1. 서론
금속 할라이드 페로브스카이트(metal halide perovskite, 이하 페로브스카이트) 소재는 높은 흡광도, 발광 효율과 우수한 색순도, 용액 공정을 활용한 낮은 생산 단가, 할라이드 이온 조절을 통한 발광 색상 조절의 용이성, 얕은 결함 에너지 레벨 등 여러 우수한 특성을 가지고 있어 태양전지, 발광 다이오드, 광감지센서, 뉴로모픽 소자, 레이저 다이오드 등 다양한 광전 소자를 위한 차세대 광 반도체 소재로서 각광받고 있다[1-10]. 또한, 최근에는 페로브스카이트 소재를 발광층으로 사용한 적색, 녹색, 청색 발광 다이오드 소자들이 상용화 가능한 수준으로 휘도, 수명, 전류 효율이 개선되고 있으며, 이로 인해 페로브스카이트는 차세대 초실감 전기발광 디스플레이를 위한 발광층 소재로 크게 주목받고 있다[8,11-12].
이러한 페로브스카이트 발광체를 차세대 초실감 디스플레이 프론트 패널에 적용하기 위해서는 페로브스카이트 층을 수백 나노미터에서 수십 마이크로미터 크기의 픽셀(pixel)로 만드는 패터닝 공정이 필수적이다. 페로브스카이트 소재의 패터닝 공정은 광원의 사용 여부에 따라 광학적 패터닝과 비광학적 패터닝으로 분류할 수 있으며, 이 중 광학적 패터닝 방법으로는 자외선 영역의 광원을 사용하는 포토리소그래피(photolithography) 공정이 대표적이다[13]. 하지만 포토리소그래피의 경우, 포토레지스트(photoresist)의 현상(development) 과정 중에 현상액(developer)에 의해 페로브스카이트 소재가 손상될 위험성이 존재하며, capillary force의 작용이나 포토레지스트의 부품(swelling) 현상으로 패터닝의 정확도가 낮아질 수 있다. 이를 해결하기 위해 최근에는 소재 자체에 광반응성을 부여하여 포토레지스트 없이도 패터닝을 가능하게 하는 직접 광학 리소그래피와 같은 간단한 공정들이 보고되고 있다[14-16]. 그러나 위와 같은 자외선을 사용하는 광학 패터닝 공정들은 수백 나노미터 수준 패턴 구현의 어려움, 자외선 광원의 높은 에너지로 인한 소재 손상 가능성, 서로 다른 소재의 연속적 패터닝 공정의 어려움 등의 한계점들이 여전히 존재한다[17]. 이러한 한계점을 극복하기 위해 광원을 사용하지 않고 수백 나노미터 크기의 패턴 구현이 가능한 템플릿 기반 프린팅 기술이 주목받고 있다.
따라서 본 리뷰에서는 차세대 초실감 디스플레이 상용화를 위해 페로브스카이트 소재에 적용할 수 있는 템플릿 기반 프린팅 기술들을 소개하고자 한다. 아래 챕터에서는 대표적인 템플릿 기반 프린팅 기술인 나노 임프린트 리소그래피(nano imprint lithography, NIL)과 나노 전사 프린팅(nano transfer printing, NTP)을 소개하고, 이러한 템플릿 기반 프린팅 기술들이 페로브스카이트 나노 패턴 제작에 어떻게 활용되었는지 간략하게 설명할 것이다. 그 후, 마지막으로 템플릿 기반 프린팅 기술의 향후 발전과 전망에 대하여 간략하게 논의하고자 한다.
2. 할라이드 페로브스카이트 소재의 템플릿 기반 프린팅 기술 종류와 활용
나노 임프린트 리소그래피는 제작하고자 하는 패턴의 실리콘 템플릿(Si template)으로부터 다양한 고분자 소재를 이용하여 몰드 스탬프(mold stamp)를 제작하고, 제작된 몰드 스탬프를 패터닝하고자 하는 박막에 올린 후 적당한 압력을 가해 패턴을 구현하는 공정이다(Fig. 1). 나노 임프린트 리소그래피는 몰드 스탬프를 이용해 빠르고 반복적으로 패터닝이 가능하기 때문에 공정 측면에서 경제적일 뿐만 아니라, 복잡한 미세 패턴 제조가 가능하고 패터닝 공정 중 광원을 사용하지 않기 때문에 발광 소재의 손상 위험이 적다는 장점을 가진다. 따라서 소재의 안정성이 유기 발광체(organic emitter)나 양자점(quantum dot)보다 낮은 페로브스카이트의 패터닝에 적합한 공정이며, 실제로 다양한 페로브스카이트 소재의 1차원, 2차원 패터닝에 이용되고 있다[17].
