1. 서론
최근 스마트폰은 사용 중에는 펼쳐서 큰 화면을 사용하고 사용하지 않을 경우에는 접어서 작은 크기로 휴대할 수 있는 폴더블(foldable) 스마트폰이 인기를 얻고 있다. 또한, 유연 태양전지, 배터리, 센서 등 다양한 소자들이 접거나 굽힐 수 있는 형태로 개발되고 있다. 이러한 유연 전자 기기를 구성하는 재료 중 금속 배선은 유연 전자기기의 동작과 전기적 연결을 이루는 동작을 위한 가장 기본적인 소재이다. 금속 배선에 굽히고 펴는 기계적 응력이 반복해서 가해질 경우, 금속의 피로 현상에 의해 침입, 압출 및 균열이 발생하게 된다. 이러한 피로 손상은 금속 배선의 전기 저항 증가와 소자의 파괴를 유발하게 된다. 금속 배선의 기계적 신뢰성 문제를 해결하고 고신뢰성을 확보하기 위해 나노홀 금속 배선, 나노포어 잉크젯 배선, 다층 배선 등 다양한 형태의 배선 소재가 연구되었다.
폴더블 스마트폰은 더 나아가 롤러블(rollable), 슬라이딩(sliding), 비틀 수 있는(twisting) 전자기기와 같이 더욱 다양한 형태로 진화할 것으로 예상된다. 이에 따라 유연 전자소자의 다양한 변형을 모사할 수 있는 시험 장비 개발과 이를 이용한 기계적 신뢰성 연구가 중요해지고 있다. 유연 투명전극이 반복 롤링 변형이 가해질 경우, 롤링 바퀴수가 많을수록 취성 균열이 더 많이 발생하여 전기저항 증가가 더 큰 것으로 발표되었다.
롤링 변형에 대한 비틀림 변형이 고정 형태와 자유로운 형태로 가해졌을 경우, 금속 배선에 발생하는 응력 분포를 해석하고 기계적 신뢰성에 대한 연구 결과가 발표되었다. 하지만, 유연 전자기기의 경우 이상적인 형태의 굽히고 펴는 동작 외에 힌지 부분의 불량이나 조립 불량으로 인해 굽힘 변형이 비대칭으로 발생할 수 있으나 이에 대한 연구는 아직까지 발표되지 않았다.
본 연구에서는 비대칭으로 굽힘을 반복적으로 가해줄 수 있는 장치를 개발하였으며, 이를 통해 (1) 곡률이 비대칭으로 가해진 경우, (2) 높이 방향으로 비대칭이 만들어진 경우의 두 경우를 연구하였다. 두 가지 비대칭 조건과 대칭적인 U-bending 조건에서 금속 배선의 전기저항을 실시간으로 측정하여 비교하였으며, 배선의 위치에 따른 전기저항 변화를 측정하고 비대칭 피로 실험 이후에 시편 분석을 통해 피로 파괴 부분을 분석하였다.
