1. 서론
현대 사회에서는 에너지의 생산과 공급, 그리고 소비 과정에서 막대한 양의 폐열이 발생하여 에너지 효율이 감소하고, 사회적 비용은 증가하고 있다. 이와 같은 폐열을 활용하기 위한 후보 기술로, 열을 직접 전기로 변환하는 열전(thermoelectric, TE) 에너지 하베스팅 기술이 주목받고 있다[1,2]. p형과 n형의 반도체 특성을 지닌 열전 소재는 소재 양단의 온도 차를 통해 전위차를 형성하여 제벡(Seebeck) 전압을 발생한다. 열전 기술은 고체 상태의 직접적인 에너지 변환이면서 동시에 부산물 및 진동이 발생하지 않아, 그린 에너지 하베스팅의 중요한 축으로 각광받고 있다[3,4].
에너지 회수 연구는 통상 그 변환 효율의 향상이 주된 목표라 할 수 있으며, 열전 기술 역시 지난 수십년간 소재의 열전 성능 지수(figure of merit, zT)를 증진하는 방향의 연구가 주를 이루어 왔다[5,6]. 하지만 최근에는 폐열이 발생하는 열원이 다양해지고 있으며, 열 회수의 대상이 점차 평면이 아닌 복잡한 표면으로 확장되면서, 열전 소재/소자에 유연성 및 기계적 순응성을 부여하려는 연구가 활발해지고 있다[7-10]. 더불어 체온 하베스팅 및 생체 신호 센서와 같은 웨어러블 열전 소자의 수요가 성장하면서[11-18], 수치 변화를 동반하는 인장 및 수축이 발생하는 열원에도 열전 기술을 접목하려는 노력이 새로운 주목을 받고 있다.
이에 통상적으로 변형성이 우수하지 않은 열전 소재와 소자에 유연성을 초월한 신축성을 부여해 변형에 대한 내구성과 열전 성능의 안정성을 동시에 확보하려는 연구가 점차 확대되고 있다. 열전 소재의 부족한 신축성은 열전 발전기(thermoelectric generator, TEG)의 소자 차원의 구조 연성화를 통해 보완될 수 있다[19-21]. 기계적 변형성이 향상된 열전 소자는 외부 응력과 변형에 의한 손상 및 열전 성능 저하를 일부 방지하며, 열원의 형태 변형에 유연하게 대응하며 순응할 수 있다. 하지만 열전 소재 자체의 신축성 부재에서 기인한 변형성의 한계가 존재하며, 제작 공정 및 디자인 자유도가 상대적으로 부족한 실정이다[22-24]. 이에 최근 소자가 아닌 열전 소재 자체에 내재적 신축성을 부여하려는 연구들이 보고되고 있다[25-38]. 신축성이 대폭 향상된 열전 소재는 소자 구조 디자인의 폭넓은 기회를 제공할 뿐만 아니라, 극한 환경에서의 열전 기술의 활용성과 안정성을 보장해 지속 가능한 열 회수를 가능하게 할 수 있다.
본 리뷰 논문에서는 다양한 복합화 및 신소재 합성을 통해 열전 소재의 내재적 신축성을 달성하는 최근 연구 결과들을 조명하고자 한다. 구체적으로는 열전 성능을 지닌 전도성 고분자로 대표되는 유기 열전 소재의 신축성 향상, 인장성 무기 열전 소재의 합성, 그리고 신소재의 개발을 통해 신축성 열전 소재를 확보하는 대표 전략들에 집중한다. 더불어 각 전략들의 기계적 변형성 향상의 정도와 더불어 열전 소재 본연의 성능 지수 변화 및 변형에 대한 성능 안정성들을 평가한다. 마지막으로 개발된 각 고유 신축성 열전 소재의 소자화 가능성을 논의하고, 어플리케이션 사례들을 소개하며 미래 활용 전망에 대해 고찰하고자 한다.
2. 신축성 유기 열전 소재
소프트 매트릭스에 유기 열전 소재를 블렌딩한 형태의 복합 소재는 고유 신축성을 지닌 모재의 변형성을 활용할 수 있다는 특징이 있다. 주로 연신성과 수축성이 모두 우수한 탄성중합체에 열전 특성을 지닌 전도성 고분자를 분산하여 열전 성능과 기계적 변형성을 동시에 달성하는 복합재를 형성한다.
스웨덴의 Xavier Crispin 교수 연구진은 PEDOT: PSS(poly(3,4-ethylenedioxythiophene) : poly-(styrenesulfonate)) 및 이온성 액체를 수성 폴리우레탄(waterborne polyurethane, WPU)에 첨가한 분산액을 진공 건조한 고신축성 삼상 복합 열전 소재를 보고하였다(Fig. 1(a))[25]. 열ㆍ전기 전달 경로를 형성하는 PEDOT:PS의 비중이 상승함에 따라, 전기전도도는 지속적으로 증가하였지만 제백 계수는 감소하는 상충 관계를 보였다(Fig. 1(b)). 동시에 소재의 영률 및 파단 변형률을 평가하여 전도성 고분자와 탄성중합체의 최적점을 결정하였다(Fig. 1(c)). 특히 이온성 액체는 전소성 고분자와 탄성중합체 상을 가소화하여 영률(<7 MPa)을 대폭 감소하고 600%를 상회하는 최대 연신을 가능케하였다. 개발 소재의 축 방향 인장 시 변형에 따른 열전 특성의 변화를 평가하였고, 또한 해당 소재와 합급 나노와이어로 구성된 10-leg TEG를 제작하여 신축성 열전 소자 구현의 가능성을 증명했다.
