1. 서론
최근 항공우주 산업에서 3D 프린팅 기술 중 금속 프린팅 기술이 주요 연구분야로 주목받고 있다[1-9]. 항공우주 산업에서는 주로 material extrusion(ME), powder bed fusion(PBF), direct energy deposition (DED) 공정이 활용되며, 그중 PBF 공정은 파우더를 빌드 플레이트 위에 얇게 도포한 후 레이저를 이용하여 용융 및 적층하는 기술이다. PBF 공정은 다른 방식과 비교하여 우수한 표면 조도를 제공하며, 내부 격자 구조를 적용할 수 있어 경량화된 제품 제작 및 복잡한 형상의 구현에 적합하다.
플로우 디바이더는 유체의 전달에 있어 가장 필수적인 부품이며, 기존까지의 공정인 절삭, 용접, 주조와 같은 공정으로 제작된 부품은 제작할 수 있는 형상의 명백한 한계가 존재하며, 이로 인한 유체분배의 균일성이 이루어지지 않거나, 유체분배에서의 저항이 발생한다.
플로우 디바이더에 3D 프린팅 기술을 적용하면 재료 낭비를 줄이는 동시에 경량화 된 부품 제작과 공정비용 절감 효과를 기대할 수 있다.
본 연구에서는 Comsol Multiphysics를 사용한 해석[10-15]을 기반으로 플로우 디바이더의 최적 설계를 진행하였으며[16-19], 최종 설계를 구현하기 위하여 3D 프린팅 공정을 이용하였다. 공정을 이용함에 앞서, 실제 부품 적용에 성능을 확인하기 위하여 Ti64[20], 소재의 형상 치수 정밀도, 인장강도, 표면조도를 측정하여 성능을 확인하고 실험 플로우 디바이더를 제작하였다. 마지막으로 CFD의 데이터와 실제 플로우 디바이더의 데이터를 비교하여 시뮬레이션을 활용한 설계의 신뢰성을 검증하였다.
2. 설계 및 실험
본 논문에서 플로우 디바이더 설계 및 분석을 위해 전산유체역학(computational fluid dynamics, CFD)을 사용하였다. CFD 프로그램으로는 COMSOL Multiphysics 외 Open FOAM, Fluent 등이 널리 사용되며, 본 연구에서 사용된 CFD 시뮬레이션은 한국전자통신연구원(ETRI)의 양용석 박사 연구팀에서 제공한 프로그램을 사용하였으며, CFD는 지속적으로 유체가 흐르고 있는 상온 환경에서의 물이 흐르는 환경으로 설정하여 수행되었다. 설계검증을 위하여 유입구와 유출구의 위치를 기존 공정으로 제작된 형상과 동일하게 설정하였으며, 이를 통해 기존 형상과 새롭게 최적화된 형상의 유량 분배 특성을 비교 분석하였다.
COMSOL 시뮬레이션에서 사용된 첫 번째 방정식인 Navier-Stokes 방정식은 뉴턴의 제2법칙 F=ma를 기반으로 도출된 방정식이다. 이 방정식은 유체의 연속성과 운동을 기술하기 위해 적용되는 대표적인 수학적 표현이다. 본 시뮬레이션에서는 비압축성 유체의 정상상태 해석을 기반으로 수식을 설정하였다.
일반적인 형태의 Navier-Stokes 방정식은 식 (1)과 같다
여기서 ρ는 유체의 밀도, u는 속도 벡터, t는 시간, p는 압력, μ는 동점도 계수, F는 외부에서 작용하는 힘이다.
이 식을 정상상태를 기준으로 단순화하였을 때 식의 형태는 식 (2)와 같다.
이를 더 단순화한 식의 형태는 식 (3)과 같다.
여기서, K=μ(∇u+(∇u)T)는 점성 텐서를 나타낸다.
COMSOL 시뮬레이션에서는 이 방정식을 기반으로 안정적인 유체 흐름과 정상 상태의 운동을 해석하였다. 또한 μ=0 조건을 포함하여 유체가 배관 내부의 벽 방향인 수직 방향으로 흐르지 않는 상태를 가정함으로써 계산을 간소화하였다.
μ는 점성 계수로, 이는 유체의 점성을 나타낸 다. ∇u는 속도 변화율로, 유체 내부에서 속도의 변화를 나타낸다. (∇u)T는 유체 내부의 마찰로 인해 발생하는 점성력을 의미한다. ∇⋅u=0은 측정 구간 내에서 유체의 압축성이 없고 속도의 변화가 없음을 나타낸다.
본 해석에서는 플로우 디바이더의 내부 배관에서의 흐름을 확인하기 위해 배관 내부 유체의 흐름 방향과 수직 방향인 외벽 조건을 식 (4)와 같이 설정하였다.