전자 기기들은 현재 편의성, 유동성, 휴대성과 같은 다양한 분야에서 연구가 진행되고 있으며 제품화 역량에 대한 평가는 필수적이다. 제품화 역량을 평가하기 위해 반드시 연구되어야 하는 분야들이 있으며 신뢰성에 대한 연구가 그 중 한 분야를 차지한다. 신뢰성 연구란 부품, 소재, 제품이나 시스템 등이 주어진 수명 하에 고장 없이 일정 기간동안 최초의 품질 및 성능을 유지하는 특성에 대해 평가를 실시하여 소비자가 만족하는 제품으로 보증하기 위한 연구를 뜻한다. 유연 디스플레이의 최근 연구 동향은 기존의 단단한 형태에서 유연한 형태로 변화되어 전자기기의 사용 장소가 한 곳에 국한되는 것이 아닌 다양한 상황에 적용할 수 있는 방향으로 변화되고 있다. 이에 따라 다양한 상황에 대한 기계적 변형에 있어서 안정성 실험의 필요성이 강조되고 있으며 안정성 확보를 위해 소재에 있어서 우수한 재료 선정이 필수적이다. 현재 다양한 전자 기기에 기본 소자 재료로 Cu가 있으며, Cu의 경우 전기전도성이 우수하며 기계적 성질이 우수하다. 이러한 특징으로 인해 Cu 소재를 유연 디스플레이용 전극 소재로써 사용이 많이 하고 있으며 전극 소재에서 일어나는 결함으로 피로파괴 현상이 발생한다. 피로 파괴 현상이란 재료가 반복적인 응력 변동에 의해 전위의 비가역적 움직임으로 인해 파괴 강도보다 낮은 응력에서 파괴되는 현상이다. 다양한 기계적 변형 중 현상 발생에 대해 충분한 이해가 필요하며 일반적인 기계적 변형과 더 나아가 비대칭한 경우 전기적 신뢰성 및 기계적 신뢰성에 대한 연구가 필요하다. 본 연구에서는 Cu film의 다양한 비대칭 조건에서의 U-bending 변형 중 전기저항 변화 측정을 통해 전기적 신뢰성을 연구하며, 실험 후 균열 분석을 통해 기계적 변형에 대해 연구하였다. 이 때 시편의 전기저항 증가와 전기적 파괴를 확인할 때 전자제품의 전기적 파괴가 20%를 일반적인 기준으로 하는 점에 근거하여 본 실험의 전기적 파괴도 20%로 결정하였다. 실험 후 주사 전자 현미경(field emission scanning electron, FE-SEM)을 통하여 표면을 관찰하였다.
2. 실험방법
실험에 사용된 기판으로는 125 μm 두께의 폴리이미드(polyimide, PI) 기판 위에 Cu 금속을 500 μm 두께로 진공 증착을 진행한 뒤 Fig. 1(a)에 보이는 이미지와 같이 60 mm×65 mm 크기로 하나의 시편에 3개의 동일 규격 샘플을 같이 실험할 수 있는 구조로 준비하였다. 이후 Fig. 1(b)의 schematic diagram은 curvature asymmetry 실험 시 시편의 모습이며 지그를 통해 고정한 뒤 각각의 샘플을 곡률(r) 값을 θ만큼 차이를 주어 비대칭 형태로 굽힘 실험을 진행하며 실시간으로 전기 저항을 측정하였다. Fig. 1(c)의schematic diagram은 Height asymmetry 실험 모습이며 상단 한 축을 고정하여 θ만큼 회전을 주어 비대칭 형태로 굽힘 실험을 진행하며 실시간 전기저항을 측정하였다. Curvature asymmetry의 경우, 곡률 반경이 균일하지 않고, 굽힘 변형 사이의 간격이 일정하지 않은 경우를 나타내며, Height asymmetry의 경우, 굽힘축이 비틀어진 경우로 굽힘과 비틀림이 동시에 가해진 경우로 가정할 수 있다. 이 때 반복적인 U-bending의 기계적 변형을 주었으며 변형률은 각 Line(1, 2, 3)의 r 값을 기준으로 변형률을 구하였다. 이 때 사용한 식은 곡률 관계를 통해 식 (1)과 같이 표현할 수 있다.
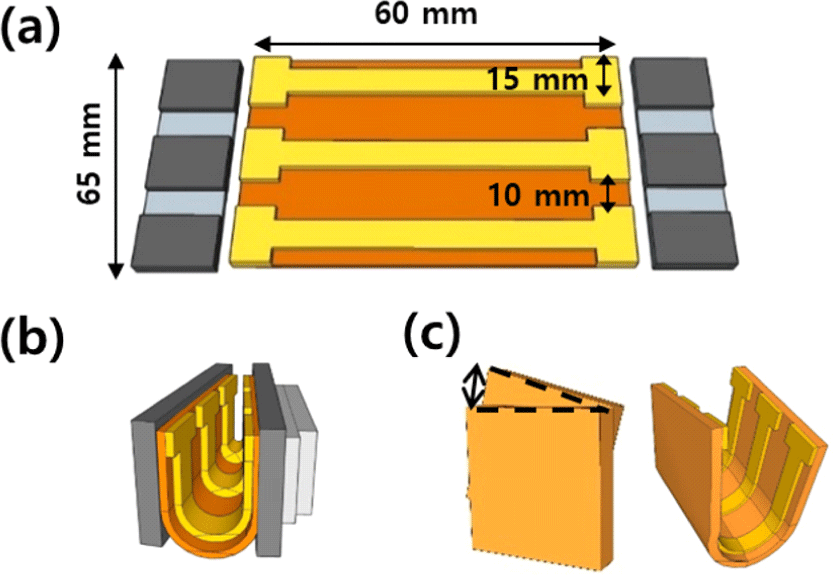
여기서 ε, r, h는 굽힘 변형률, 굽힘 반경, 시편 두께를 의미한다. U-bending 변형을 가하는 10,000 cycle 동안 전기저항 측정 장치(Keithley 2400)를 통해 4-point probe 방법으로 실시간 전기 저항을 측정하였다. 변형률은 Line에 따라 θ값을 다르게 부여하여 1 Hz의 속도로 실시하였다. 실험 후 기계적 변형 동안의 전기저항 변화를 각각 확인하였으며 시편의 Line에 따른 피로파괴 현상을 광학현미경(optical microscopy, OM)을 통해 표면 관찰로 확인하였다. Height asymmetry의 경우 실험 후 FE-SEM을 통하여 표면을 관찰하였다.