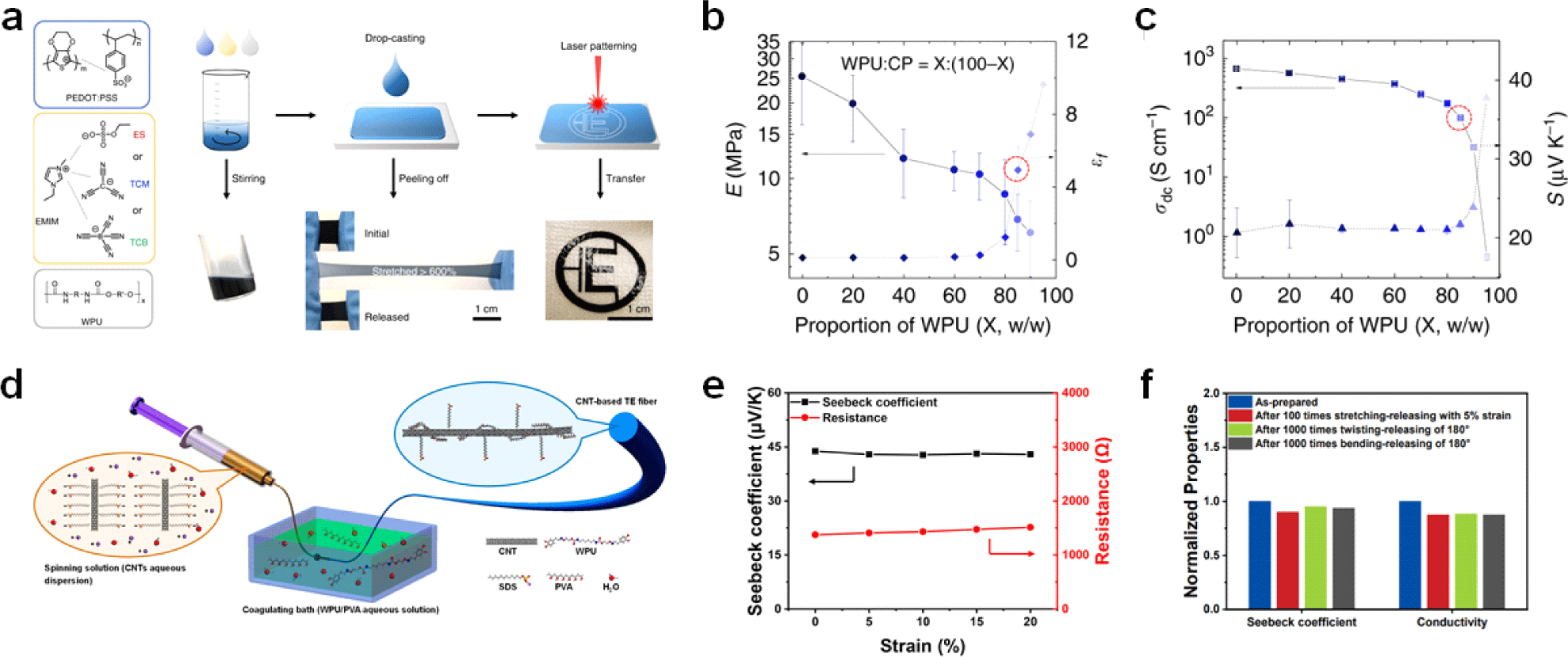
Fig. 1(d)는 습식 방사 공정을 활용해 열전 소재와 WPU를 복합화 한 열전 섬유의 예시이다[26]. WPU 및 PVA(poly(vinyl alcohol))를 포함한 응고 용액에 수분산 된 탄소나노튜브(carbon nanotube, CNT)를 시린지를 통해 직접 토출하여, 섬유 형태의 신축성 열전 소재를 제작할 수 있다. CNT에 WPU-PVA 고분자 사슬이 침투한 해당 열전 섬유의 최대 연신율은 27%에 그쳤고, 절연성 고분자의 첨가로 인하여 열전 성능 증진을 기대하기 어렵다(Fig. 1(e)). 하지만 WPU에 의해 CNT 네트워크의 변형 안정성이 향상되어 신축, 굽힙, 비틀기 등 다양한 형태의 기계적 변형을 1,000회 가량 인가 후에도 전기 전도도 및 제백 계수의 저하가 거의 없는 우수한 열전 성능의 반복 내구성을 입증하였다(Fig. 1(f)). 최종적으로는 섬유 형태에서 기인한 웨어러블 TEG를 제작하여 나노와트 수준의 체열 회수 능력을 보고하였다.
열전 필러를 소프트 소재 내부에 블렌딩하는 전략은 신축성 열전 소재를 제작하는 방법 중 가장 직관적이며 공정이 비교적 단순하다는 장점이 있다. 하지만 부피 분율이 절대적인 모재 역할을 하는 탄성중합체는 대부분 전기적 절연성을 지녀, 복합재 전체의 열전 성능은 필러의 고유 열전 특성에 미치지 못하는 경우가 빈번하다. 이를 극복하기 위해 매트릭스 내 열전 소재 분포의 최적화 및 기계적 변형에 따른 열적ㆍ전기적 네트워크의 안정성을 향상하는 연구가 필요하다.
가소화(plasticization)는 고분자에 가소제라는 첨가제를 넣어 유연성과 가공성을 향상하는 과정을 말한다. 가소제는 고분자 사슬 사이에 들어가 분자 간의 인력 및 분자 간의 반데르발스 힘을 약화시키고, 고분자 사슬의 얽힘을 방지하는 등 고분자 사슬 사이의 상호작용을 완화시켜 고분자의 기계적 특성이 유연해지도록 만들어준다. 대표적으로 가소제는 고분자 가소제(예: polyethylene glycol, glycerol, polyvinyl alcohol 등)와 이온성 액체(예: 1-ethyl-3-methylimidazolium dicyanamide, 1-ethyl-3-methylimidazolium chloride 등) 로 분류할 수 있다.
UNIST의 최경진 교수 연구진은 열전 소재인 PEDOT:PSS박막의 용매 처리 및 신축성 기판 사용이 열전 특성에 미치는 영향을 조사하였다[27]. 다양한 용매 EG(ethylene glycol), DMSO(dimethyl sulfoxide), MeOH(methanol), PEG(polyethylene glycol), H2SO4 (sulfuric acid)를 각각 PEDOT:PSS에 첨가한 후 PDMS (polydimethylsiloxane) 기판에 스핀 코팅 하여 복합 열전 박막의 전기적, 기계적 특성을 조절할 수 있었다(Fig. 2(a)). 특히, 고분자 가소제인 PEG를 사용하면 PEDOT:PSS 사슬의 유연성이 증가하며, 응력 집중 구간에서 박막의 균열 발생을 지연시켜주는 역할을 하게 되고 그 결과 55%의 높은 신축성을 달성하였다. 가소화로 인한 PEDOT 박막 특성 변화(PEDOT도메인 구조 변화)로 인해 인장 변형에 따라 전기 전도도는 감소하지만 제벡 계수는 증가하는 경향을 보였다(Fig. 2(b)). 또한 30% 사전 변형된 PDMS 기판 사용을 통해 PEDOT 박막의 신축성을 65%까지 더욱 향상시킬 수 있음을 보고했다.