이 식은 관내 유동의 No-slip condition을 나타내는 조건으로 배관 벽면 근처에서의 유체 입자가 표면과 같은 속도를 가지게 되어 속도가 0에 가까워지는 것을 의미한다.
이는 유체와 고체의 상호작용 중 점성효과로 발생하는 현상을 예측하기 위하여 중요한 요인이다.
본 해석에서 유입구와 유출구의 조건은 유체 흐름 데이터를 도출하기 위한 핵심 요소로 작용한다.
특히, 유입구 조건은 식 (5)로 정의되며, 다음과 같다.
유출구 조건은 식 (6)과 같다.
여기서 n은 유체의 방향벡터를 T는 벡터의 전치를 의미하며 −pI는 압력, K는 점성을 나타낸다 μ는 유체의 속도를, t는 유입구 경계 표면에 대한 방향 벡터를 나타낸다.
이 조건은 유체가 유입구에서 경계 표면의 벡터방향이 아닌 배관의 내벽방향으로 흐르지 않음을 의미한다.
p0, 는 유입구 평면에서의 외부 압력을 나타낸다. 방정식을 기반으로 플로우 디바이더의 최적설계를 다음과 같은 방법으로 진행하였다.
먼저 기존 공정으로 만들어지는 플로우 디바이더와 같은 위치의 유입구 및 유출구를 설정하여 형상 차이에 의한 성능 개선을 추구하였다. 다음으로 곡률 변수를 2개로 설정하였으며, 곡률변수는 유출구 A,D로 향하는 배관의 이동거리와 비슷하도록 하며, 유체의 이동 중 가속을 발생하게 하여 A,D와 전체적인 유량 분배를 균일하게 할 수 있도록 기여하였다.
위 식들을 기반으로 CFD 변수를 조정하며 설계결과를 확인하였다(Fig. 1).

성능의 최적 설계를 위하여 각 변수의 수를 변경하며, CFD 결과를 측정하였다(Fig. 2).
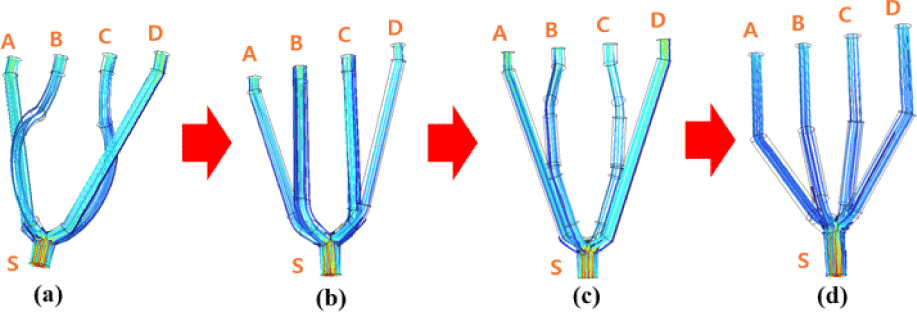
측정한 결과를 바탕으로 가장 최적의 결과를 확인하기 위하여 각 모델의 최적 결과를 그래프로 비교하며 설계를 진행하였다(Fig. 3).
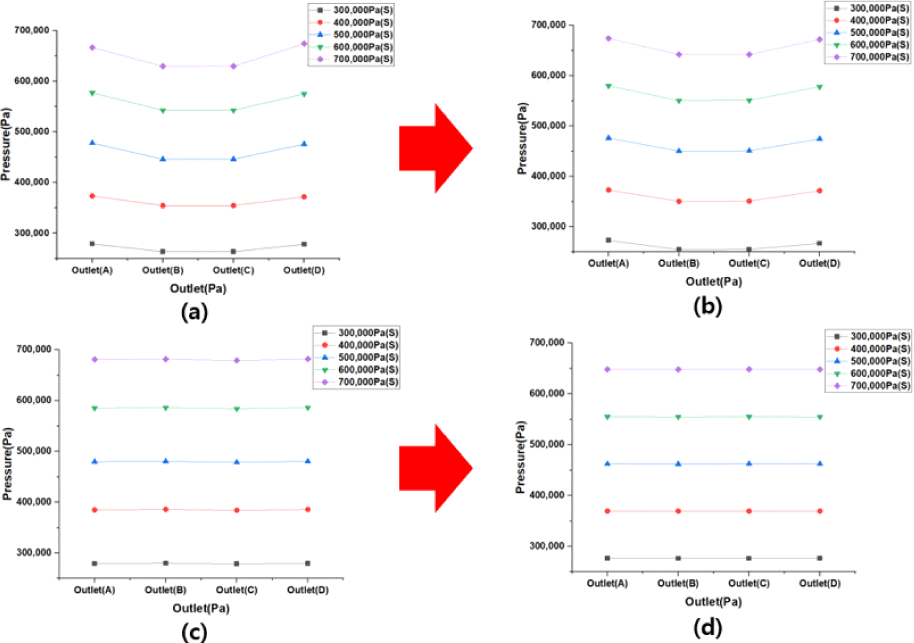
PBF 공법은 주로 기하학적 형상, 내부의 복잡한 구조를 가진 부품 제작, 다양한 부품의 간소화 등 부품의 단순화, 경량화, 효율 개선의 목적으로 많이 사용된다.