3. 결과 및 고찰
Table 1은 비대칭 굽힘 실험에서 각도에 따른 각 Line의 변형률을 나타낸 표이다. Line 1, Line 2, Line 3의 순서(θ=1.76°, θ=3.52°, θ=4.8°, θ=5.3°)에 따라 변형률을 나타냈다. Line에 따라 변형률 값은 다르게 나타났으며 θ각이 증가함에 따라 변형률의 값이 변화하였다. Line 3의 경우 변형률 1.47%로 동일하였으나 Line 2의 경우 변형률이 1.56%에서 2.08%까지 증가하였고 Line 1의 경우 1.78%에서 3.57%까지 가장 크게 변화하는 것을 확인할 수 있었다.
Fig. 2는 Table 1에서 말한 θ값의 변화에 따른 전기저항 변화 그래프이다. 각 시편은 10,000 cycle 동안 비대칭 굽힘 실험 중 실시간으로 전기 저항을 측정하였다. 각 시편의 초기저항은 모두 R。= 0.252 Ω이다. Fig. 2(a)의 이미지는 Line 별 위치와 비대칭 굽힘 실험의 모습을 나타내며, θ=1.76°의 Line 1, 2, 3 전기저항 변화그래프를 보면 초기 cycle에서 전기저항의 변화가 시작되어 100%까지 전기저항 증가폭을 보이며 10,000 cycle 이후 전기저항의 변화가 약 230%까지 증가하는 것을 확인할 수 있다. 이 때 모든 라인의 전기저항 변화폭에 차이가 없는 것이 확인되었다. Fig. 2(b)는 θ= 3.52°에 해당하는 전기 저항 변화 그래프이며 Line 3, 2, 1 순으로 초기 cycle에서 약 10,000 cycle 후 전기 저항의 변화가 230%, 250%, 270% 순으로 전기저항 변화폭이 확인되었다. Fig. 2(c)의 경우 θ=4.8°의 전기저항 변화 그래프로 Line 3, 2, 1 순으로 230%, 500%, 1,600% 순으로 전기저항 변화폭이 확인되었다. 이 때 Line 1의 경우 초기 cycle에서 전기저항 증가폭이 250 %까지 상승하였다. Fig. 2(d)는 θ=5.3°의 전기저항 변화 그래프로 Line 3, 2, 1 순으로 230%, 500%, 6,000% 순으로 전기저항 변화폭이 확인되었다. Line 3과 2의 경우 θ값이 4.8 이후로 차이 효과가 전기저항 측면에서 미비하였으나 Line 1의 경우 초기 cycle에서 증가폭은 θ=4.8°일 때보다 높은 500%였다. Line 1이 가장 낮은 전기저항 변화 그래프를 보였으며, Line 3가 가장 높은 전기저항 변화 그래프를 나타냈다. 이는 비대칭 굽힘 실험에서 θ 값에 따라 Line 1이 가장 높은 변형률 조건이며 Line 3가 가장 낮은 변형률 조건에서 실험이 진행되어 나타난 결과이다.