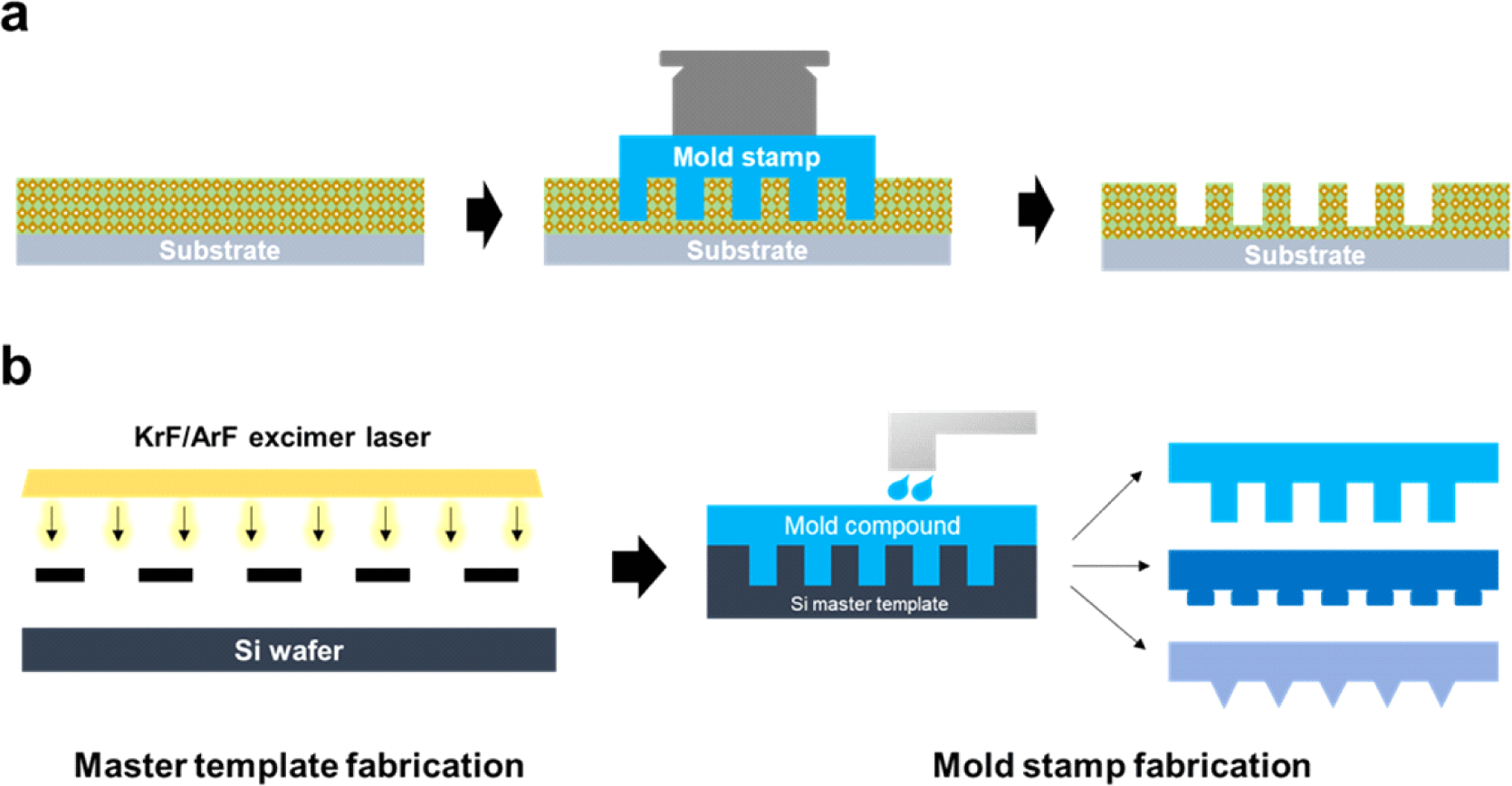
이러한 나노 임프린트 기술을 활용하여 균일하고 재현성이 높은 패턴을 구현하기 위해서는 템플릿으로부터 만들어지는 몰드 스탬프의 패턴 품질이 중요하다. 특히 몰드 스탬프의 소재 선택에 따라 형성되는 박막의 패턴 품질이 달라지는데, 이는 사용하는 몰드 스탬프 소재의 신축성, 친수성 및 페로브스카이트와의 계면 특성 등에 영향을 받는다. 일반적으로 임프린트 공정을 위한 몰드 스탬프로는 신축성이 좋은 폴리디메틸 실록산(Polydimethylsiloxane, PDMS)을 사용한다(Fig. 2(a))[18-20]. 하지만 PDMS는 소수성(hydrophobility)을 가지고 있기 때문에 상대적으로 친수성(hydrophilicity)이 높은 박막의 경우, 몰드 스탬프와 박막 사이의 반발 작용으로 인해 균일하고 높은 종횡비 (aspect ratio)의 고품질 패턴을 얻기 어렵기 때문에 상대적으로 단단하고 소수성이 덜한 NOA(Norland optical adhesive) 소재의 몰드 스탬프를 사용한 사례도 있다(Fig. 2(b))[21]. 또한, 패터닝된 실리콘 웨이퍼를 직접 몰드로 사용하여 균일한 1차원 및 2차원 패턴을 구현한 연구도 보고되었다(Fig. 2(c))[22].