플로우 디바이더를 본격적으로 제작하기에 앞서, ASTM E8 subsize 인장시편을 제작하였다
인장강도 측정을 통해 실제 사용에 있어 유체의 압력이 높은 환경에서도 충분한 성능을 낼 수 있는지 확인하였다.
아래 결과를 바탕으로 실제 금속 대비 3D 프린팅된 출력물이 약 85%의 성능을 보이는 것을 확인하였다. (Fig. 4).
출력함에 앞서 출력 정밀도가 높을수록 설계와의 오차가 적게 발생하므로 스케일바를 제작하였고, 각 부위를 측정하여 출력의 정밀도를 측정하였다(Fig. 5).
측정 결과, 설계도면과의 오차가 0~0.2%로 기하학적 형상을 띈 플로우 디바이더의 형상을 설계와의 오차가 충분히 적게 출력할 수 있는 높은 치수 정밀도를 보였다.
이를 바탕으로 플로우 디바이더를 제작하였다(Table 1).
스케일바의 표면조도를 측정하였다. 플로우 디바이더 내부의 표면조도는 유체의 흐름에 있어 점성에 의한 속도변화에 영향을 미치며, 거친 표면 조도일수록 표면에서의 마찰, 표면장력 등에 의한 저항이 발생하기 쉽다.
측정된 Ti64 스케일바의 평균 표면 조도(Ra)는 5.23μ로 준수한 표면조도를 보이며, 이를 통해 플로우 디바이더 내부의 마찰에 의한 저항이 매우 적음을 확인하였다(Fig. 6).
위 측정결과를 바탕으로 (주)Prototech에서 Truprint 3,000장비를 활용하여 최적설계한 플로우 디바이더를 다음과 같은 설정값으로 제작하였다(Table 2).
Laser power | Scan speed | Hatching distance | Layer thickness | Powder size |
---|---|---|---|---|
300 W | 1,500 mm/s | 0.09 mm | 30 μm | 40 μm |
COMSOL 시뮬레이션으로 측정한 성능 데이터와 제작한 플로우 디바이더의 데이터를 비교하였다(Table 3 및 Table 4).
최종적으로 제작한 3D 프린팅 플로우 디바이더는 시뮬레이션과 유사한 균일한 압력 분포를 보였으며, 이를 통해 시뮬레이션이 제품에서의 성능을 정확하게 예측할 수 있음을 검증하였다. 또한, 시뮬레이션을 바탕으로 기하학적 설계나 부품의 단순화를 통해 기존 공정보다 내구성 및 성능이 뛰어난 부품을 제작할 수 있음을 입증하였다.
3. 결론
본 연구에서는 COMSOL Multiphysics 프로그램 을 활용하여 최적설계를 진행한 플로우 디바이더를 PBF 공정을 이용해 제작하였다.
그리고 CFD와 제품의 성능을 비교함으로써 설계의 신뢰성을 검증하였다. CFD를 활용한 결과, 기존 공정 방식의 플로우 디바이더보다 최적설계를 진행한 플로우 디바이더가 우수한 유체 분배 성능을 보여주었다.
PBF 공정으로 플로우 디바이더를 제작하기 위해 Ti64 소재의 기계적 물성치와 출력시의 치수정밀도를 측정하였다. 제작된 시편은 0%에서 0.2%의 오차를 보였고, 실제 절삭 공정으로 제작된 Ti64 소재의 약 85%에 해당하는 기계적 물성치를 확인하였다. 이를 바탕으로 우주 환경에서 사용가능한 플로우 디바이더를 제작하였다. 제작된 플로우 디바이더는 시뮬레이션과 동일한 양상인 개선된 유체 분배를 보였다.
본 연구는 시뮬레이션을 통한 최적설계를 진행하여 부품의 성능을 개선하고, 3D 프린팅을 활용한 부품 간소화 및 제작이 가능함을 증명하였다. 또한 이 연구를 기반으로 하여 항공우주 산업뿐만 아니라 다양한 부품과 장비에 적용하여 실제 부품들을 개선할 수 있음을 입증하였다.