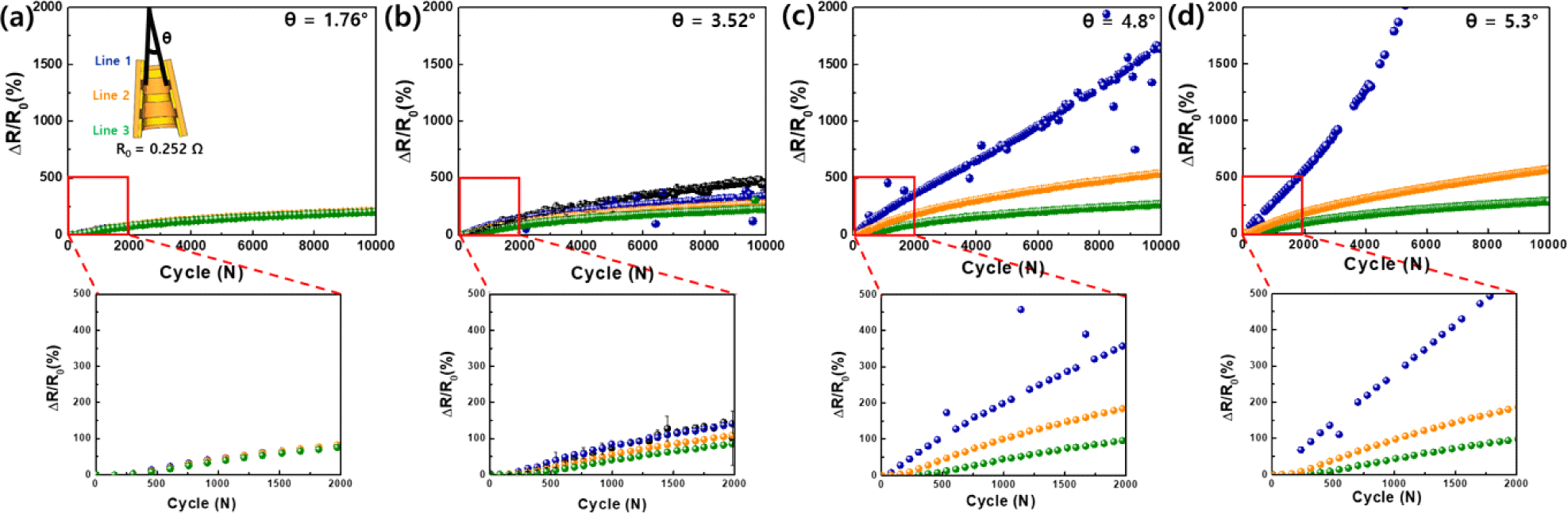
Fig. 3은 실험에서 전기저항 변화가 100%에 도달하기까지의 cycle 수를 나타낸 그래프이다. 변형률이 감소할수록 100%에 도달하는데 진행한 cycle 수가 증가하는 것이 확인되었다. 피로 수명 주기를 정량적으로 분석하기 위해 Coffin-Manson equation을 이용하였다.
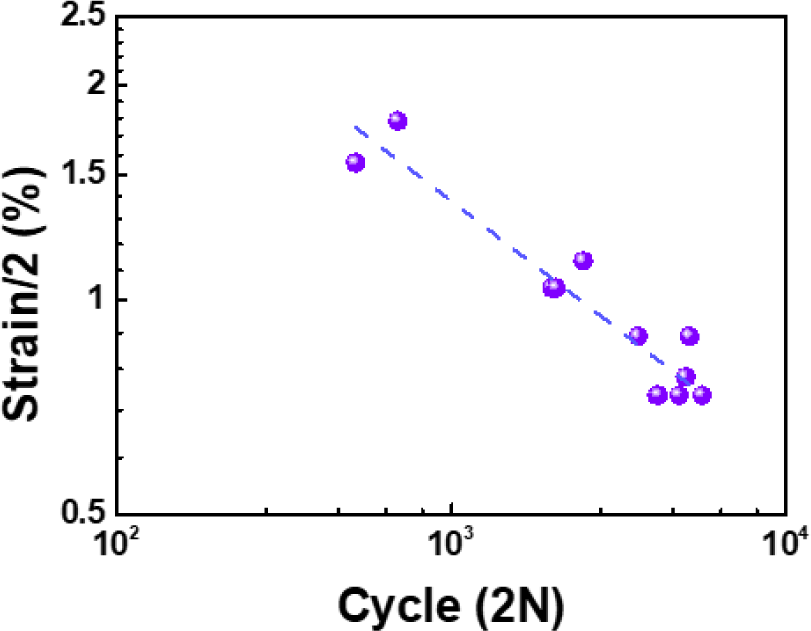
식 (2)에서 εf’는 피로 연성 계수를, c는 피로 연성 지수를 의미한다. Fig. 3의 log-log 그래프를 통하여 εf’= 0.167, c=0.361을 얻을 수 있다.