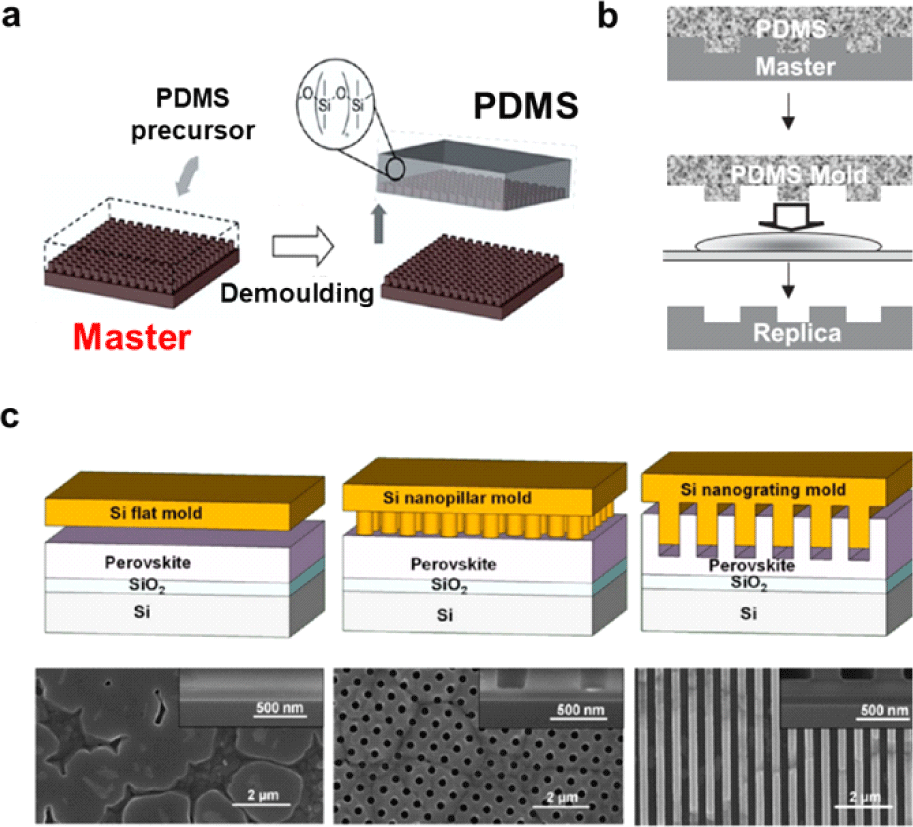
이외에도 나노 임프린트 리소그래피에서 파생된 공정 기술로 기판 위에 패터닝된 몰드를 올려놓고 패터닝할 소재의 전구체 용액을 흘려서 모세관 현상을 유도하여 몰드 내의 골(trench)에 용액이 채워지고, 열을 이용해 결정화를 진행하여 원하는 패턴을 구현하는 방법도 존재한다. 이러한 모세관 현상을 이용한 패터닝 방법은 M. Whitesides group에서 최초로 보고되었으며 (Fig. 3(a) 및 Fig. 3(b))[23], 이후 H. Lee group에서 수백 나노미터 수준의 패턴을 최초로 구현하였다(Fig. 3 (c)) [24]. 모세관 현상을 이용한 패턴의 최대 높이는 몰드 표면과 패턴을 형성할 박막의 전구체 용액의 계면 에너지, 몰드 소재, 몰드 패턴의 간격 등의 영향을 받으며, 식 (1)과 같이 나타낼 수 있다[25].

식 (1)에서 hmax는 패턴 최대 높이, γ는 몰드 스탬프 위에서의 용액의 표면 장력, θ는 몰드 스탬프/용액의 접촉각, ρ는 용액의 밀도, G는 중력 가속도, L은 몰드 패턴의 간격을 의미한다. 따라서 모세관 현상을 활용한 패터닝 공정 시 높은 종횡비의 패턴을 구현하기 위해서는 위에서 언급한 요소들을 고려해 패터닝을 진행해야 한다.