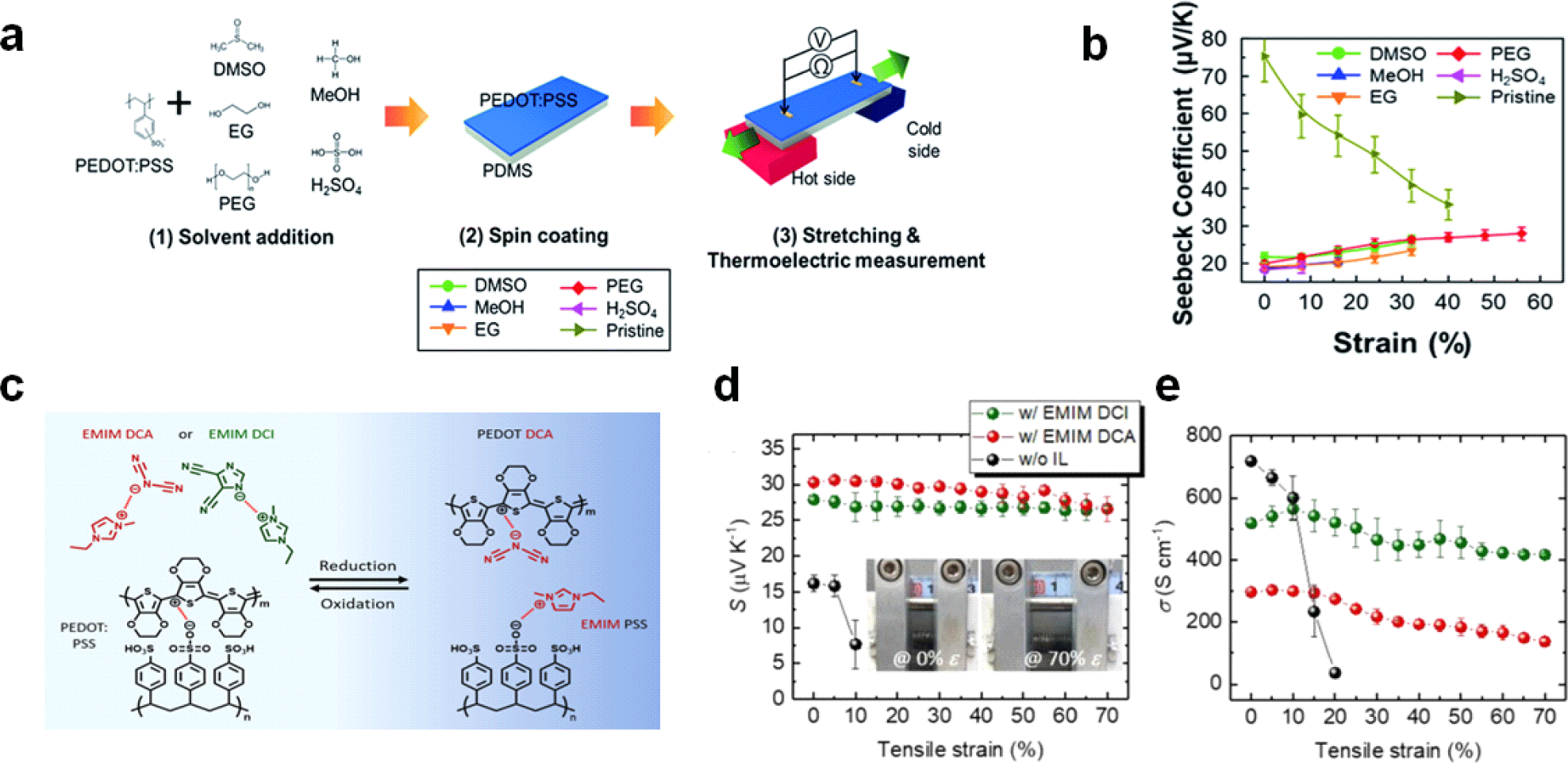
KAUST의 Derya Baran 교수 연구진은 PEDOT:PSS와 이온성 액체(ionic liquid, IL)인 EMIM:DCA(1-ethyl-3-methylimidazolium dicyanamide) 및 EMIM: DCI(1-ethyl-3-methylimidazolium 4,5-dicyanoimidazolate)를 혼합한 복합체를 이용하여 고신축성 및 공기 안정성을 가진 유기 열전 소재를 개발하였다(Fig. 2(c))[28]. 이온성 액체는 PEDOT:PSS 매트릭스 내부에서 결정성 섬유질 구조의 형성을 촉진하고, 소프트 도메인으로서 이를 임베딩하여 열전 성능과 70%의 인장을 견딜 수 있는 기계적 변형성을 동시에 향상했다. PEDOT:PSS/IL 필름에서 이온성 액체는 절연성 PSS 억제 및 PEDOT 도메인 재배열의 역할을 하여 더 나은 퍼콜레이션 네트워크를 형성할 수 있게 한다. 또한, 양이온(PEDOT⁺)과 음이온(DCA⁻ 또는 DCI⁻)이 상호작용을 하여 PEDOT 도핑 수준을 조절하고, 이에 따라 제벡 계수 및 전기 전도도가 향상되었음을 보고하였다(각각 최대 35 μV/K @400 K, 538 S/cm @300 K)(Fig. 2(d) 및 Fig. 2(e)). 또한, 최대 30%의 인장 변형을 60회 인가하는 사이클 평가 후에도 필름은 초기 역률 값의 약 73%를 유지하여 기계적 응력 하에서의 향상된 탄성과 내구성을 보였다.
유기 열전 소재에 전기 전도 네트워크를 조절할 수 있는 적절한 가소제를 선택 및 도입하면 기계적 신축성을 향상하거나 제벡 계수, 전기 전도 동시 향상으로 인한 열전 성능 증진 등의 이점을 얻을 수 있다. 가소화는 인장 강도와 같은 기계적 특성의 트레이드오프를 초래하여 응용분야의 제한이 생길 수 있는 한계점이 존재한다. 또한, 신축성과 열전 성능 향상의 균형을 맞추기 위해 가소제의 종류 및 농도를 최적화하는 방안을 생각해야 한다.
계면활성제는 양친매성 분자로, 유기열전 소재에 첨가될 경우 주로 표면과 계면에 흡착하여 소재의 표면 특성을 변화시키고 표면 장력을 감소시킨다. 이러한 변화는 마이셀 형성, 계면 윤활 효과, 미세 구조 조정, 상분리 제어 등 다양한 현상을 유도하며, 이로 인해 유기 열전 소재의 기계적 및 전기적 성능이 향상된다. 특히, 계면활성제는 신축성을 증대시키는 데 중요한 역할을 하고, 이는 계면 조정과 구조 변화를 통해 소재 내부의 응력 분포를 고르게 하고, 퍼콜레이션 네트워크를 개선하여 전도성 및 변형성을 함께 향상시킨다.
KAUST의 Derya Baran 교수 연구진은 대표적 유기 열전 소재인 PEDOT:PSS, DMSO, 그리고 계면활성제 Triton X-100을 혼합하여 자가 치유력 및 신축성이 있는 3성분계 복합 열전 소재를 개발하였다[29]. 매트릭스의 역할을 하는 계면활성제의 친수성 PEO (polyethylene oxide)기는 PEDOT:PSS의 친수성 파트와 결합하여 도메인의 재배열을 통해 인장성을 부여할 수 있다. 복합 열전 소재는 35%까지의 인장 변형에 견딜 수 있는 신축성을 보였고(Fig. 3(a)), 손상 후에도 빠른 시간 내에 본래 전기적 특성을 대부분 회복하는 자가 치유 능력을 보였다(Fig. 3(b)). 또한 DMSO는 전기전도도를 향상하고 계면활성제는 열전도도를 감소하여 해당 소재의 최종 열전 성능 지수(zT)가 2배 이상 증가했다. 최종적으로 3D 프린팅 기술로 복합재를 인쇄한 열전 발전기를 제작하여, 반복적인 절단에도 초기 출력의 85% 이상을 유지하는 치유 능력과 인체 온도를 이용한 유연한 TEG의 실용성도 시연하였다.