Fig. 4(a)는 각도에 따른 높이 비대칭 굽힘 실험 모습이며, Fig. 4(b)∼Fig. 4(d)는 각도에 따른 높이 비대칭 실험의 전기저항 그래프이다. 각 시편은 10,000 cycle 동안 비대칭 굽힘 실험 중 실시간으로 전기 저항을 측정하였다. Fig. 3(b)는 symmetrical line에 대한 전기저항 그래프로 약 440 cycle에서 전자제품의 전기적 파괴도인 20%까지 전기저항 변화가 측정되었다.
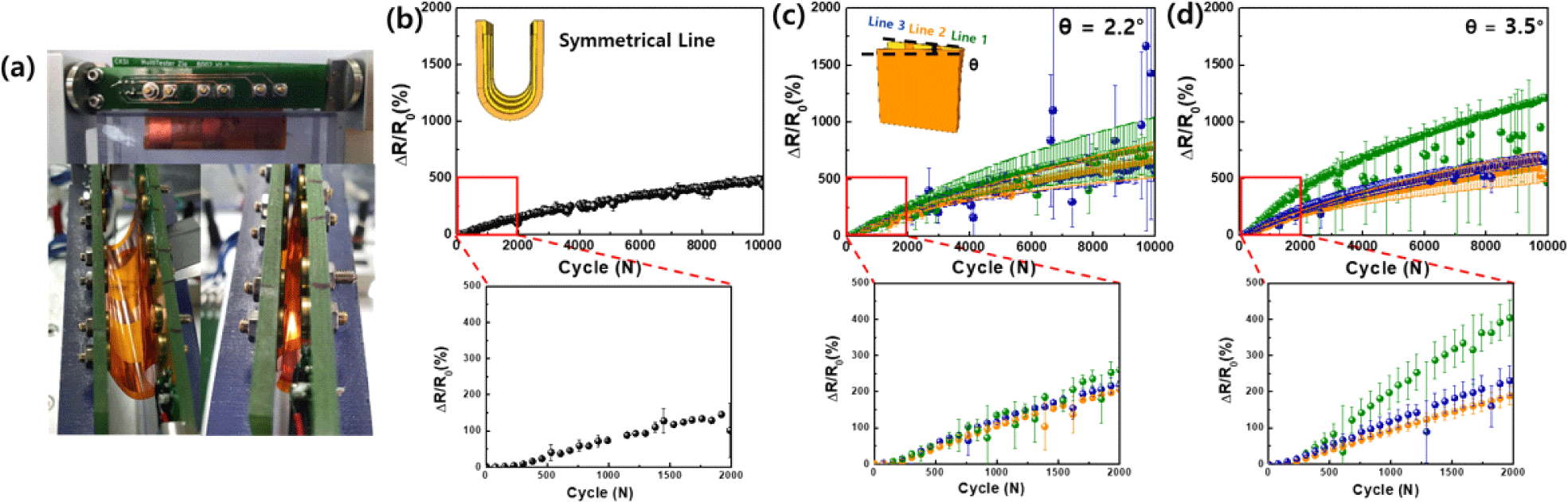
Fig. 4(c)는 θ=2.2°의 조건에서 높이 비대칭 굽힘 실험의 전기저항 그래프이며, Line 3, 2, 1 전부 전기저항이 약 700%까지 상승하였다. Fig.4(d)는 θ=3.5°의 조건에서의 전기저항 변화 그래프로 Line 3, 2, 1순으로 초기 cycle에서 약 10,000 cycle까지 진행 후 전기저항의 변화가 400%, 500%, 1,300% 순으로 변화 폭이 확인되었다. Line 1의 경우 초기 cycle에서 증가폭이 다른 Line 2, 3에 비해 약 700% 높게 나타났다. 이는 각도별 비대칭 굽힘 시험과 같이 Line에 부여되는 변형률이 커질수록 전기저항 증가폭이 큰 모습이 관측되어 높이 비대칭 실험의 결과 또한 비슷한 양상이 나타났다.