이러한 나노 임프린트 공정을 활용하여 수백 나노미터 및 마이크로미터 수준의 1차원 및 2차원 페로브스카이트 패턴을 구현한 여러 연구들이 보고되었다. 먼저 고전적인 임프린트 방법인 압력을 가하여 구현한 페로브스카이트 패턴의 경우, S. P. Lau group에서 DVD 뒷면을 활용하여 수백 나노미터 간격의 균일한 1차원 선형 페로브스카이트 패턴을 구현한 바 있으며, 이러한 패턴의 높은 편광 민감도(polarization sensitivity) 특성을 이용하여 편광을 감지하는 포토디텍터(photodetector) 소자를 구현하여 페로브스카이트 소재 기반 편광 감지 소자의 구현 가능성을 보였다(Fig. 4(a))[26]. 또한 J. Myoung group에서는 PDMS 몰드를 활용하여 직경 10 마이크로미터의 2차원 원형 CsPb (Br/I)3조성의 페로브스카이트 패턴을 구현하였으며, 이러한 패턴을 10 마이크로미터 해상도 픽셀의 마이크로 발광 다이오드(micro light-emitting diode, μ-LED)에 응용함으로써 페로브스카이트 발광체 기반 초실감 근안 디스플레이 소자 구현의 마일스톤을 제시하였다[27]. P. Heremans group에서는 제작한 페로브스카이트 박막 상부에 폴리머 레진 박막을 형성한 후, 임프린트 공정을 통해 200 나노미터 수준의 1차원 패턴 제작에 성공하였고, 이를 이용해 광학적 펌핑을 통한 반치폭(FWHM) 0.16 nm 수준의 페로브스카이트의 레이징 현상을 보고하였고, 페로브스카이트 소재를 기반으로 광학적 레이저 다이오드 소자 구현의 가능성을 보여주었다(Fig. 4(b))[28]. 마지막으로 E. C. Garnett group에서는 (CH3NH3)PbBr3 조성의 페로브스카이트 전구체 용액의 용매 종류가 페로브스카이트 결정화 과정에 영향을 미쳐 페로브스카이트 박막의 임프린트 공정에서 패턴의 균일도를 변화시킨다는 사실을 밝혀냈으며, 이를 기반으로 200 나노미터 수준의 고해상도 페로브스카이트 박막 패턴 제작에 성공하여, 페로브스카이트 구조체의 광학 소자로서의 활용 가능성을 제시하였다[29].
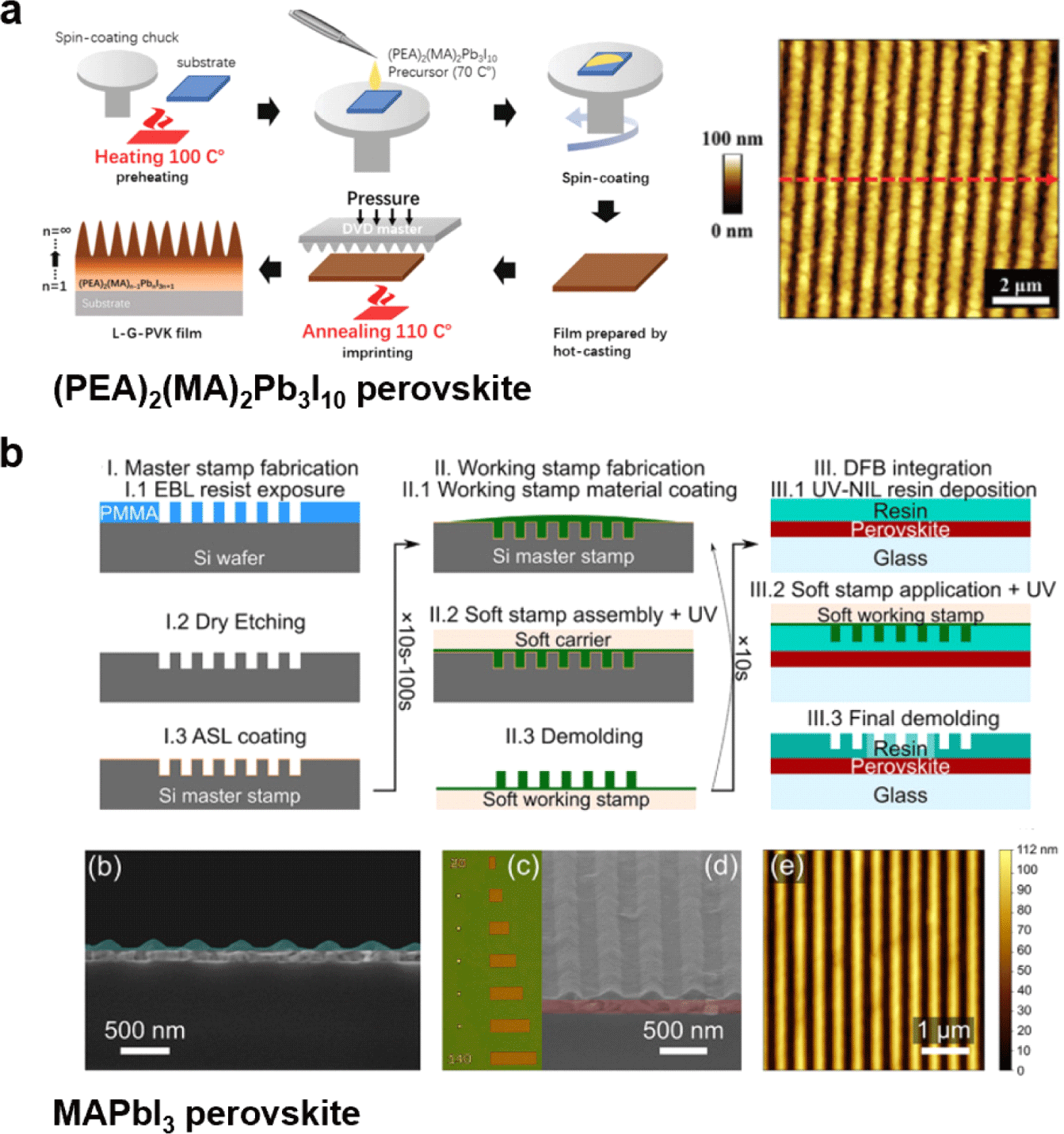