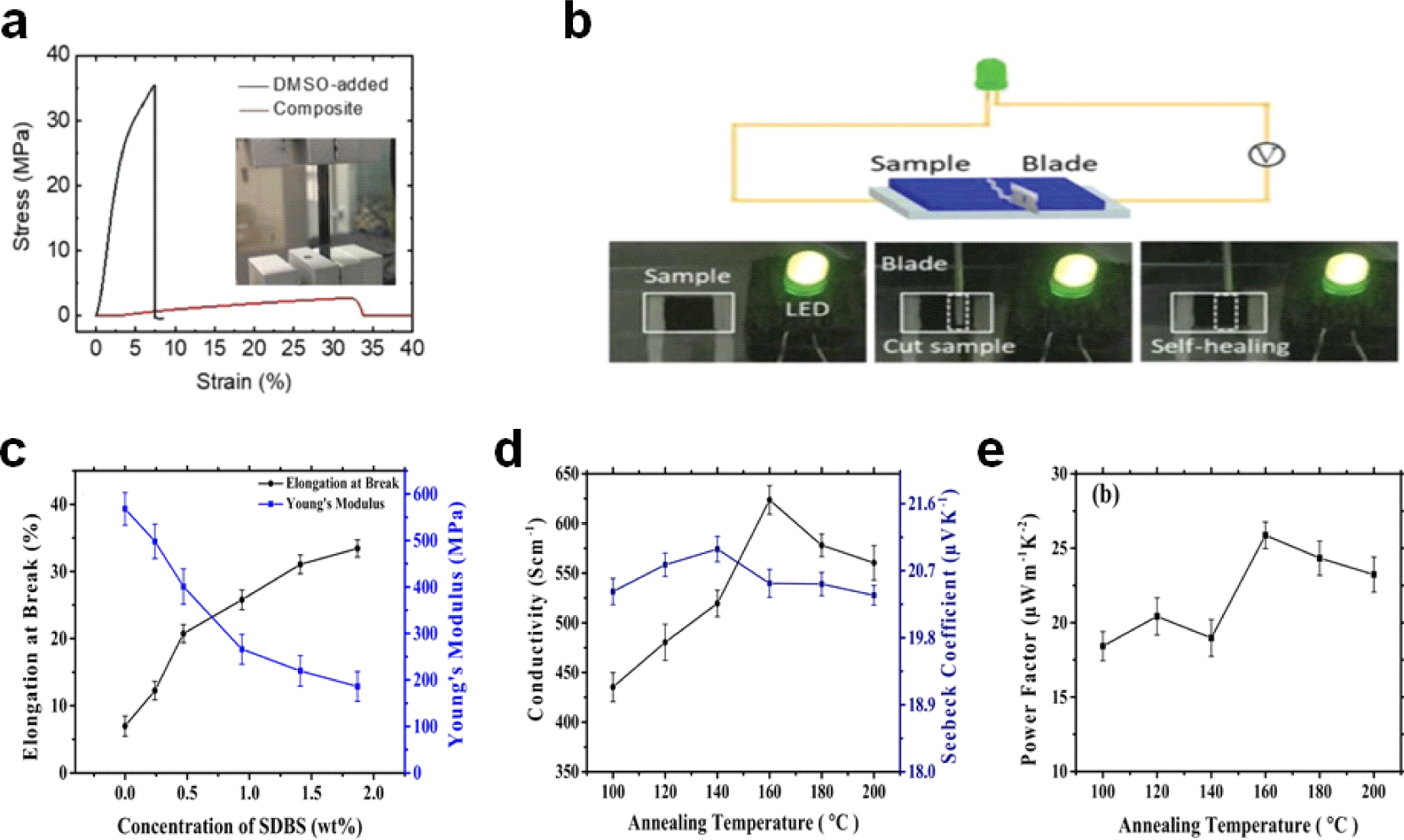
Nagoya Institute of Technology의 Naoki Kishi 교수 연구진은 다양한 어닐링 온도를 가정하여 소듐 도데실벤젠 설포네이트(sodium dodecylbenzene sulfonate, SDBS) 계면활성제로 개질된 자립형 PEDOT:PSS 필름의 신축성 및 열전 성능 향상을 연구했다[30]. 음이온성 계면활성제인 SDBS로 음이온 PSS−를 대체하여 쿨롱 인력을 감소시켜 PEDOT 사슬 자유도가 증가하고, 이에 따라 신축성이 향상되어 최대 34% 파단 연신율(1.87 wt% SDBS 조건 하)을 기록했다(Fig. 3(c)). 어닐링 온도에 따라서 PEDOT:PSS/SDBS 필름의 열전 성능이 달라졌으며, 최대 623.68 S/cm 전기 전도도, 25.87 μW/m·K2 파워 팩터를 기록했다(160℃ 어닐링 조건 하)(Fig. 3(d) 및 Fig. 3(e)). 제벡 계수는 어닐링 온도에 거의 영향을 받지 않았고, 그 결과 계산된 열전 성능 지수(zT)는 최대 0.05 값으로 측정되었다. 또한, PEDOT:PSS 용액에 SDBS, DMSO, EG를 섞어서 다양한 기판 위에서 접촉각 측정을 했고, PEDOT: PSS/SDBS 용액이 가장 낮은 접촉각을 가져 좋은 습윤성을 보였다.
유기 열전 소재에 계면활성제 기반 구조 제어를 적용하면, 소재 신축성 향상 및 일부 열전 성능 증가의 이점을 얻을 수 있다. 하지만, 계면활성제의 함량이 특정 임계점을 넘어가면 절연성을 가진 계면활성제 분자들이 전도성 경로를 차단할 수 있다. 그렇기에 계면활성제 사용에 대한 최적점이 존재하고, 전기 전도도와 열전 성능 간의 최적 균형을 찾는 것이 중요한 사안이다. 또한, 계면활성제 기반 구조 제어를 통해 얻은 소재의 신축성이 높은 값을 가지지 못하였고, 이를 향상시킬 방안을 모색해야 한다.
기존의 제벡 효과 기반 열전 소재와 달리, 이온성 열전 소재는 이온 전도체 내부의 온도 구배에 의해 양/음이온이 서로 다른 정도로 확산하여(Soret 효과) 그 불균형에서 전위차를 형성한다. 이온 전도체 내의 다양한 종류의 양/음이온들은 이온의 크기, 질량, 전하, 전기 음성도 등에 따라서 다른 이동도를 가질 수 있다. 따라서, 한 이온의 이동도를 극대화하고 반대 전하 이온의 이동도를 제한하여 전하의 불균형과 전위차를 극대화할 수 있다. 또한, 이온성 열전 소재는 대부분 유연한 고분자 매트릭스 또는 젤 기반 물질로 구성되어 있고, 양/음이온의 결합을 통해 네트워크의 상호작용을 조절할 수 있어 고유 신축성을 가질 수 있게 된다. 주로 사용되는 이온성 열전 소재는 이오노겔, 이온성 고분자, 이온성 복합체 등이 있다.
UNIST의 장성연 교수 연구진은 폴리아닐린(polyaniline, PANI), 비공액 음이온 고분자(poly(2-acrylamido-2-methyl-1-propanesulfonic acid), PAAMPSA), 그리고 피트산(pitric acid, PA)을 조합하여 자가 치유가 가능하고 본질적으로 신축성이 있는 3성분계 열전 하이브리드 소재를 개발하였다[31]. 하이브리드 소재는 구성 요소 간의 동적 수소결합, 양전하를 띤 PANI의 아민기와 음전하를 띤 PAAMPSA의 황산기 사이의 정전기적 상호작용으로 인해(Fig. 4(a)) 연성 네트워크의 신축성이 약 750%까지 향상되었다. 특히, 50% 인장 변형률에서도 열전 성능이 유지되며, 30회의 자가 치유 과정을 거친 후에도 성능을 유지하는 것으로 확인되었다. 해당 소재에서는 Soret 효과의 이동성 이온인 피트산의 양성자가 PAAMPSA의 설폰산 그룹 사이를 호핑하며 이온 전도가 진행된다. 최대 이온 열전 성능 지수(zTi)는 1.04(RT=90%)로, 상대 습도가 높을수록 높은 열전 성능을 보였다(Fig. 4(b)). 연구진은 개발한 열전 하이브리드 소재를 사용하여 열전 발전기(ionic thermoelectric generator, ITEG) 장치를 제작하였으며, 이 장치는 기계적 스트레스와 절단에도 불구하고 초기 성능을 지속적으로 유지함을 시연했다.