Fig. 5(a)는 높이 비대칭 굽힘 실험 후 Line별 균열 범위를 나타낸 이미지이다. Line 3, 2, 1 순으로 균열 범위가 다른 양상이 나타났으며 Line에 따라 높은 변형률로 인해 굽힘부 이외에도 A, B, C 영역에 균열의 범위가 나타나는 것이 확인되었다. Fig. 5(b)는 높이 비대칭 굽힘 실험 후 Line별 시편의 표면을 보여준다. A, B, C 영역의 Line 3, 2, 1 균열 이미지로 가장 낮은 변형률을 통한 굽힘 실험이 진행된 Line 3의 경우 굽힘 실험이 진행되는 A영역과 실험을 통해 지그로 고정시키는 C영역에서 반복 응력이 가해지고 그로 인하여 균열이 열리고 닫히게 되면서 침입과 압출의 파괴가 발생하여 균열이 관찰되었다. B영역에서는 표면에 균열과 같은 기계적 파괴 변화가 확인되지 않았다. Line 2의 경우 Line 3과 A영역와 C영역에 있어 더욱 큰 침입과 압출이 나타났으며, B영역에서도 동일하게 관찰되었다. 가장 높은 변형률을 통한 굽힘 실험이 진행된 Line 1의 경우 A, B, C영역에서 반복응력으로 인해 파괴가 관찰되었다. 종합적으로 Line 3에서 C 부분의 균열 범위가 다른 Line 들에 비해 낮은 것이 확인되었으며, Line 3, 2, 1 모두 A 영역에서 균열 범위와 밀도 차이에서 큰 차이가 나타나지 않았다. 마지막으로 곡률 비대칭의 경우 θ 값이 클수록 Line에 대한 변형률도 증가해 굽힘 실험 시 균열의 밀도 증가로 인해 전기저항의 급속한 변화가 발생하였고, 높이 비대칭의 경우 상단 한 축을 기준으로 회전을 주어 높이 차를 주었을 때, Line 3에서 접촉면의 발생으로 인한 전기저항의 급속한 증가가 나타난 것으로 확인되었다.