페로브스카이트는 용액 공정이 가능한 소재이므로, 앞서 언급한 모세관 현상을 이용한 임프린팅 공정이 가능하고 관련된 사례도 존재한다. J. E. Elshorf group에서는 PDMS 몰드를 이용하여 모세관 현상을 기반으로 한 임프린트 공정을 시도하여 수 마이크로미터 해상도를 가진 1차원 패턴을 구현하였으며, 기존의 압력을 가하는 방식으로 얻은 패턴과 종횡비와 패턴의 균일성을 비교하였고, 임프린팅 기술로 구현한 페로브스카이트 기반 구조체에서 1.8의 높은 종횡비를 달성하였다. 또한 형성된 페로브스카이트 패턴의 결정성과 광학적 특성 또한 구체적으로 분석하여 광학 소자에 적용 시 구조체의 광학적 특성을 극대화하기 위해서는 적절한 임프린트 공정이 필요하다는 점을 강조하였다 (Fig. 5(a))[30]. C. Park group에서는 페로브스카이트 전구체 용액을 SiO2 기판 위에 도포한 후, PDMS 몰드 스탬프를 붙여 모세관 현상을 이용하여 몰드 내의 골 내부에서 페로브스카이트를 결정화시켜 300∼400 나노미터 간격의 1차원 선형 패턴을 구현하였고, 이를 토대로 450∼800 nm 파장 범위의 가시광선을 감지하는 포토 디텍터 소자를 제작함으로서 페로브스카이트 소재 기반 발광 소자의 상용화의 가능성을 보여주었다 (Fig. 5(b))[31]. H. Fu group에서는 PDMS 몰드를 활용하되, 기존의 개방된 선형 패턴이 아닌 직사각형 모양의 홈(rectangular groove-templates) 패턴을 이용해 페로브스카이트 전구체 용액을 가둔 후, 모세관 현상을 이용해 끝에서부터 천천히 결정화시켜 길이 50 마이크로미터, 폭 460 나노미터 크기의 직사각형 나노와이어(nanowire) 형태를 가지는 페로브스카이트 패턴을 제작하였으며, 이를 이용하여 광학적 펌핑을 통한 페로브스카이트 레이징을 구현하였고, 4×107번의 많은 레이저 광원 조사 후에도 발광체의 광학적 특성이 열화없이 그대로 유지되어 페로브스카이트 기반 고수명 레이저 소자 구현의 가능성을 보여주었다(Fig. 5(c)) [32]. 더 나아가, 이 기술을 확장하여 PDMS 몰드에 2차원 원형 홈을 제작하여 같은 방식으로 2×2 마이크로미터 크기의 사각형 페로브스카이트 패턴을 구현하였으며, 이를 3 μJ cm−2의 낮은 에너지로 페로브스카이트 발광체의 레이징 현상을 관찰하였다. 또한 다양한 색상의 마이크로 어레이를 구현하여 페로브스카이트 기반 고해상도의 마이크로 LED 구현 및 초실감 근안 디스플레이의 가능성을 제시하였다(Fig. 5(d))[33].