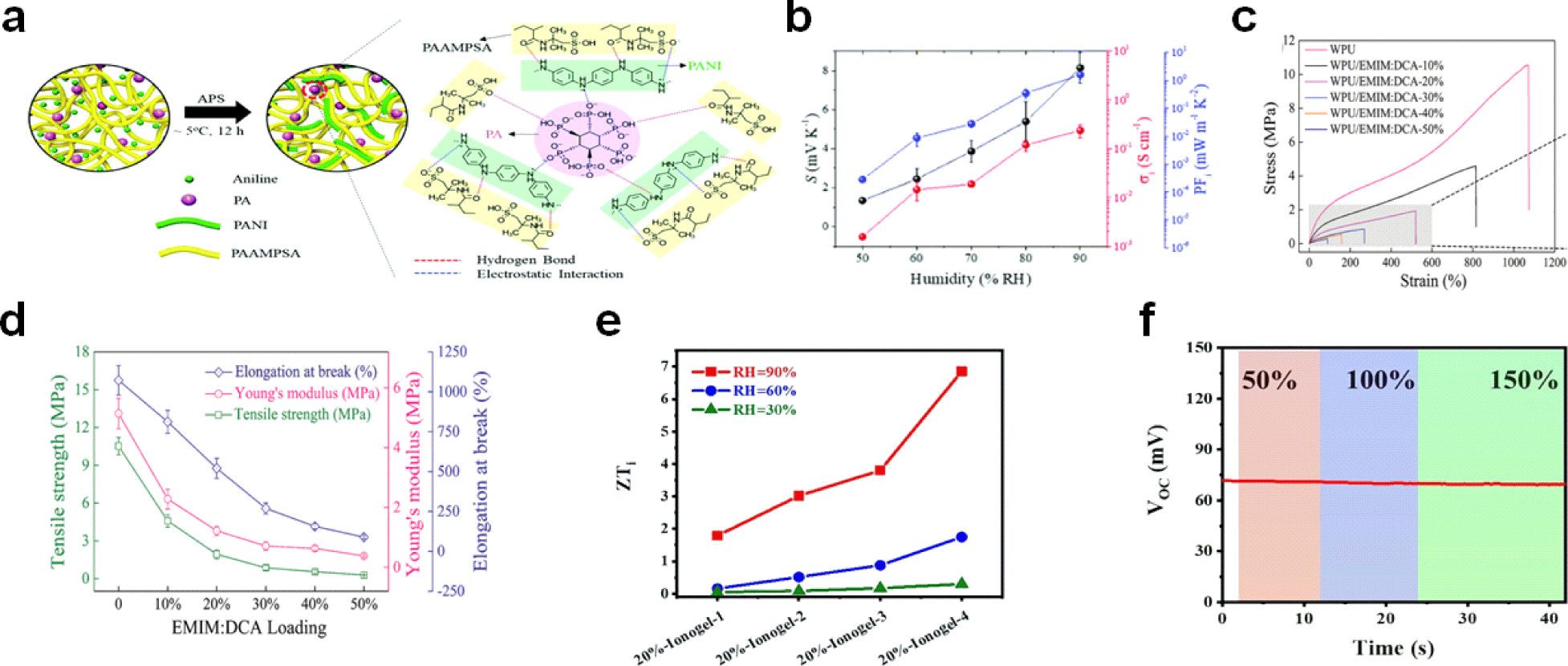
싱가포르 국립대학교의 Jianyong Ouyang 교수 연구진은 탄성중합체인 WPU와 이온성 액체인 EMIM:DC를 조합하여 신축성과 투명성을 가진 이오노겔을 보고하였다[32]. 해당 이오노겔에서 양이온 EMIM+은 WPU에 의해 이동이 제한되고, 이에 따라 Soret 효과의 이동성 이온은 음이온 DCA−이다. 90% 상대습도 조건에서 34.5 mV/K의 높은 이온 제벡 계수, 8.4 mS/cm의 높은 이온 전도도, 0.23 W/m·K의 낮은 열전도도를 나타냈고, 이온성 열전 성능 지수(zTi)는 1.3± 0.2의 값을 보였다. 하지만 이오노겔 내 EMIM:DCA의 함량이 증가함에 따라 점도 증가 및 WPU 고분자 네트워크의 변화로 인해 인장 강도와 영률이 낮아지고 신축성 또한 떨어져 최적 함량을 찾는 일이 필요하다(Fig. 4(c) 및 Fig. 4(d)). 소재를 100%까지 인장 시 이온 제백 계수와 이온 전도도가 크게 변하지 않았으며, 반복적인(최대 100회) 100% 인장률의 신축에도 성능이 유지되었다. 연구진은 이 이오노겔을 이용하여 이온성 열전 커패시터(ionic thermoelectric capacitor, ITEC)를 제작하여 열을 전기로 변환 및 저장하는 응용 가능성을 시연하였다.
중국의 Hebei 대학 Hongzan Song 교수 연구진은 아크릴산(acrylic acid, AA)과 헥사플루오로부틸 아크릴레이트(hexafluorobutyl acrylate, HFBA), 화학 가교제로 N, N-메틸렌 비사크릴아미드(N, N'-methylenebisacrylamide, MBA) 및 이온성 액체로 EMIM:DCA를 사용하여 신축성과 투명성을 가진 이오노겔을 만들었다[33]. AA의 카르복실기 및 MBA의 가교 효과로 인해 양이온 EMIM+ 이동도가 억제되기 때문에, Soret 효과의 주 이온은 음이온 DCA−이다. 해당 소재는 90% 상대습도 조건에서 28.43 mV/K의 이온 제벡 계수, 35.3 mS/cm의 이온 전도도, 2.85 mW/m·K2의 파워 팩터를 나타냈고, 이온 열전 성능 지수(zTi)는 최대 6.9의 값을 보였다(Fig. 4(e)). 이오노겔은 AA와 HFBA 조합의 유연한 폴리머 매트릭스 및 MBA 가교제의 역할로 인해 최대 250%의 신축성을 보였고, 또한 50∼150%의 인장 변형 구간에서도 비슷한 열전 성능을 유지했다(Fig. 4(f)). 연구진은 이 이오노겔을 이용하여 호흡 감지를 위한 열전 센싱 마스크를 제작해 4가지 보편적인 행동 하에 날숨 및 외부환경의 온도구배를 이용하여 호흡을 측정하는 시연도 진행했다.
이온성 열전 소재는 높은 열전 성능과 고유 신축성을 가지고 있어 주목을 받고 있는 열전 소재이다. 그러나, 기존의 제벡 효과와 달리 Soret 효과는 전자가 아닌 이온의 확산에 의존하므로 반응 속도가 느리고 즉각적 에너지 변환이 아닌 슈퍼커패시터와 같은 전기화학적 에너지 저장에 더 적합하다. 또한, 온도 구배에 의해 발생하는 이온 확산도의 차이를 극대화할 수 있는 외부 환경 조건이 잘 갖춰져야 한다는 제한이 있다. 예를 들어, 높은 상대 습도 조건에서 뛰어난 이온 열전 성능을 가지지만, 습도의 변화에 민감하여 성능의 불안정성 및 응용 분야의 제한 등을 초래할 수 있는 문제가 있다.
3. 연성 무기 열전 소재
무기 열전 소재는 일반적으로 유기 열전 소재에 비해 우수한 열전 성능을 가지지만, 취성이 있어 외력에 의한 변형에 취약하다는 결점을 가지고 있다. 이러한 한계를 극복하기 위해 S, Te 등의 원소를 도핑하거나 합금하여 화학적 구조를 제어함으로써 고유 연성을 가진 신축성 무기 소재를 합성하는 연구가 진행되고 있다.