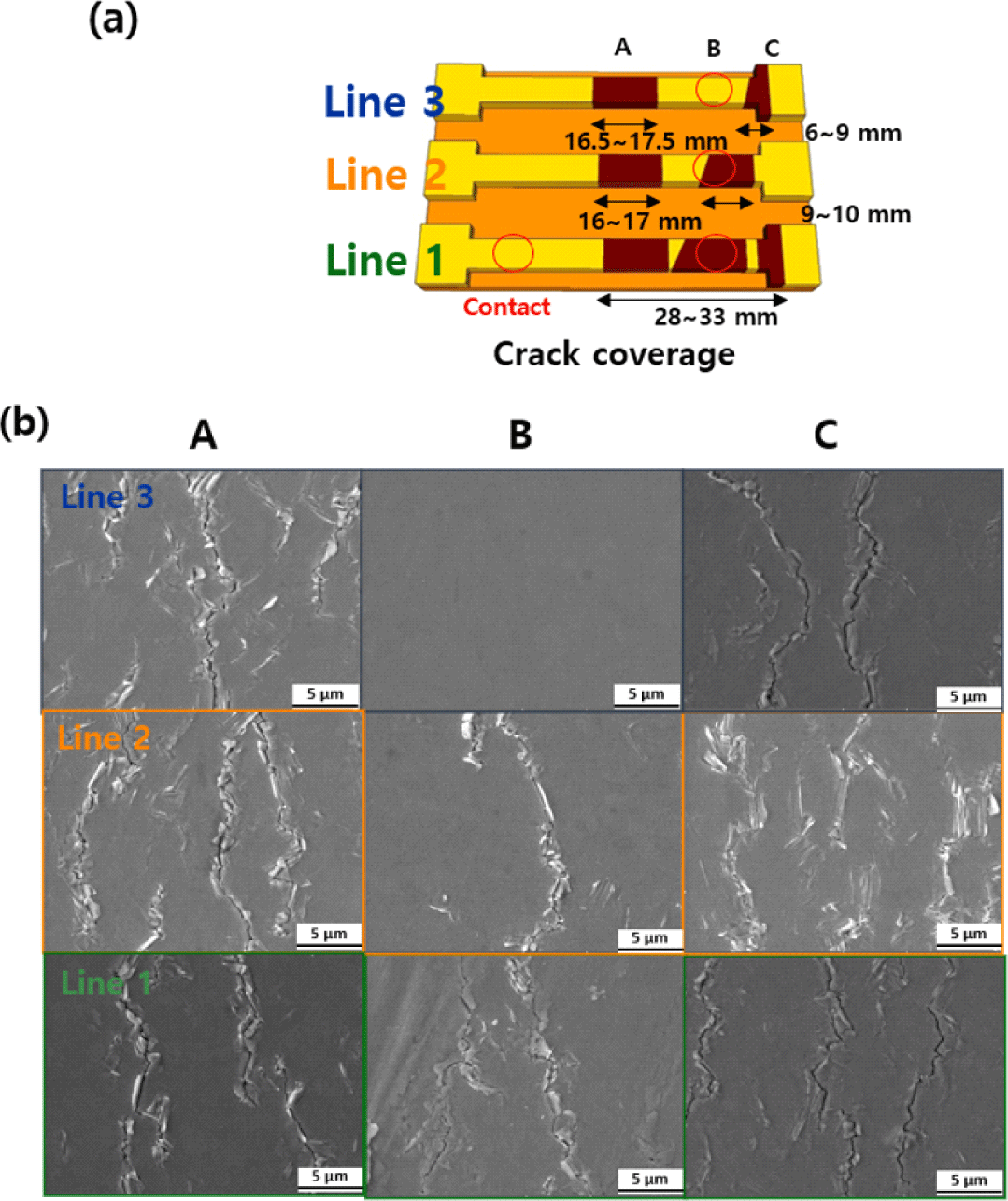
4. 결론
유연 디스플레이용 배선 및 전극 소재의 기계적 변형에 따른 전기적 신뢰성에 대한 연구를 진행하였다. Cu를 폴리이미드 기판에 진공 증착 후 곡률 비대칭 조건과 높이 비대칭 조건에서 U-bending test를 통한 기계적 변형을 받는 조건을 실험하였다. 위 실험 진행 중 cycle에 따른 전기저항 변화를 실시간으로 관찰하였다. 곡률 비대칭 조건에 따라 시편의 Line별 전기저항의 차이가 나타났다. 가장 큰 θ값을 가지는 Line의 경우 전기저항 변화가 크게 증가하며, 상대적으로 θ값이 낮은 경우 전기저항 변화가 소폭 증가하였다. 높이 차 비대칭 조건 실험의 경우 높이 차이가 없는 Symmetrical Line과 비교하여 θ값이 증가함에 따라 Line별 전기저항의 변화가 증가되는 차이가 나타났다. 이는 표면 분석을 통해 균열의 밀도와 크기가 θ값이 증가함에 따라 다른 양상이 나타난 것이 확인되었다. 가장 큰 변형률의 영향을 받은 Line의 경우 A, B, C 구간 전체적으로 균열 양상이 나타났으며, 가장 작은 변형률의 영향을 받은 경우 A, C 구간에서만 균열이 나타남이 확인되었다. 본 연구를 통해서 유연 디스플레이용 소재의 비대칭 조건에서의 기계적 변형에 대한 신뢰성 향상에 가이드 라인이 될 것으로 기대한다. 예를 들어 실제 제품화된 폴더블 스마트폰 및 노트북의 경우 힌지 부분에 변형이 가해져서 불균일한 굽힘 변형이 발생할 경우, 수명이 급격하게 줄어드는 현상에 대한 해석에 도움이 될 것으로 기대한다.