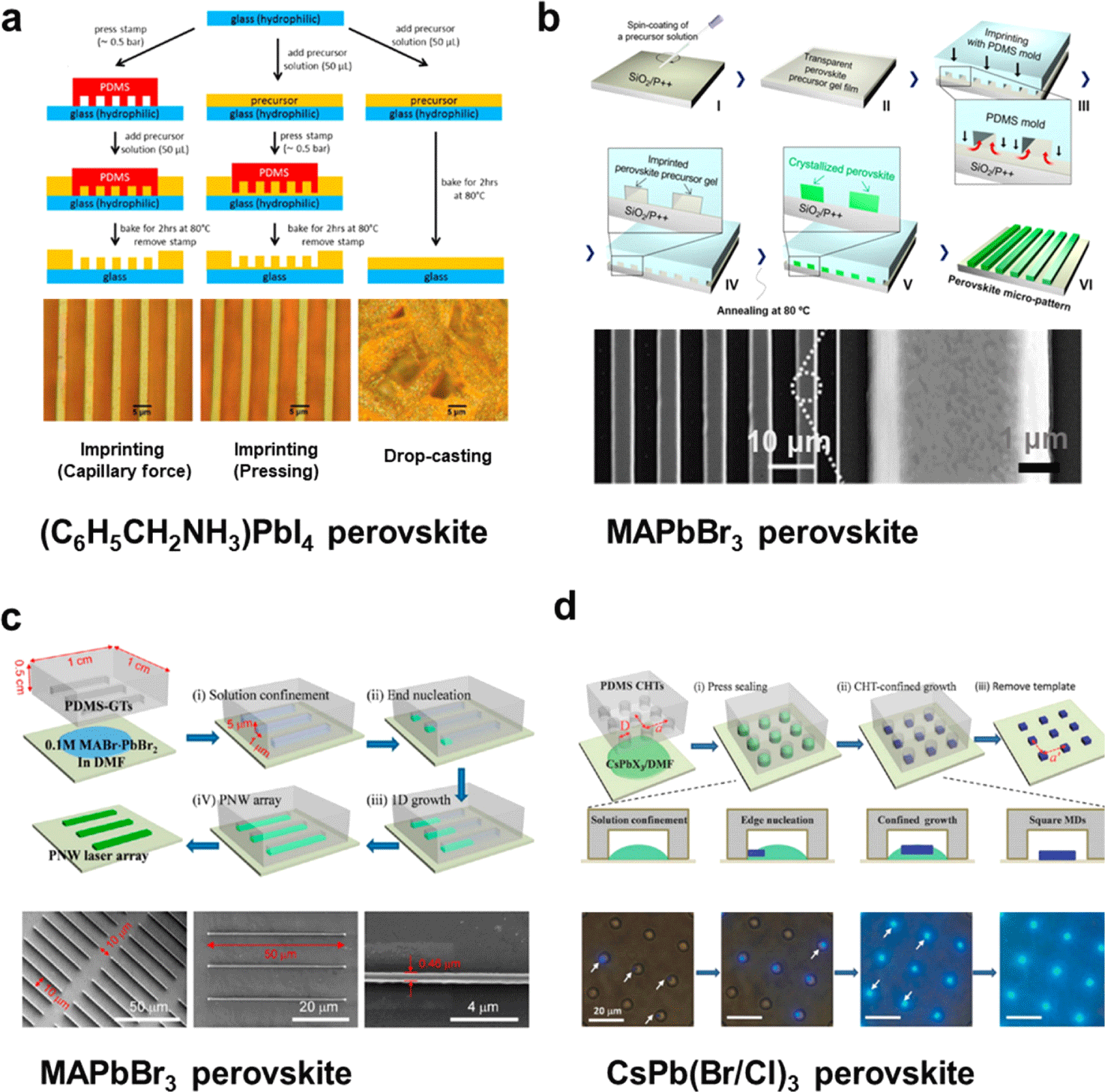
위의 사례들처럼 페로브스카이트 나노임프린트 공정은 단순히 템플릿을 활용한 마이크로미터 이하 수준의 반복적인 구조체 제작이 가능할 뿐만 아니라 다양한 발광 소자로의 적용이 가능한 범용성 높은 기술임을 알 수 있다. 하지만 이러한 발광소자의 성능 개선을 위해서는 소자의 목적에 부합하는 패턴 설계와 임프린팅 후 제작된 페로브스카이트 구조체의 균일성 확보를 하는 것이 중요하고, 더불어 광학적․전기적 특성 손실을 최소화하기 위한 다양한 전략의 연구가 필요하다.
템플릿 기반 나노 패터닝의 종류 중 하나인 나노 전사 프린팅은 제작하고자 하는 패턴의 실리콘 템플릿(Si template)으로부터 얻은 몰드 스탬프나 이미 패터닝이 된 구조체를 전사 스탬프를 활용하여 다른 기판으로 옮기는 인쇄 기술이다. 일반적으로 전사 스탬프의 경우 공정 과정에 있는 기판들과의 탈부착을 용이하게 하기 위해 PDMS 등의 엘라스토머(elastomer) 소재를 이용한다[34]. 나노 전사 프린팅 공정은 기존의 나노 임프린트 리소그래피 공정과는 달리 대부분의 기판을 활용할 수 있으며, 전사하고자 하는 구조체를 상온에서 높은 정확도로 프린팅을 할 수 있다는 장점이 있다. 또한 기존 용액 공정으로는 진행하기 어려운 각 구조체의 적층(stacking) 공정 시 소재의 손상을 최소화할 수 있으며, 마이크로미터 수준의 정밀한 위치 조절이 가능하여 디스플레이 상용화 기술에 필수적인 픽셀 어레이 구현이 가능하다[34]. 따라서 기존의 유기 발광체와 양자점 발광체 소재의 경우 이러한 전사 프린팅 기술을 활용한 고품질 나노 구조체 제작 기술이 많이 보고되어져 있다[35-38].