대표적인 무기 열전 소재 중 하나인 α-Ag2S는 비대칭성으로 인한 슬립(slip)을 용이하게 하는 단사정계 구조와 Ag-Ag 금속 결합의 존재로 인해 연성 변형에 유리하다는 특징을 가지고 있다. 손재성 교수 연구진은 자체적인 연성을 가지고 있는 Ag2S 파우더를 에틸렌다이아민(ethylenediamine)과 에테인다이티올(ethanedithiol) 혼합 용매에 융해하여 스핀 코팅을 통해 신축성 박막을 형성하였다(Fig. 5(a))[34]. 이를 신축성 고무 기판에 전사해 축 방향의 인장을 시험한 결과, 최대 14.9%의 인장 변형률이 측정되었다. 또한 기판이 사전 변형되었을 경우 Ag2S의 인장 변형률은 52%까지 향상되었으며(Fig. 5(b)), 동시에 전기적인 특성까지 유지할 수 있다는 것이 확인되었다. 더불어 1,000회의 굽힘 사이클 후에도 성능을 유지하여 내구성까지 입증하였다(Fig. 5(c)).
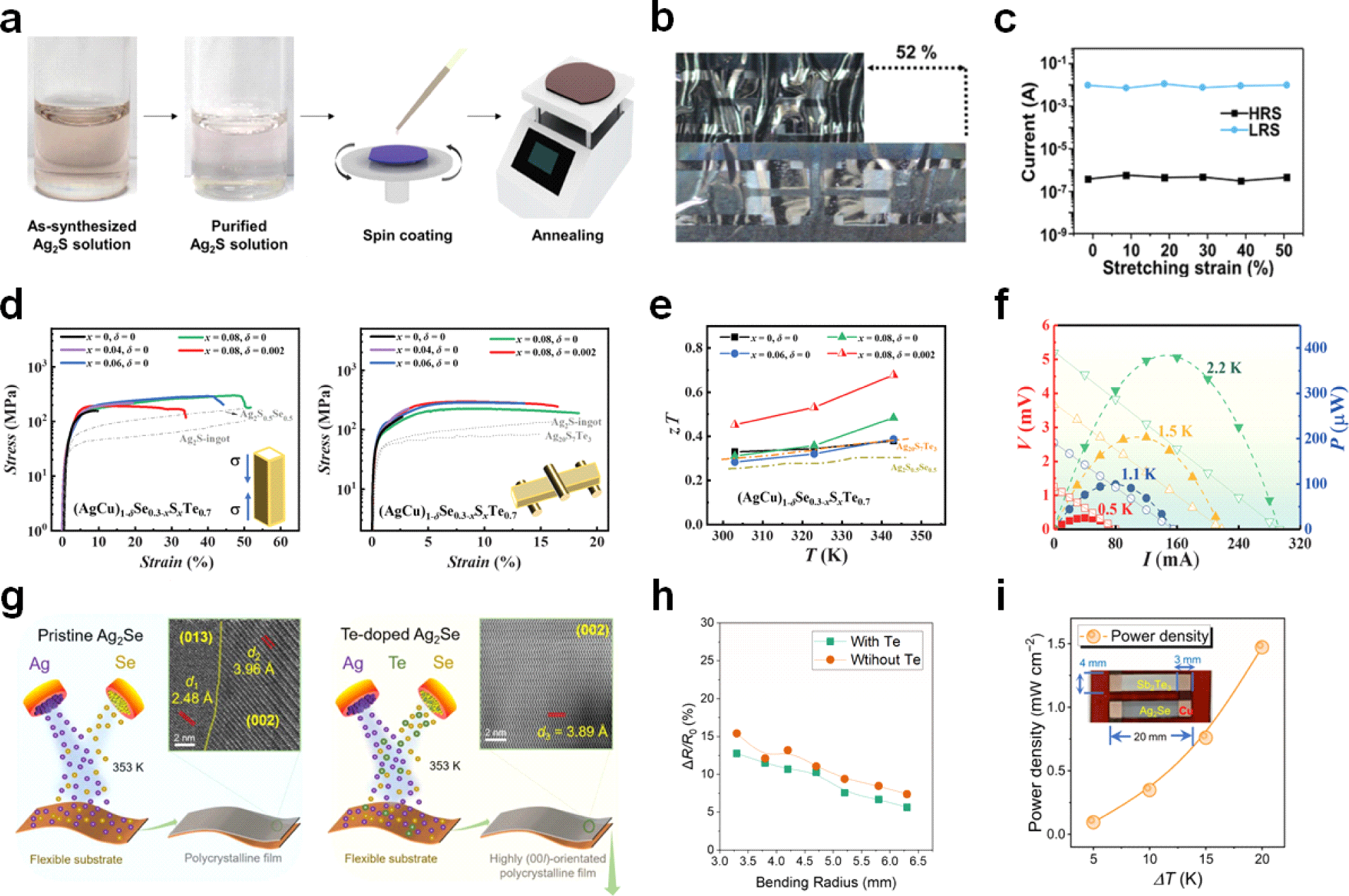
한편 중국 Shanghai Institute of Ceramics의 Lidong Chen 교수의 연구팀은 p타입 무기 열전 물질인 AgCu (Se1−yTey)(0.7≥y≥0.5)에 소량의 S를 합금할 경우 Ag와 S 사이에 추가적인 결합이 생겨 슬립에 유리한 구조로 변화하면서 취성-연성 변이가 발생함을 확인하였다[35]. AgCuSe0.3−xSxTe0.7의 화학적 조성을 가진 합금 소재를 사용하여 압축 시험과 3점 굽힘 시험을 진행한 결과, 각각 최대 약 50%와 18%의 변형률을 기록하였다(Fig. 5(d)). 이는 도핑되지 않은 AgCuSe가 기록한 약 3%의 3점 굽힘 변형률에 비해 월등히 향상된 수치이다. 또한 15 mm의 굽힘 반경으로 500번의 변형 사이클 시험을 거친 결과, 내부 저항의 변화율이 5% 미만으로 유지되어 내구성 면에서도 우수한 소재임을 입증하였다. 300 K의 온도에서 0.45, 340 K에서 0.68의 열전 성능 지수가 측정되었으며(Fig. 5(e)), 이때 열전도도는 0.3∼0.4 W/m·K로, 전통적인 Bi 기반 재료보다 큰 온도 구배를 형성하여 발전에 유리한 것으로 나타났다. 최종적으로 3쌍의 TE 모듈로 구성된 열전 소자를 제작해 평가한 결과, 전력 밀도는 최대 약 30 μW/ cm2·K2로 측정되었다(Fig. 5(f)).
또한 퀸스랜드 공과대학의 Zhi-Gang Chen 교수 연구팀은 Ag2S와 유사하게 고유의 결정구조로 인해 다른 무기 열전 소재에 비해 비교적 높은 기본 연성을 가지고 있는 Ag2Se에(001) 평면의 균일성을 향상해줌으로써 전기전도도의 이점을 가져올 수 있는 Te를 도핑하여(Fig. 5(g)) 연성을 확보하면서 열전 성능을 향상시키는 연구를 진행하였다[36]. 3.2 at.%의 비율로 Te를 도핑한 샘플을 굽힘 시험한 결과, 도핑을 하지 않은 샘플은 내부 저항 증가율이 8%~15.5%로 측정된 반면 Te 도핑이 된 샘플은 내부 저항 증가율이 6~12.5%의 작은 폭으로 억제되었다(Fig. 5(h)). 추가적 유연성 향상을 위해 소재에 고분자(90% poly(vinyl laurate), 10% methylpyrrolidone)를 스핀 코팅한 경우, 굽힘 실험 중 내부 저항 증가율이 약 3% 이하로 유지되었고, 굽힘 반경 6.3 mm에서 1,000번의 굽힘 사이클 후에도 성능 저하가 단 2.5%에 그쳤다. Te가 3.2 at.%로 도핑되었을 때 열전 성능 지수는 약 1.2를 기록하였고, 단일 페어 열전 발전기를 제작해 20 K의 온도 차이에서 1.5 mW/cm2의 전력 밀도를 수확했다(Fig. 5(i)).
