LED 위에 구동회로를 형성함에 있어 반도체 특성을 가지는 2차원 나노소재가 활발하게 연구되고 있으며, 유연성 확보를 위한 전극구조 또한 매우 중요한 이슈이다(2.5.절).
현재, 유연 및 폴더블 디스플레이로 OLED가 시장에 출하되어 있으며, 수요와 공급 모두 급속도로 확대되고 있다. LED는 유연 디스플레이로 제작하기 위해 많은 기술적 챌린지가 있고 해결해야 할 문제가 많다. 그러나 LED의 우수한 물리적 성질과 이를 필요로 하는 응용에서는 LED라는 화소 광원의 수요는 절대적이라고 할 수 있고, 이러한 장점을 유연 디스플레이에서도 활용할 수 있어야 하겠다. LED 디스플레이와 유연 디스플레이의 상용화를 위해서는 공정의 단순화, 수율, 단가 뿐만 아니라 디스플레이 스탠다드를 만족시킬 수 있는 성능 균일도 확보 및 유연 기판으로의 집적 기술이 중요하다. 이를 위해서는 마이크로 LED의 초소형화에 따른 효율 저하 이슈, LED 대량전사법의 전사 위치 정확도 향상 방법, 유연 디스플레이를 위한 LED/트랜지스터와 인터커넥트 구조에 대한 연구가 활발할 것으로 전망된다.
우리나라가 LCD와 OLED에서 독보적인 세계 1등을 차지했던 것은 각 디스플레이 플랫폼이 가지고 있는 문제점과 한계점을 뛰어넘기 위한 산업계와 학계의 노력이 있었기 때문이다. 그리고 LED 디스플레이에서도 전술한 기술적 난제들을 극복하기 위한 연구가 국내에서 매우 활발하게 진행되고 있다. LCD와 OLED에서 남들이 풀지 못했던 어려움을 극복하면서 초격차 기술을 확보해왔던 우리나라 디스플레이 산업이 LED 디스플레이와 LED 유연 디스플레이에서도 역시 세계 최고의 기술로 우뚝 서길 기대해본다.