페로브스카이트 소재 또한 이러한 전사 프린팅 기술을 활용한 나노/마이크로미터 수준의 구조체 형성 사례가 많이 보고되어져 있다. 먼저 M. Choi group에서는 피킹(picking)할 기판(donor substrate) 상에 형성된 페로브스카이트 나노결정 박막을 PDMS 소재 스탬프를 통해 피킹(picking)하고 이를 원하는 모양으로 패터닝이 된 기판(intaglio trench)에 옮겨 패턴을 형성한 다음 다시 스탬프를 이용하여 기판(receiver substrate)의 원하는 지점에 전사를 하는 기술을 개발하였다. 이를 이용해 3 마이크로미터, 2,550 PPI 수준의 초고해상도 페로브스카이트 RGB 픽셀 어레이를 구현하였으며, 400 나노미터 수준의 선형 패턴 또한 전사가 가능함을 보고하였다. 또한 LED 소자로 제작하였을 때 15.3%의 높은 외부양자효율(EQE)를 보여주어 페로브스카이트 소재 기반 고효율, 고해상도 마이크로 LED 소자의 상용화의 가능성을 열어주었다(Fig. 6(a))[39]. Z. Xiao group에서는 PDMS 스탬프 상에 용액 공정을 통해 페로브스카이트 박막을 형성한 후, 이를 소자층 위에 전사하는 공정을 개발하여 페로브스카이트 발광 소자의 효율을 크게 개선시켰다. 더 나아가 동일 공정으로 적색발광 및 담청색 발광 페로브스카이트 발광소재를 1차원 구조체를 만들어 각각 원하는 지점에 전사하여 100 마이크로미터 해상도의 적색/담청색 1차원 선형 패턴을 색상의 겹침 없이 구현을 하였고, 적색, 담청색 발광을 혼합하여 200 마이크로미터 해상도의 백색 LED 소자를 제작하여, 전사프린팅 공정을 활용한 고해상도 백색 페로브스카이트 LED를 최초로 구현하였다(Fig. 6(b))[40]. 또한 C. Park group에서는 겔(gel) 형태의 페로브스카이트 전구체 박막을 패터닝된 PDMS 기반 몰드 스탬프로 피킹하여 전사할 기판(receiver substrate)에 옮긴 후, 열처리를 통해 페로브스카이트를 결정화시켜 20 마이크로미터 크기의 육각형 패턴을 구현하여 마이크로미터 수준의 픽셀을 갖는 고해상도 페로브스카이트 발광 소자 구현의 가능성을 보여주었다(Fig. 6(c))[31]. 마지막으로 Y. Lee group에서는 PDMS 기반 스탬프에 페로브스카이트 단결정을 올린 다음 이를 고온 박리 테이프(thermal release tape)를 활용하여 박리한 후 이를 패턴이 된 실리콘 템플릿을 활용하여 미세하게 조각을 내고 전사할 기판에 옮겨 10∼20 마이크로미터 지름의 균일한 2차원 원형 패턴을 구현하였고, 이를 LED 소자에 적용하여 상대적으로 소재 안정성이 높은 단결정 페로브스카이트 기반의 마이크로미터 해상도의 LED 소자를 최초로 구현함으로써 단결정 페로브스카이트 기반 마이크로 LED의 가능성을 보여주었다(Fig. 6(d))[41].