이처럼 무기 열전 소재에 다양한 원소를 첨가하는 전략을 이용하여 무기 소재의 취성 극복 가능성을 직간접적으로 입증하였다. 그러나 기계적 변형의 평가가 대부분 굽힘 실험에 한정되어 있고 축 뱡향의 인장 변형까지는 연구에 포함이 되지 않아, 소재의 인장성이 유의미하게 향상되었다고 증명하기에는 아직 한계가 있다. 또한 유기 소재와 같은 탄성 영역, 즉 인장 또는 압축 후 원래 형태를 회복하는 능력에는 아직 미치지 못하며, 또한 실질적인 활용을 위해서는 고유 인장성의 추가 확보가 요구된다.
화학적 변화를 통한 소재의 인장성 및 열전 효율 개선 외에도, 물리적 구조 변형을 통해 인장성을 가진 무기 열전 소재를 개발하는 연구가 활발히 진행되고 있다. 카이스트 정연식 교수 연구팀은 PUA(poly urethane acrylate) 몰드를 사용하여 Bi층과 Te층을 교차적으로 적층한 나노리본을 얀 형태로 꼬아 유연성을 확보하였다(Fig. 6(a))[37]. 이 과정에서 재료의 두께를 수백 나노미터 수준으로 극단적으로 감소시켜 굽힘 파괴에 대한 내구성을 강화하였으며, 나노 구조 간 상호 지탱을 통한 인장성과 열전 소재로서의 성능을 동시에 향상하는 전략을 사용하여 인장성 열전 소재를 제작하였다. 약 0.49 mm의 곡률로 1,000회 굽힘 사이클 후 최대 약 2.3%의 내부 저항 변화율을 보였으며, 축 방향 인장 변형률 약 5%에서 1,000회 인장 사이클 후 최대 약 4.4%의 성능 저하를 보였다. 그러나 축 방향 변형률이 14.5% 이상일 경우 내부 저항비가 초기 값 대비 12.3배로 급격히 증가하고 제벡 계수의 절댓값이 감소하여, 인장성과 열전 성능 모두 감소하는 경향을 나타냈다(Fig. 6(b)). 최종적으로 1줄의 Bi2Te3 얀과 체온을 활용한 웨어러블 열전 소자의 출력 전압을 측정한 결과, 최대 약 13 mV의 전압이 형성되었다(Fig. 6(c)).
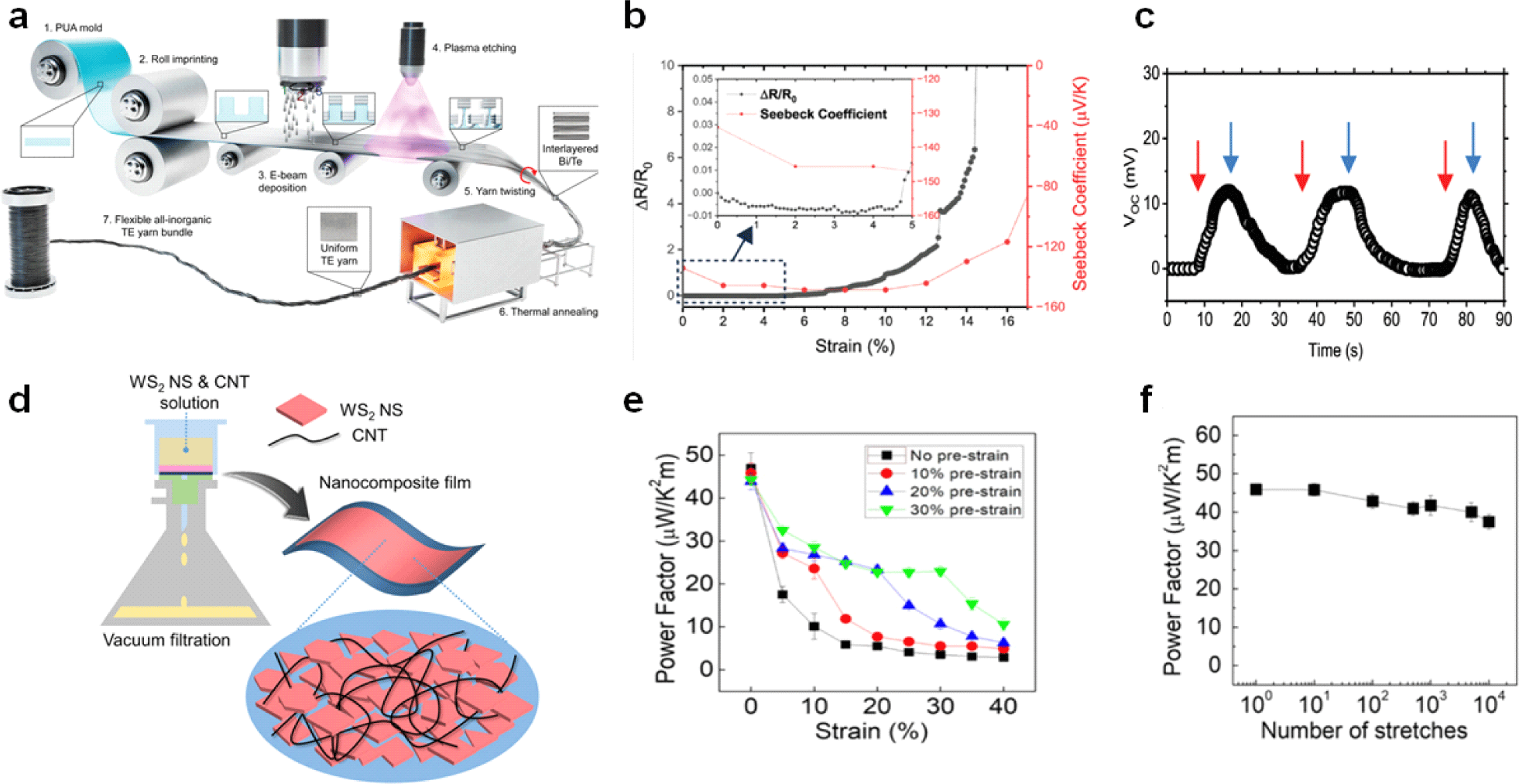
보편적 무기 열전 소재 이외에도 이차원 소재의 적층 구조를 제어하여 신축성을 부여하는 방법도 제시되었다. 가천대학교 이태일 교수 연구팀은 WS2NSs (tungsten sulfide nano sheets)의 전기전도도 향상을 위해 단일벽 탄소나노튜브(single wall carbon nanotube, SWCNT)를 첨가한 용액을 진공 여과하여 신축성 박막을 제작하였다(Fig. 6(d))[38]. WS2NSs는 2D 층상구조 간 약한 반데르발스 힘으로 결합되어 있어 슬립이 쉽게 발생한다는 특징을 가지고 있다. 또한 이를 사전 변형된 PDMS 기판에 직접 전사하여 주름 구조를 통해 열전 소재의 축 방향으로 추가적인 신축성을 부여하는 연구를 진행하였다. 사전 변형이 없을 때 축 방향 인장 변형률 40%에서 약 12%의 비저항 증가율을 보인 반면 사전 변형률이 30%일 때 약 4%의 비저항 증가율을 보였다. 파워 팩터는 최대 약 42 μW/m·K2에서 인장 변형률 증가에 따라 약 10 μW/m·K2까지 감소하는 경향을 나타냈다(Fig. 6(e)). 또한, 30% 인장 변형을 10,000회 인가하는 사이클 실험 후 파워 팩터는 약 46 μW/m·K2에서 약 38 μW/m·K2로 감소하여 변형 내구성의 저하가 두드러지지 않음을 확인할 수 있다(Fig. 6(f)).
이러한 연구들은 재료의 물리적 구조 변형을 통한 무기 열전 소재의 유연성과 인장성을 동시에 향상시키기 위한 소재 차원의 구조 제어 방식을 제시하고 있다. 하지만 무기 열전 소재의 인장 변형률이 일정 수준 이상으로 증가하게 되면 열전 성능이 급감하는 현상을 보여주며, 이는 여전히 무기 소재 고유의 취성으로부터 완전히 자유롭지 못하다는 것을 시사한다. 화학적 조성, 물리적 구조 제어 전략 모두 열전 소재의 유연성 향상에 기여하였으나, 더 높은 변형률에서도 열전 성능이 유지될 수 있는 개선된 전략이 필요하다.
Table 1의 모든 열전 특성과 신축성 수치는 상온(300 K)에서 가장 높은 ZT값을 보였던 실험 조건을 기준으로 작성되었다. 또한 참고문헌 [31]∼참고문헌 [33]의 열전 특성은 이온성 열전 소재를 기준으로 측정된 값이다.
4. 실제 적용 및 과제
신축성 열전 소재는 기존의 열전 소재와 같이 전기-열 간의 쌍방향 변환이 가능하면서도 유연성 및 변형성을 갖추고 있어 다양한 첨단 분야에서 활용될 수 있다. 웨어러블 전자 기기 분야에서는 피부에 밀착하여 다양한 운동 및 변형 환경에도 대응하며 신체와 외부 환경 간의 온도 차에서 전력을 생산하는 에너지 하베스팅 소자로 활용될 수 있다. 예를 들어, 의료용 웨어러블 기기에서 피부에 부착할 수 있는 신축성 열전 센서를 이용해 체온 모니터링 및 건강 데이터 수집 등에 활용할 수 있다. 이외에도 소프트 로보틱스, 스마트 의류, 전자 피부(e-skin) 등의 차세대 기술에도 적용이 가능하다는 이점이 있다.
웨어러블 전자 기기 분야는 특히 신축성 열전 소재의 활용 가능성이 주목받는 영역이다. 하지만, 현재 신축성 열전 소재의 발전 성능은 상용 전력 공급 장치의 완전 대체는 물론, 보조적인 에너지 하베스팅 및 충전 용도로 활용하기에도 아직 충분한 수준에 도달하지 못했다. 이를 확인하기 위해 참고문헌 [35]에 보고된 무기 신축성 열전 소재를 기준으로 상용 충전기와의 발전 성능을 비교하였다. 해당 열전 소자는 PN 레그 3쌍으로 구성되어 있으며, normalized power density 값은 35 μW/cm2K2로 측정되었다. 이때 신체 및 주변 환경과의 온도차를 10 K로 가정하여 계산한 발전 성능은 약 0.0035 W 정도이다. 반면, 웨어러블 전자기기의 통상적인 충전기인 USB-C 타입의 평균 출력은 약 5~30 W로, 두 값 사이에는 상당한 차이가 존재한다. 이는 신축성 TE 소재 및 소자의 열전 성능에 여전히 개선이 필요함을 시사하며, 현재 수준에서는 웨어러블 기기의 보조 전력원으로 활용하는 데에도 다소 한계가 있을 수 있다. 따라서, 실질적인 전력 공급원으로서 실용성을 확보하기 위해서는 소재 최적화를 통한 열전 성능의 향상이 지속적으로 이루어져야 할 것으로 전망한다.
5. 결론 및 전망
본 리뷰 논문에서는 열전 소재의 내재적 신축성을 확보하는 최신 연구 동향에 대해 논의하였다. 전도성 고분자 기반 유기 열전 소재의 복합화를 통한 신축성 극대화부터 무기 열전 소재의 물리/화학적 구조 제어를 통한 연성화 및 새로운 열전 소재의 합성에 이르는 각 전략들의 신축성 향상 정도를 비교 평가하였다. 나아가 각 전략들의 열전 특성 및 기계적 변형에 대한 성능 안정성을 검증하고, 신축성이 향상된 열전 소재를 소자화 하여 다양한 어플리케이션에 적용한 사례들을 살펴보았다.
신축성 열전 소재 연구는 비교적 최근에 이르러서야 본격적으로 주목을 받기 시작한 초기 단계이며, 열전 효율을 향상하는 종래의 소재 연구에 비해 아직 연구의 깊이와 폭이 부족한 편이다. 본문에서 논의된 대부분의 연성화 전략은 여전히 열전 효율의 증대 없이 신축성을 극대화 하거나, 고효율 열전 소재에 제한적인 인장성을 부여하는 공통의 한계점을 지니고 있다. 따라서 소재 열전 효율과 신축성의 상충 관계를 극복할 수 있는 차별화된 연구가 절실하다. 또한 특정 열전 소재의 네트워크나 화학적 조성을 변경하여 내재적 신축성을 달성하는 연성화 전략은 아직 p형 또는 n형 열전 반도체 한가지 타입에 치중된 경우가 대부분이다. 각 타입의 열전 소재가 번갈아 가며 전기적으로 직렬로 연결되어야 하는 열전 소자의 특성 상, 기계적 변형에 대한 안정성을 p형 및 n형 열전 소재 모두에 부여할 수 있는 범용성 전략이 필요하다.
내재적 신축성을 지니는 열전 소재를 개발하는 연구를 조명하는 본 리뷰 논문의 대상에서는 제외되었지만, 열을 회수하고 제어하는 열전 플랫폼의 디자인 및 제작 공정과 같은 소자 차원의 논의 역시 필수적이라 할 수 있다. 먼저 열전 소재의 내재적 신축성 향상은 점진적으로 가공성 및 자유형상성의 확보로 이어져야 한다. 열전 플랫폼은 주로 폐열이 발생하는 열원 상에 부착하는 구동 방식의 특성 상 소자, 수직 방향으로 인가되는 온도 차이에서 에너지를 회수하는 경우가 대부분이다. 따라서 우수한 발전 효율을 위해서는 신축성 열전 소재를 수직 방향으로 적층하거나 성형하는 소재 가공 기술의 개발이 수반되어야 한다. 또한 열전 소재 외에도 신축성 기판, 전극, 배선, 보호층, 히트싱크 등 열전 플랫폼 제작에 핵심적인 구성 요소들의 열 및 기계적 물성 제어와 더불어 제작 공정 연구가 병행되어야 한다. 지난 수십 년간 신축성 전극 및 기판의 연구는 활발히 진행되었지만, 열전 성능 향상을 위해서는 수직 방향의 열전달 및 이방성 열제어에 대한 체계적인 접근이 추가적으로 요구된다. 신축, 비틀기 등의 기계적 변형 인가 시 응력이 열전 소자의 특정 구성 요소 또는 계면에 집중되지 않도록 각 컴포넌트들의 변형성을 조율하고 이를 소자 차원에서 구현할 수 있는 3차원 적층 기술의 개발 역시 중요한 축이라고 할 수 있다. 위와 같은 기술적 난제들을 극복하고 최종적으로 신축성 열전 소재와 소자를 적용할 수 있는 분야 및 사용처를 발굴하려는 노력이 뒷받침된다면, 각종 산업 공정, 발전, 모빌리티 등의 여러 분야에서 지속 가능한 열 에너지 회수에 한걸음 더 가까워질 것이라고 전망한다.