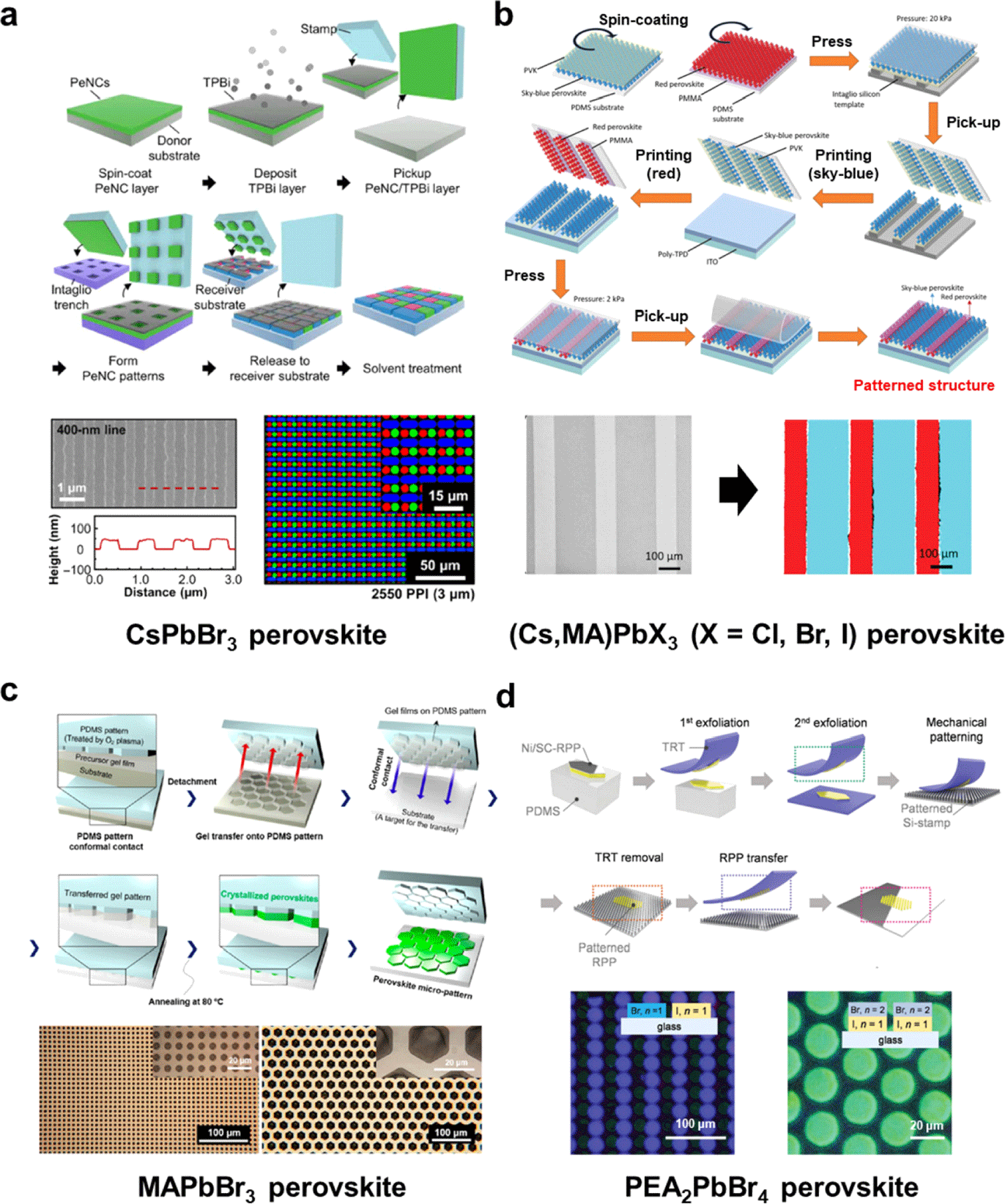
이처럼 페로브스카이트 전사프린팅 공정 또한 다양한 발광 소자로의 적용이 가능한 미세 패터닝 기술이라는 것을 알 수 있다. 하지만 본 기술을 활용한 발광소자의 성능 개선을 위해서는 소자의 목적에 맞는 패턴 모양의 설계, 전사수율(picking yield)의 개선, 그리고 전사한 페로브스카이트 구조체의 균일성 및 광학적․전기적 손실의 최소화 등이 필요하고 이를 해결하기 위하여 다방면적으로 고려해야 한다.
3. 결론 및 전망
본 리뷰에서는 차세대 발광 소재로 각광받고 있는 페로브스카이트 소재의 나노/마이크로 단위의 패턴 제작 시 사용될 수 있는 템플릿 기반 프린팅 기술인 나노임프린트 리소그래피와 나노 전사 프린팅 공정 기술을 소개하였다. 나노 임프린트 리소그래피의 경우 경제적으로 미세패턴을 형성할 수 있으며, 공정과정에서 발광소재의 손상 가능성이 낮다는 장점이 있다. 하지만, 형성되는 미세 패턴의 품질이 몰드 스탬프의 패턴 품질에 크게 의존하므로 스탬프 소재 선정 시 기계적 특성과 표면특성을 신중히 고려해야 한다는 한계점이 존재한다. 반면, 나노 전사 프린팅 기술은 상대적으로 기판 선택의 폭이 넓고 픽셀 어레이 구현이 용이하다는 장점을 가지지만, 공정 과정에서 발광 소재의 광학적·전기적·구조적 손상이 일어날 수 있다는 단점 또한 존재한다. 향후 차세대 증강현실/가상현실 디스플레이의 상용화를 위해서는 위와 같은 한계점들을 극복하여 발광체의 광학적·전기적·구조적 특성 손상을 최소화하면서 수 마이크로미터 이하 크기의 초고해상도 픽셀을 구현할 수 있는 효율적인 패터닝 기술의 개발이 중요하다. 이를 위해서는 패턴하고자 하는 소재의 고유 특성과 응용처에서 필요로 하는 특성들을 동시에 고려하여 패터닝 공정을 설계할 필요가 있다. 기존 공정들의 한계를 극복할 수 있는 비파괴적 패터닝 공정 기술의 지속적인 연구 개발을 통해 차세대 초실감 디스플레이의 구현이 앞당겨지기를 기대한다.